Aerospace Supply Chain Company Selects Tornos Gamma for New Project
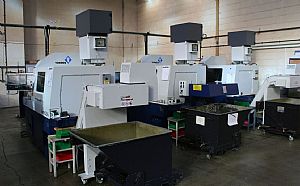
Rugby based Technoset has been actively involved in the aerospace supply chain since the mid 1990s and has seen huge changes in the way the industry has reinvented itself since then to compete in the very demanding, technically and commercially, world of the aerospace industry.
As Technoset Managing Director, Mr Kevan Kane comments: “To be competitive in the industry supply chain today has required sub contractors to commit to serious investment in latest modern technology plant and machinery and also, most importantly, into the training of staff to embrace and commit to lean manufacturing practices and processes”.
Over the past six years Technoset has undertaken a gruelling, root and branch overhaul of its business and working practices, with the cooperation, support and commitment of everyone involved in the business.
This has resulted in Technoset achieving aerospace AS:9100 accreditation four years ago, Mr Kane goes on to say that: “As an early signatory to the aerospace SC21 programme and its associated service commitment levels, the company also received an SC21 Bronze award in 2011 recognising its success in delivering on its Quality and OTIF (On Time In Full) service commitment to its customers”.
As a subcontractor operating all CNC sliding and fixed head machinery with capacity from 0.5 to 120mm diameter Technoset constantly monitors, reviews and accesses its machine capacity, reliability and profitability to ensure the right mix of plant is available to fulfil its commitments to its customers.
Recently, following one such review and compounded by a global aerospace OEM placing a long term order for parts in the 20mm diameter range, the company decided to review the current market place for the best machine tool to most accurately fit the required profile capability and capacity to satisfy its needs. The Tornos Gamma machine fitted that profile most accurately.
A key factor in the decision to purchase the first Tornos Gamma was its ability to work not only as a traditional sliding head machine for long slender parts but also its quick and easy changeover to bush less working for production of short stubby parts. This system significantly cuts material wastage through reduced bar remnant sizes. Mr Kane states: "A lot of our work is with very high value materials such as Inconel, Titanium, Monel and aerospace Stainless steel grades. In some cases very high value materials can cost as much as £50 per meter. The new Gamma can cut remnant lengths from 10-12 inches to 1-2 inches giving us significant material cost savings. In addition, with shorter length parts we can produce significantly more parts per bar”.
From a productivity perspective, the Tornos Gamma has improved cycle times in some cases up to 20% when compared with previous production processes. The improvements result from the Gamma 20 having the cutting tools located close to the workpiece to reduce non-cutting times. Further improvements are derived from the back end tool stations. The Gamma 20 has 8 back end tool stations that offer 4 static and 4 driven tool configuration all having Y axis capability . Previous production only permitted a 2 static and 2 driven configuration. The benefit to Technoset is increased overlapping of the tools stations allowing overlapping to provide simultaneous machining, further reducing cycle times.
As Mr Kane continues: “ The first Gamma 20 arrived at Technoset in July 2011. As part of the Techno Group that also incorporates Technoturn in Hastings we made a group decision to install and trial a Gamma 20 at the Technoturn plant based on the initial success of the first installation. Whilst the workload and machine tool requirements of the Hastings operation are more diverse than at Technoset, the Gamma 20 also fitted seamlessly into the Hastings business."
"At Technoset, our business is 75% aerospace with the remaining work being in the telecommunications and fire detection industries. All three industry sectors are driven by impeccably high quality levels and rapid turnaround times, especially the aerospace work that is predominantly parts for aerospace engines. Our parts can range from simple to complex features that are machined in batches from 500 to 1,000 out of some pretty demanding materials. The Tornos Gamma lends itself to this type of work as it is rigid and robust whilst being easy to set-up and run, thus reducing our changeover times. Lending itself to this type of work, the machine has proven its worth not only at Technoset but also at Technoturn."
With the majority of Technoset's business being in the 20mm diameter range and with business increasing through new orders, the company opted for an additional two Gamma 20 machines that were delivered in December 2011. "We knew that despite our relentless drive for efficiency and improving our capacity that we needed more turning centres to cope with the influx of new work. In the 6 months of having our first Tornos Gamma's at both Technoset and Technoturn we were thoroughly impressed with the level of service and support we have received. With a highly capable cost effective machine tool that improves productivity and reduces waste and the associated costs, we were very comfortable with the prospect of acquiring two additional Tornos Gamma 20 machines. As our business prepares for the challenges of the aerospace market that will continue to grow over the next 3-5 years, we feel that we are now well positioned for the future growth with our new Tornos machines," concludes Mr Kane.