AG/CAD Delivers Blueprint for Diversity
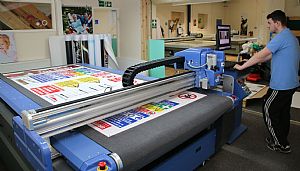
If variety is the spice of life, then valley's based Screentec is the spiciest print company on the Welsh side of the Severn Bridge. Producing everything from ring binders and box files through to clipboards, signs, labels and posters, stickers, wallets and exhibition displays, Screentec prides itself on its ability to turn around virtually any print, PoS or packaging projects from just about any material.
The driving force behind the diversity of Ferndale based Screentec is a management team that employs innovative designers and then supplies its team with the tools to implement its creativity. The latest tools given to its staff was a Trotec laser for rapid prototyping of industrial graphics and membrane switches and a DYSS X7-1325C cutting table from AG/CAD. Commenting upon the DYSS acquisition, Screentec's Managing Director, Mr Darren James says: "We have traditionally used cutting formes produced in-house for cutting our print work, but for small quantity jobs, its been uneconomical. This also applies to prototypes, development work and complex formes that are labour intensive or demand high levels of precision."
"We were conscious that we needed a cutting table and in the 6 months prior to making the decision, we were ruing the missed opportunities and jobs we were turning away. There were 2-3 jobs a week we had to turn away either because it wasn't cost effective or it was beyond our capabilities."
Why Buy The DYSS?
For the Rhondda company the decision was easy. After reviewing the various vendors, Screentec opted for the DYSS for a number of reasons. As Mr James continues: "Firstly, it was the build quality. The DYSS proved more robust and well built than more expensive options. Secondly, the DYSS uses AG/CAD's KASEMAKE CAD software suite that is developed in-house by the Winsford company. Some of the leading cutting table manufacturers have licenses to use KASEMAKE, which means their level of support will never be as good as buying directly from the developer. This was a key factor in our decision."
"Additionally, AG/CAD were attentive to our needs and wanted to satisfy our demands. Many of the larger vendors were far from customer focused - we felt like a number rather than a person/customer. In the 3 months since installing the machine, our initial perception of working with a company that wants to deliver on its service and support commitment, is being fulfilled. Finally, we got all this at a better price than what anyone else could offer. Exceptional build quality, internally developed CAD software and by far the best service available - all at a price almost £25,000 below more expensive machines. It wouldn't have made business sense to select anything else!"
What has the DYSS brought to Screentec?
First and foremost, the DYSS has delivered the tool for 25 employee Screentec to implement its philosophy of diverse print & PoS solutions. Secondly, it has provided the tool for flexible production whilst reducing costs, lead-times and improving productivity. It has also brought more work to the business.
Quantifying the benefits...
The immediate benefit was the ability to reduce the hours its skilled and full time cutting forme employee spent producing formes. Screentec has now relocated his labour to alternate jobs - improving productivity elsewhere in the business. Moreover, the cutting formes were costing Screentec £80 to £150 to produce; a cost that had to be allocated to the respective jobs. By eliminating this cost, Screentec is considerably more competitive on small print and PoS projects.
For example, a recent set of 30 leaflet holders would have required a cutting forme at a cost of £150. This labour and cost input would have instantly reduced the profitability and feasibility of the £250 project. The customer for this very same job, had an eleventh hour design change, which couldn't have been implemented to deadline if cutting formes were made. With the DYSS, a few simple steps on KASEMAKE generated the desired design changes in minutes.
"The DYSS has reduced our cutting forme production by 90% with some formes still being produced for long print runs. It has also enabled us to do tests & trials for customers, improving our flexibility and turnaround times. Before buying the DYSS our average turnaround time was 4-5 days with 2-3 of those days spent creating the cutting forme. Now, in certain cases we can turn jobs around in 24 hours, something that was impossible prior to the arrival of the DYSS."
The jobs on the DYSS..
With its remarkable diversity, Screentec wanted a machine that could be as flexible as its customers' demands. To this end, the DYSS X7-1325C has in its early months been used to cut polypropylene box files, ring binders and retail PoS projects, internal and external signage on Di-Bond; foamex, Corex and display board retail PoS signage and acrylic and Perspex projects for the fruit machine industry. And this doesn't include its printing and cutting of Phototex and vinyl stickers and B Flute board. With its 1.35m by 3.09m bed, the DYSS has the capacity to accept standard 8 by 4 foot boards whilst its roll feeding facility enables the company to print rolls up to 50m long and then transfer straight to the DYSS. A facility that is particularly useful for the printing and cutting of stickers.
Regardless of the material processed, the DYSS is delivering material savings in excess of 20% at Screentec. As Mr James continues: "The precision of the DYSS with its K-Cut vision system gives us the confidence to run jobs to order without running spares for potential errors, which was previously the case. In addition, the nesting facility within the KASEMAKE CAD system ensures we can optimise our material usage to reduce waste and off-cuts. If there is any left-over material or off-cuts, we can easily load it onto the bed for processing smaller jobs at a later date. The combination of these factors is giving us a material saving we couldn't have envisaged before buying the machine."
The Unforeseen Benefits of the DYSS
"In the few short months since installing the DYSS, our business has grown by 10%. However, we receive upward of 20 new customers each month and we couldn't previously retain them all, as we couldn't provide a complete cutting service. Now that we can cut prototypes and small print runs with complex shapes, our customer retention is continually improving in-line with our capabilities. The DYSS is also enabling us to up-sell to existing customers."
An example of this is noted with a company producing health & safety and hospital signage. The company previously used Screentec to print its signage whilst the cutting was processed internally. By acquiring the DYSS, Screentec now prints and cuts the complete H&S projects that are now delivered straight to the end user. This has resulted in a 50% increase in business that equates to £60,000 in the first couple of months of installing the DYSS. The benefit for the customer is reduced component handling and the ability to allocate its member of staff that was cutting the signage to alternate tasks. A Win/Win situation for all sides.
In addition, Screentec has also purchased two seats of KASEMAKE software for its design studio.
As Mr James concludes: "The library within KASEMAKE is extraordinary. It has become a key element of our up-selling strategy. We are using KASEMAKE to design jobs for customers and provide them with CAD generated illustrations, which they are using to sell and present PoS products and services to their customer base. Essentially, it has given our designers a tool to create projects that aren't being cut on the DYSS. The complete package is a revelation to our business."