AA Tools up with new Mitsubishi
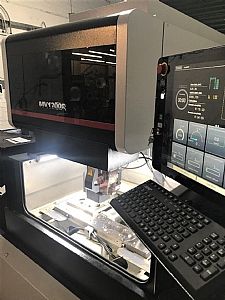
When long-established cutting tool manufacturer AA Tools was acquired by new owners in 2014, the objective was to modernise the shop floor equipment with the very latest CNC machine tool technology. For the bespoke cutting tool manufacturer, the acquisition trail included a CNC tool and cutter grinder, a 4th-axis machining centre, a live tooling turning centre, an EDM drilling machine and a Mitsubishi MV1200R wire EDM machine from the Engineering Technology Group (ETG).
Located in Sheffield, AA Tools has specialised in bespoke cutting tool solutions since its inception more than 35 years ago. The company manufactures PCD, solid and brazed carbide cutting tools, special tooling, magnetic drills and hot tap cutters, construction tools and wear parts as well as offering a subcontract machining service for the aerospace, offshore, automotive and general manufacturing sectors. Producing and re-grinding hundreds of bespoke cutting tools every month, AA Tools was witnessing a shop floor bottleneck with its optical grinding. This bottleneck was compounded by the fact that the nine-employee company could not find the skill set in the local area to add to its department. The company directors investigated possible solutions, and wire EDM proved a best-fit option.
Following extensive market research, demonstrations and trials, AA Tools opted for the Mitsubishi MV1200R wire EDM machine from ETG. Recalling the process, Business Development Director, Mr Chris Birt says: “We use our optical grinder for profiling, tip shaping and brazed carbide production, which meant the machine and operator were overloaded and it was a pinch point in our business. We reviewed a number of machines and as a newcomer to EDM and a company looking to buy our first EDM machine, the demonstration from ETG’s Scott Elsmere really hit the spot. Scott gave us a complete demonstration that emphasised the remarkable ease of use of the Mitsubishi machines. Furthermore, Mitsubishi EDM machines were recommended by some of our customers and also other machine tool suppliers.”
AA Tools installed the Mitsubishi MV1200R with its 400 by 300 by 220mm X, Y and Z-axis travel facility and its taper angle of 15/200 degree to workpiece ratio at the tail end of 2020. The machine has since eradicated the optical grinding bottleneck and reduced lead times on special tools by more than 50%. Discussing this, Chris continues: “With the Mitsubishi MV1200R we can undertake the profiling and shaping tasks that were once only possible on the optical grinder, but moreover, we can modify and manufacture tools and take on new work that wasn’t previously possible. The Mitsubishi machine has also presented new opportunities beyond the scope of cutting tools, such as the manufacture of bespoke jigs and fixtures. It has also reduced operations and costs for our business. Just one example would be the grinding of a steel tool body with carbide tips. The operator would have to change grinding wheels multiple times for the different materials and profiles whereas the EDM machine will precisely cut its profile regardless of material.”
Alluding to the ETG demonstration and ease of use, Production Director at AA Tools, Mr Adam Wood adds: “For a company with no EDM experience, we found the demonstration and the user interface very easy-to-use and quite familiar for our machine operators. Despite being a 2D process rather than 3D machining, the Mitsubishi software interface presented a familiarity that has shortened the learning curve for our team. We now have three staff members capable of using the machine as opposed to just one optical grinding operator. This also enables us to schedule our work more effectively. We can also easily import DXF files and rapidly set up repeat jobs with ease. It's so easy to use, we already have an 18-year-old apprentice working on the machine. Additionally, there is an excellent Mitsubishi online resource library of videos to guide users through everything from operation to simple maintenance tasks.”
From a shop floor perspective, the Mitsubishi MV1200R has an open work area that is more accessible than alternate machines, as Adam continues: “The machine is very spacious, it’s easy to access and the worktable is accessible from all four sides, unlike competitor machines. This means that we have extra space for setting up jigs and fixtures and it enables us to get jobs through the shop floor faster. One example is a set of components that we manufacture for the typesetting industry. Produced in regular batches from 50 to 1000-off that require special form ground wheels, we moved the job to the EDM machine and reduced the lead time from 2 to 3 weeks to just one week. Additionally, we have three machinists that can set the EDM machine and it can also be left to run unmanned overnight – meaning that our team can move on to other jobs, creating greater efficiency for our business.”
“We also have some jobs that used to require 3 to 4 set-ups on our machining centres and some of these have also been moved to the Mitsubishi MV1200R. The result is reduced set-ups, reduced operator intervention and overnight unmanned machining. From a surface finish and precision perspective, we can rough cut relatively quickly with precision levels of 10 microns whereas some parts, cutting tools and inserts that demand a better finish can be processed to a finish of Ra0.3 This eliminates secondary grinding operations.”
Concluding on the acquisition, Chris says: “As a business, we are delighted with the new machine. It has reduced our lead times, significantly improved productivity, relieved a bottleneck within our business and the ease-of-use now gives our shop floor much more flexibility. Added to this, we are winning a lot of new business in areas previously outside our scope. From a service perspective, ETG has been fantastic. Their expertise, understanding of our business needs and supporting those needs has been first class.”