acs Clears the Air For F1 Subcontractor
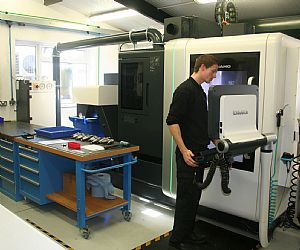
When JK Engineering Ltd was formed in 2001, the focus of the subcontract business was to supply complex components to the F1 industry. Installing the latest 5-axis DMG machining centres and Open Mind CAM software, the Watford company has proven extremely successful since its inception.
Roll forward little over a decade and the company strategy has evolved to target more diverse industry sectors. To accommodate fast turnaround F1 work in small batches as well as large batch production runs, the company has geared its machine shop for automated production as well as complex small batch projects. This has resulted in its DMG DMU machining centres being replaced with five new DMG EVO 5-axis machines with state-of-the-art automation systems. All installed in the last two years, the investment has provided higher spindle speeds with through coolant and inevitably more coolant mist.
Priding itself on the clinical cleanliness that sees so many F1 teams and prestigious OEMs using JK Engineering as a subcontract supplier, the company has always installed OMF1000 coolant mist filtration systems from acs (Air Cleaning Systems) on its CNC machine tools. As an advocate for the acs systems, JK Engineering's Managing Director, Mr John Kenny says: "We have media filtration systems from more than one supplier, so we can testify that the OMF1000 has filter life at least 5 times better than the leading competitor. When we realised the difference between the two systems some years ago, we specified acs units on all our new machine purchases. Now that we have replaced many of our machining centres, the older OMF units have been moved to our turning section and acs has supplied brand new filtration systems for our new DMG machines."
With nine OMF1000 filtration systems on site, JK Engineering insists upon installing the units on all new machine tools. Some machine tool brands, fit filtration units to high specification machines that generate coolant mist, as a standard feature. However, the experience at JK Engineering highlights that the OMF1000 units from acs provide cleaner air, are of superior build quality, are cheaper to install than factory supplied units and also have a more cost effective service life. Furthermore, when DMG rebranded its machine tools with a new colour scheme, acs supplied the new OMF filtration systems to colour match the new acquisitions.
Commenting upon the operating cost of the units, Mr Kenny says: "The OMF units have a media filter that can easily be removed, washed and re-fitted every whilst the HEPA filter lasts for up to two years. This filter life is up to 6 times better than alternate units and therefore more cost effective. As we run 40bar through coolant for 50% of the working day and low pressure coolant the other 50% - and the machines are constantly filled with mist, this demonstrates excellent filter life. Comparing the filter life between the two systems, the OMF1000 units will pay for themselves in a 3 year period. Added to this, the OMF1000 has an efficient 500W fan that saves a considerable amount of power when running nine units."
The ability of acs to meet the bespoke requirements of its customer base has seen the Llantrisant based manufacturer implement a number of measures at JK Engineering. Like many subcontract machine shops, JK Engineering is conscious of operating costs, power consumption, floor space and aesthetics. To satisfy the stringent demands of JK Engineering, acs has not only colour matched the OMF1000 systems to match the machine tools, it has also positioned and ducted the units to best suit the floor space premium of a busy machine shop.
Paying attention to detail, the OMF1000 units have been wired to the low and high pressure coolant pumps on the new DMG acquisitions. By fitting relays to the two coolant pumps on the DMG machines, the OMF systems only run when the coolant is flowing and for one additional minute afterwards to clear any excess mist. By fitting these relays, JK Engineering believes it delivers a 20% power consumption saving on each of its nine OMF1000's per shift. Furthermore, unnecessary operating noise is reduced.
Putting the specification of OMF1000 filtration units into perspective, Mr Kenny concludes: "We've had three factory fitted filtration systems from alternate vendors. They were expensive to buy and to run and they got blocked up frequently. In comparison, the acs units are cost effective to purchase and to run whilst they deliver performance far beyond alternate systems. The acs team pays attention to the finite details to satisfy the customer."
"For us, these details involved colour coding in line with our machines, reducing power consumption by fitting relays to coolant pumps, which subsequently minimises our noise levels and also ducting and positioning the systems to minimise the impact on our limited floor space. Additionally, with filter gauges on the front of the OMF's we know when to clean or change filters. This isn't available on alternate systems and the result was blocked filters, diminishing air quality and unscheduled downtime - something we can ill afford in a production environment."