ACT Launches Flexible MQL Applicator
10 April 2013
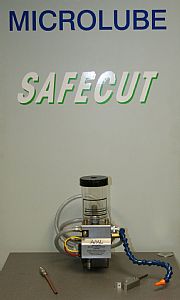
With the benefits of Minimal Quantity Lubrication (MQL) systems increasingly apparent, Advanced Carbide Tooling (ACT) Ltd has now developed its new ECOLube MQL system for reducing machining costs and improving productivity. The cost effective bolt-on solution can be magnetically attached to any machine tool and moved from machine to machine, giving the ultimate in flexibility.
The ECOLube system from Advanced Micro Lubrication, a subsidiary of ACT provides all the advantages of 'near dry' machining with none of the disadvantages of flood coolant. As a replacement for flood coolant systems, the new ECOLube system features an ‘applicator’ unit and pneumatic control to deliver very small amounts of a vegetable-based oil that has no EP additives or chlorine. The lubricant is pumped through a small capillary tube around which an outer tube blows compressed air to effectively spray the oil on to the cutting tool. The innovative new ECOLube device is a small stand-alone unit that can be hidden at the side or behind a machine tool and can be set-up with remarkable ease.
The new application system is ideal for sawing, milling, drilling, tapping and reaming, swaging and pipe manipulation. Discussing the benefits of the system ACT Application Engineer, Karl London comments: "Varying the length of the stroke of the pump will control the volume of the liquid, while a small frequency generator controls the timing of each pulse. A standard consumption for a milling operation is approximately 10ml (or two teaspoons full) per nozzle per hour.”
As a smaller variant of the highly successful MicroLube system, the new ECOLube is a fully portable unit that can be adapted to all types of machine tool. Available as an off-the-shelf product, the ECOLube only requires a compressed air line with 80 to 150psi and a ferrous surface for the magnets to clamp the ECOLube to a machine.
With such low volumes of oil being consumed, the benefits of the new ECOLube system include improved tool life and surface finishes as well as health and safety benefits and the cost reduction associated with oil consumption. For manufacturers that are machining high value materials and generating considerable amounts of swarf, the list of benefits is further extended. For example, swarf remains dry and this improves chip evacuation with compressed air lines. The rapid removal of swarf from the work envelope further enhances tool life and prevents chip re-cutting. Additionally, with swarf waste that is not contaminated by cutting oil, the end user will achieve a better price on their valuable swarf scrap.
As standard, the ECOLube has an oil reservoir with a 1/3 of a litre that is sufficient for 30 hours of production. The oil flow can be controlled by a stroke delivery setting whilst the air line ensures that the heavier than air droplets of oil are continuously delivered to the cutting edge.
To ensure the oil reaches its target, the hoses are provided in 2.5m length as standard with options up to 15m whilst end nozzles offered in lengths from 150 to 750mm in copper or steel or even as a horseshoe type for bandsaw applications.
The operation is controlled by an actuator that opens and switches the applicator on when it receives a signal from the host machine. As a specialist in the provision of lubrication systems, Advanced Carbide Tooling has a number of alternate options available for customers, including its SafeCut metalworking lubricant.