Accuracy in the Micron Realm
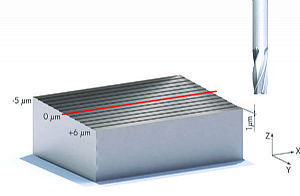
Miniaturization of tools and cutting sizes, faster machining speeds and contact sensitive coatings, provide an ever-increasing challenge in terms of tool monitoring. As a result, machines used for micro manufacturing now feature almost exclusively non-contact laser measuring systems, since they are the only way to detect and compensate for all factors influencing tools while machining.
An important aspect to consider when choosing the right tool monitoring system is to ensure that it can demonstrate absolute accuracy in the harsh conditions of a machining center.
The accuracy of a laser measuring system is defined by its repeatability and by its absolute measuring accuracy. For the user, the latter is more important since it defines how precise the measured results are when workpieces with extremely diverse characteristics are measured. The reason for this lies in the functioning principle of the system. Simply put, a laser measuring system uses a light barrier that operates as a simple switch. When a rotating tool breaks the beam, a skip signal is generated and transmitted to the control to record the machine axis positions. Standard software integrated into the machine control compares a calibrated reference value to the tools measured values and then calculates the tool length and radius and automatically enters this data in the tool table.
Absolute accuracy is crucial
No matter the brand of laser, a skip signal is only generated after a certain percentage of the beam is shaded. For this reason, when measuring tools with varying characteristics (e.g. diameter, shape, cutting radius etc.) the beam is shaded in differing ways and can bring inaccuracies, particularly in laser systems with simple optics systems. When measuring small tools, it is primarily the cutting edge geometry that exerts an influence on the measured result. Different cutting edge geometries protrude to unequal depths into the beam before the corresponding shading percentage is reached. For this reason, a beam with a smaller diameter minimizes the shading error for every blade. Based on this relationship, large beam diameters have a correspondingly high shading error. What this means for the machining process is that when using different tools, dimension deviations occur on the workpiece. Systems with large beam diameters will measure small tools to be longer than they actually are because the tool needed to protrude further through the beam to cause a skip signal.
Focused laser beam
To counteract this, Blum-Novotest uses extremely precise, high quality optics to focus the laser beam. This generates a very thin beam with an extremely homogeneous light intensity, guaranteeing maximum possible precision and absolute accuracy from tool to tool. In addition, these systems feature the proven and patented NT technology that utilizes microprocessors to identify coolant and generate a skip signal only after the longest tool blade has exited the beam.
Reliable production processes
Ultimately, what counts when machining in the micron realm is the precision achieved on the workpiece. This is influenced by a large number of factors, each of which play a role. Fluctuations in the machine and ambient temperature, tool wear and changes in length of the machine spindle at different speeds, all have an impact on the machining results in the hundredth of a millimeter range. With laser measuring systems, such as LaserControl NT from Blum-Novotest, you can accurately account for all these factors. However, if the processing machine does not have the appropriate positional accuracy, even the most precise laser measuring system has its limits. That is why Blum offers specially developed methods and solutions. These allow the actual machine accuracy to be tested on the workpiece and deliver proof of the high absolute accuracy of the laser measuring system.
Testing Machine Positioning Accuracy
To test the positioning accuracy of a machine, a stepped profile, 'micron staircase' is cut into the workpiece along the X-axis, as shown in Figure 1. The height difference from step to step (in the Z-axis) is 1µm. The positioning accuracy is then tested by milling across the µm steps along the Y-axis. This is done multiple times, each time adjusting the depth of the cut by 1µm. A microscope is then used to identify the exact µm step where the qualified cut was made. On an accurate high quality machine, a uniform perpendicular offset cut profile is produced. This gives the user information on the quality of the machine’s positioning accuracy.
Determining absolute accuracy
A modified test can also be used to demonstrate the absolute accuracy of the laser measuring system. The basic requirement for this is a preceding machine accuracy test. In this test, several workpieces with very different characteristics (e.g. tool diameter and shape) are measured without contact using the laser system immediately before the cutting process. When the measurement is complete, a defined Z dimension is cut in the center of the stepped structure (from Y+ to Y-). Finally, the microscope is then used to determine the µm step on which the first qualified cut was produced on each tool. The position of the first cut provides µm accurate reference for answering the question of how precisely a tool has been measured. If there is a positive variation, the tool has been measured as too long and vice versa. Tool SF6 shows the confirmation of the tool zero line that cut the stepped structure.
Absolute accuracy at ± 0.5µm
In the test, four shank end milling cutters (SF) and four ball cutters (KF) with a diameter of 0.1, 0.3, 1.0 and 6mm were measured. When a standard Blum “LaserControl Nano NT” system is used, the spread of the measured values is just ± 1µm. However, if it is already known when selecting the laser system that only tools with similar characteristics (e.g. tool diameter) will be used on the machine, an absolute accuracy in the ± 0.5µm range is achieved.
Tools down to Ø 5µm measurable
The minimum tool diameter that can be measured essentially depends on the conditions in which the equipment is used. Blum systems are designed in such a way to guarantee reliable and precise measurement even in extreme machining conditions. In micro manufacturing, there are different conditions than those seen in typical standard machines. For this reason, specially adapted devices are available for these measuring tasks and environments. If extremely small tools need to be measured for special applications, Blum configures the systems to meet customer requirements prior to delivery. Customer-specific devices enable tools from a diameter of 5µm to be accurately measured.
Ultimately, it always comes down to an interaction between the machining center and the measuring system. If workpieces are to be manufactured with maximum precision, an excellent machine is required on the one hand, but also the ability to measure the tools with the maximum possible accuracy in the actual clamping situation and at actual tool cutting speed. If accuracy in the micrometer range is required, a laser measuring system from Blum is the only solution.