AG/CAD Carves Out a New Market for Flexpress
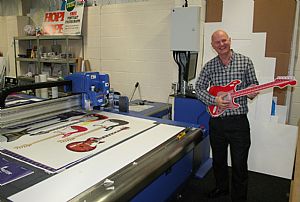
Focusing on the customer and always striving to open up new markets has seen Flexpress Ltd, double its turnover in the last two years. Part of this strategy to enter new markets with an overall vision of being a one-stop print shop, led the Leicester based company to buy an Océ Arizona 360GT flatbed UV printer at the IPEX 2012 exhibition. An investment that was soon followed by a DYSS X7 CNC Die-less Flatbed Cutting/creasing System from AG/CAD Limited.
The Managing Director and the man that started the business with a key cutting shop and a black and white photocopying service in 1989 and grew it to a successful 22 employee business, Mr Steve Wenlock, shares his insight on the situation: "We were already a big Océ customer as well as being an Océ Quality Centre, so we naturally visited their stand at the IPEX show to investigate new innovations. Our business didn't have a large format flat-bed printer but I knew it would open new markets for us, so we made the commitment and the machine was delivered in June 2012."
As an instinctive businessman that has continually pushed the boundaries of his business; when Mr Wenlock was informed by an Océ sales representative that 80% of companies buying large format flatbed printers didn't buy a CNC cutting table, the next step was inevitable. However, the digital cutter offered alongside the Océ printers at the IPEX show proved very expensive, so Mr Wenlock investigated the market further.
With the 8 X 4 foot printer installed and operational, Flexpress was keen to install a digital cutter knowing that it would enable the company to explore new avenues such as production of display units, kiss cut stickers, calendars, show and swatch cards, Foamex boards, life size card and board characters, and much more. The company knew this would take it beyond the capabilities of alternate print suppliers without large format flat-bed printers. So, when Flexpress saw a magazine advert for the DYSS CNC digital cutter, an enquiry was made.
Compared to the machine on the Océ stand at the IPEX show, the DYSS was significantly more cost effective. Investigating the capabilities of the DYSS further, a demonstration thoroughly impressed Mr Wenlock. He continues: "We compared the DYSS to alternate cutting machines on the market and the most staggering factor was cost. We also looked at second hand machines from alternate suppliers and whilst the cost was then comparable, the capabilities of the DYSS were significantly better.” As a result, Flexpress opted for a new DYSS X7 CNC digital cutter and took delivery of the machine in July 2012.
Commenting upon the acquisition, Mr Wenlock continues: "The DYSS build quality is exceptional and it is capable of doing everything we need and more. We now look back and ask why we would be better off with a more expensive alternative. The answer is we wouldn't be better off. The DYSS is extremely flexible and capable of meeting and even exceeding our needs. Furthermore, the dust extraction unit on the DYSS is very neat with the tubing all contained within the machine, whereas expensive competitor machines have bulky overhead units that are ugly as well as noisy."
Flexpress set a modest target of £100,000 of business for the Océ printer and the DYSS cutting table in the first 12 months. Working in complete harmony together, the two new acquisitions have exceeded expectations by delivering the required turnover in the first 6 months. The DYSS CNC cutting table is running for up to 5 hours a day with almost every print job on the Océ Arizona being transferred to the adjacent DYSS machine.
Going with his business instincts, the DYSS acquisition has reaped rewards for Flexpress, as Mr Wenlock states: "The versatility we have been afforded by the DYSS makes us more profitable than the multitude of print manufacturers that can only do vinyl banners with no CNC cutting. The DYSS has put us in a niche market whereby we can be our own cost centre by providing the complete service. Not initially realising the full capability of the DYSS CNC cutting table and the allied KASEMAKE display and boxmaking software, it has already opened doors to new business for us as well as giving us new customers requiring litho print services."
Since acquiring the Océ printer and DYSS cutting table, Mr Wenlock believes that the company has won four 'good' new customers with a minimum annual spend of £50,000 each. These customers work with large high street retailers that are specifically looking for point-of-sale print products that also include card assemblies, signage, panels, window stickers and packages. It is this new customer base and the potential spend that has convinced Flexpress that the DYSS is a winning solution.
"The DYSS has opened a whole new market for us, as customers are coming to us for prototype work and print batches from 1 to 1000. We are winning this work as the DYSS has given us capabilities beyond that of our competitors. This has been proven by a dozen other new customers we have picked up. Many of our new customers include print manufacturers that do not have the capability to conduct accurate CNC cutting work."
The capabilities the company now has with regard to cutting its printed products is a marked improvement. Previously, Flexpress used to Javelin cut its Foamex boards and this would take anything up to 15 minutes per board; with the DYSS cutting table a board can be cut in under a minute - saving considerable time and making each job a cost effective and profitable exercise. With three cutting heads on the DYSS cutting table, the new solution offers the flexibility to cut anything from stickers and cardboard through to Foamex, Di-Bond, MDF and aluminium with extremely fast changeover times between jobs.
Cutting boards on the DYSS has also improved accuracy at Flexpress, as Mr Wenlock continues: "With the DYSS, our accuracy is pin point and every job is 100% correct with impeccable edge finishes. When we previously cut by hand, the shop floor staff would have to gauge accuracy by eye and the 'cutting mark' would often be lost. This would result in the adjacent job and its edge accuracy being compromised. The DYSS has eliminated this issue with its K-CUT Vision System that guarantees precision and speedy processing, regardless of the complexity of the form to be cut."
From a productivity standpoint, Roller Banners would previously take 15minutes to cut by hand and these are now processed in less than a minute. This is a major saving considering the company receives multiple orders each week for batches from two to 20 off banners. With regard to poster production, 100 posters from a roll printed on the Océ would take a full day for an operator to cut by hand. On the DYSS, this is now completed in under two hours with remarkable precision. These examples of savings are on predominantly straight line cutting jobs, for complex curved creasing and cutting, Flexpress would have previously had to turn work away.
Reflecting upon the decision to purchase the DYSS machine, Mr Wenlock concludes: "The DYSS X7 has opened new markets for us whilst improving our productivity, precision and overall quality. I couldn't ask for anything more from a new investment. We are delighted with the acquisition and are already wondering where our business would be without the combination of the Océ printer and DYSS CNC cutting table. As our experience progresses with the KASEMAKE structural design software which includes hundreds of freestanding displays, boxes and furniture, there is no doubt that our capabilities and profit margins will extend even further."