AG/CAD Delivers Savings to 'Mail' Printer
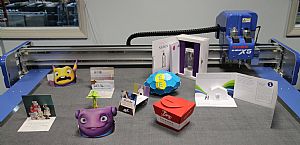
With eight facilities and almost 1400 staff in the UK, DST is one of the most prestigious print and packaging manufacturers in the British Isles. As with any industry leading manufacturer, DST invests in the latest technological advances to maintain its competitive instinct. This recently included the acquisition of a DYSS X5-1310T sample-making / digital cutter from AG/CAD.
Putting DST into perspective, the company produces over 1 billion statement images each year; it is responsible for 836 million posted mail packs that sees every UK household receive a DST printed mail every 13 days. Furthermore, the company picks and packs over 828,000 items each month, and its customer base reads like a 'who's who' of the retail, banking and service sectors. Dealing with such staggering quantities, it’s no surprise the company's busy design department at the 120,000sq/ft Nottingham facility needed to upgrade its ageing sample cutting machine to a state-of-the-art DYSS X5 digital cutter.
The Justification....
Discussing the justification of buying a new cutting machine, Product Development Manager, Mr Steve Hutchinson says: "Like any large company, we needed to investigate and justify our choice of supplier and machine. With a design department that creates over 10,000 design samples every year, reliability was a critical factor. The new cutting table would replace an old Studio Sampler cutting machine that AG/CAD supplied in 1999. As we had been using AG/CAD's KASEMAKE CAD package in conjunction with the machine for over 15 years, we were confident of AG/CAD's outstanding products and technical support. This proven support mechanism and equipment reliability was a key factor in our purchasing decision."
Savings on the Print Shop Floor...
DST Nottingham’s site has a busy shop floor with printing presses generating average print runs from 25,000 to 5 million. It was identified that by producing varnish blankets for its sheet fed presses on a precise cutting machine, set-up time and cost savings could be made further downstream. Since purchasing the DYSS X5-1310T digital cutting table, DST has quantified the savings. As Mr Hutchinson continues: "By producing varnish blankets on the DYSS X5 in just a few minutes, we are saving press time of approx. 30 minutes on simple jobs, more on complex ones. Over the duration of a calendar year, this is saving us £1,000’s in make ready down time. This was a major factor in the investment in the DYSS X5."
The original machine that was replaced by the DYSS was continually cutting from 70 to 350gsm paper as well as folding boxboard (FBB). However, with a diverse product range, DST needed a more precise, flexible and also robust solution for making leaflets, booklets & mailers from 70 to 350gsm, and packaging from folding boxboard up to 750micron range. "The DYSS X5 comfortably processes everything we do. Furthermore, the K-Cut Digital Camera Vision System ensures we have more precise cutting, as it identifies the registration marks on printed jobs to give us impeccable accuracy levels. This allows us to precisely check duplex print back-ups for the production department, saving time & increasing accuracy. We also convert die cut proofs for production jobs, due to the high precision of the machine."
Functionality..
"From a productivity standpoint, the DYSS X5 is considerably faster than its predecessor. This has reduced bottlenecks and improved throughput for our busy design department.
The original cutting machine at DST while very reliable and hard-working was somewhat labour intensive. Mr Hutchinson recalls: "The previous machine used electrostatic hold to secure materials while cutting, a system that struggled on thicker materials, which meant taping sheets down to the plotter bed. With the new DYSS X5 and a vacuum pump sited out of the department, we have a quiet machine that has a powerful vacuum hold eliminating the need to tape sheets down. Our original plotter also applied limited force, equating to multiple passes when converting thicker stocks, something that isn’t an issue on the DYSS X5, due to its impressive force capabilities. Another benefit, having such a broad substrate range to convert, is the sample material profiling feature, which minimises time spent on tool settings during material changes. Plus the digital camera registration system negates the need for creating masks when outputting proofs, a must on our old plotter, adding a further time saving and increase in accuracy. Furthermore, everything we do is within a B1 print size, so we needed a compact machine, capable of the speed, accuracy and flexibility to cover all of our requirements and AG/CAD met this brief to a tee.”