AG/CAD Makes Signs for Success
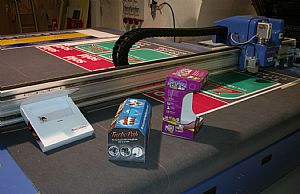
When Mike Hitchman started his company in 1992, the experienced screen printer initially focused upon working with an industry sector that was familiar to him. From its humble beginnings that started with printing estate agents sales boards, SignsDisplay.com has evolved to become the most successful supplier of signs to the estate agent industry in the North East.
The 10 employee company has evolved with technology and this has seen the business move from printing and erecting boards for estate agents in its early days to its existing form that sees the company conducting design, print and the cutting of media for local government agencies, councils, estate agents, hospitals, theme parks and also Point of Sale displays. SignsDisplay.com has reached this point by investing in digital roll-to-roll printers, routing machines and more recently an AGFA 3020 Titan UV flatbed printer and a DYSS X7 2230C CNC digital die cutting table.
Recalling the company's journey, Managing Director Mr Mike Hitchman recalls: "In the early days we were vinyl cutting and producing stencils for screen printing. We are always looking for innovations to improve our business and at Sign & Digital UK 2012, we were looking for a flatbed digital printer and a compatible cutting table with a similar bed size to the printer. The arrival of the AGFA Titan in July 2012 enabled us to process faster and at a higher quality with a 3 X 2m bed capacity, so we could move existing work from screen to digital printing with a capacity of 200sq/m per hour. The market review for a compatible cutting table led us to acquiring the DYSS X7 CNC die-less cutting table that was delivered a month after the AGFA printer. The DYSS complements the printer perfectly with working area of 2.25m X 3m (89 X 120inch) with a maximum sheet size of 2.35m X 3.4m (93 X 134inch)."
Whilst the printer has enabled the Hull based company to increase its capacity and print quality, the DYSS X7 with a maximum cutting depth of 25mm (1inch) has been a revelation for SignsDisplay.com. Prior to the arrival of the DYSS X7, SignsDisplay.com was manually cutting up to 2000 Corex boards each month for estate agents with its Excalibur wall stand and knife. This labour intensive operation was a full time job for one employee. Additionally, with more customers requiring Corex boards with innovative shapes and designs to set themselves apart from their competition, SignsDisplay.com was using a platen cutter with complex board forms to service such demands. With cutting forms externally produced at a cost of £150 per board, this was a cost that SignsDisplay.com had to factor into the pricing for jobs.
As Mr Hitchman continues: "We were in a position whereby more estate agent boards required platen cutting and with typical batch sizes of 50 to 100 and some batches up to 400, the cost of the platen was adding up to £3 to the cost of each board. In a cost competitive market, customers were reluctant to accept this. The arrival of the DYSS allows us to produce these complex Corex boards on the cutting table without the cost of platens. Furthermore, with the KASEMAKE K-Cut workstation and variable look-ahead vector control, we can improve accuracy beyond that of platens whilst optimising our processing speed. This enables us to pass our efficiencies on to the customer and be more price competitive than our rivals whilst providing precision and quality that is far superior."
"In one instance, we were asked to produce a Corex board shaped like a frog. Previously we wouldn't have offered this service due to shape complexity that wouldn't have made the project cost effective. With the DYSS, we accepted the Illustrator file, exported it to the KASEMAKE software and efficiently completed the project. Additionally, we could tweak and alter the forms for this job without the cost of altering platens."
The hand cutting of Corex boards is a slow, laborious task with poor levels of accuracy and consistency. One element of the labour intensive, inaccurate board production is the hand drilling of holes. This is all now a thing of the past as the DYSS X7, notches out holes with unsurpassed accuracy of +/-150 microns (0.0059inch), consistent repeatability of +/-20microns (0.0008inch) and superb edge finishes. This is credit to the rigid machine construction with a heavy duty base and honeycomb vacuum design that gives the boards a rigid base with a high clamping force. Whilst this quality and consistency is a major selling point for SignsDisplay.com, a major benefit of the DYSS is the productivity. As Mr Hitchman continues: "The DYSS has increased our productivity by a massive 20% whilst simultaneously freeing an employee from hand cutting boards to alternate tasks."
DYSS Opens New Markets
The production of frog shaped boards for a letting agent is just one example of how the DYSS has opened new market opportunities for SignsDisplay.com. The DYSS has recently been employed for cutting BeeLite up to 16mm thick for a screen print manufacturer. With three cutting heads on the DYSS, SignsDisplay.com utilises one fixed knife and one reciprocating knife and a routing tool for processing the thick corrugated card that would have been impossible to cut to the required accuracy or quantity by hand. However, the DYSS has comfortably processed the material and the Hull company has also used V-shaped routers to create accurate folding lines.
Highlighting this situation, Mr Hitchman continues: "We now have screen printers and competitors coming to us for our cutting capabilities. The DYSS has developed business from local companies that are aware of our cutting machine. Additionally, it has enabled us to diversify into new market sectors. We are now creating a lot of prototypes and small batch production of cardboard boxes. We are getting more packaging and toy manufacturers becoming aware of our ability to cut, crease and fold boxes and packaging materials. The KASEMAKE software with the DYSS machine also gives us the potential to provide a complete graphic illustration and design service to complement the cutting and creasing. We have only touched on the possibilities of the software at present as we are so busy, but at the first opportunity we'll be spending more time developing our skills with the software as the possibilities are endless."
"We are using the KASEMAKE package in its simplest form at present. Despite our relative inexperience with the package, we have already designed wrap-around covers to protect tree stems for Hull County Council. Using the 3D rendering element of the KASEMAKE package we had the ability to create 3D PDF files and movies to present a professional visual design. This is just one example of the immense possibilities the software provides. We will undergo further training in future as it will undoubtedly create new opportunities for us."
In conclusion, Mr Hitchman says: "We've not had the DYSS machine for long and we're already wondering how we coped without it. It has improved productivity, quality, consistency and efficiency. Furthermore, the machine has improved our competitiveness, reduced our labour demands and with any machine or software queries answered remotely with AG/CAD's remote access to our machine - the service and training has also been outstanding. We've witnessed all these benefits in such a short period of time and we have only scratched the surface with regards to the potential for this machine. The DYSS will be an integral part of our future development and growth."