ACT is Spot on With New I-Center
19 September 2013
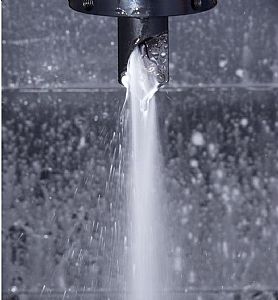
Advanced Carbide Tooling has now launched its new Nine9 Series of I-Center indexable centre drills for improved accuracy, repeatability and tool life whilst also providing reduced tool changeover times. Following its European exhibition debut at the recent EMO event, the new I-Center range of indexable centre drills caused a stir at the show and is already extremely popular with UK customers.
Acknowledged as the world's first indexable insert centre drill, the new I-Center is a highly efficient tooling concept that requires no re-setting or re-sharpening, therefore saving the end user significant time with tool changeovers. By eliminating re-sharpening with a simple insert changeover, the I-Center drastically improves process performance. This is enhanced by an insert clamping system that utilises two locating pins and a clamping screw to give a positioning repeatability of 0.02mm in the radial direction with an axial positional accuracy of 0.05mm.
With impeccable repeatability and accuracy supported by incredibly rigid insert clamping, the new I-Center concept from Nine9 can perform at extremely high feed and speed rates credit to the specially ground insert geometry and robust clamping system. This combination enables the new I-Center to drill alloy steel at 6000rpm with a feed rate of 600mm/min with considerable ease.
The new I-Center delivers remarkable tool life and performance with coolant supplied directly through the tool-holder to the cutting edge. Furthermore, the insert geometries, grades and coatings have all been developed specifically for the preparation of holes.
The Nine9 tool holder for the I-Center range is a robust high alloy steel holder with the shank ground to a H6 tolerance for unparalleled accuracy. With shank diameters that include 10, 16, 20 and 25mm with a length of 30, 48, 50 and 56mm, this optimal length and width ensures the I-Center outperforms all alternate center drilling options. As well as being available in metric dimensions, Nine9 has also developed a series of imperial tool holders and inserts.
As for the I-Center inserts, Nine9 has developed a K20F carbide grade insert that is TiAlN coated for the centre drilling of carbon steel, alloy steel, high alloy steels, cast iron, aluminium and aluminium alloys. With two cutting edges per insert, Nine9 has developed inserts with either a radius or chamfer form. Both designations offer a 120 degree point angle and entry diameters starting at 1, 1.25, 1.6, 2, 2.5, 3.15, 4, 5, 6.3, 8 and 10mm.
When measured against conventional centre drilling methods, the benefits of the I-Center drastically outweigh HSS and solid carbide centre drills. With cutting speeds comparable to solid carbide end mills, the geometries and through coolant facility of the I-Center enable it to increase feed rates and thus productivity by over 20%. Furthermore, under extensive testing the I-Center has proven under testing to process over 7000 holes on steel before an insert change whereas a solid carbide centre drill can only manage 5000 spots. Adding the benefits of improved accuracy, reduced set-ups and changeovers, the I-Center is the centre drilling option for the future.