12 Months See's Dozen's of Changes at Unicut
14 November 2012
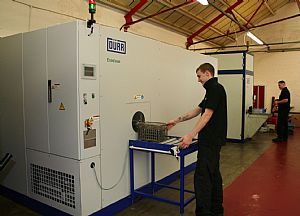
The investment levels at Unicut Precision have grown yet again as the company has spent £1.2m in the 12 months of 2012. The bold investment strategy has paid dividends for the Welwyn Garden City subcontractor with 25% growth in 2012, contributing to the doubling of the company's turnover in just two years.
The acquisition of four new machine tools, component cleaning plant, the building of a dedicated dispatch department and investment in inventory control software has reaped rewards for Unicut and the local economy, with the company's headcount growing by 25% from 33 staff in January to its current level of 41.
The investment strategy has maintained the success at the forward thinking subcontract business with the arrival of a Miyano ABX64-SYY twin turret turning centre in January. The acquisition of the Miyano was to create a dedicated production cell for hydraulic power components that could duplicate the capabilities of existing machine tools for a long term customer. This commitment was extended through June & July when the company acquired two Citizen A20 S sliding head turning centres to accommodate capacity requirements on the company's aerospace work.
Commenting on these three acquisitions, Unicut Precision's Sales Director, Mr Stuart Lawson comments: "Our business is built upon investing in technology and staff to deliver the 'Perfect Manufacturing Environment'. This encompasses manufacturing complete parts and assemblies that can be packaged and delivered to JIT schedules with unsurpassed quality levels. To provide this level of confidence for end users, we invest in machine tools 'two at a time', so if one machine incurs unforeseen downtime, the customer can rest assured that we have the capacity to complete any job to the required schedule. This strategy provides customers with confidence in our service and this has won us significant Long Term Agreements (LTA's) from a multitude of prestigious manufacturers."
However, Unicut has gone beyond the 'two by two' approach in 2012, updating its plant list with a 'like for like' replacement of an aging Citizen M32 sliding head turning centre - a clear indication of the company's commitment to technology. The new Citizen M32 that arrived in September 2012, incorporates new servo drives for faster rapids plus enhanced software and tooling configurations to improve productivity by 25% compared to its predecessor.
September proved a busy month for Unicut, as the installation of the Citizen M32 coincided with an £150,000 investment in a Durr EcoClean cleaning plant and the completion of the company's new dispatch department. The Durr EcoClean 3 tank aqueous system incorporates a washing, rinsing and passivation station that enables Unicut to maintain in-house control of processes that were previously subcontracted out. With machine tools running both soluble coolants and neat oils, the existing Durr system at Unicut was only suitable for cleaning components machined with neat oils. This resulted in the stainless steel components undergoing the passivation stage externally. The Durr acquisition is an investment for Unicut in process control and stability that will further reduce lead times and enhance the company's 'lean' credentials.
The Durr arrival is part of a wider strategy to create an efficient through-flow for the 1.3million components the company produces each month. To this end, the Durr system has been located adjacent to a newly built dispatch department that incorporates three separate stages. Firstly, the parts are bagged and labelled before being boxed and wrapped. Finally , the components are held in a goods-out area to await dispatch to the customer.
As Mr Lawson continues: "Producing 1.3million parts a month, we have to run a pretty slick operation. The new dispatch department has its own dedicated staff that can guarantee the efficient and timely dispatch of parts to the allocated schedule. This schedule for each job is tightly controlled from goods in through production, inspection, assembly, cleaning, packaging and dispatch, credit to our investment in PSL Datatrack software. The through flow of each job can be followed on large screens and desk top PC's that we have installed throughout the facility. The next step for Unicut is to build upon the investment levels of 2012 to take our business and that of our customers to the next level."