AG/CAD Packages the Picture Perfect Solution for Venture Photography
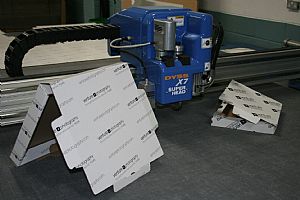
With 35 retail outlets throughout the UK, a thriving worldwide on-line business and outlets throughout Asia and the USA, Venture Photography rightly brands itself as the pioneers of the 'storytelling image'. As the benchmark in family photography, the Venture umbrella also incorporates Venture Productions, a professional digital printing and picture framing service for fine art photographers, digital artists and art professionals.
Dealing with anything from photos of the family pet to working with globally renowned artists, Venture's manufacturing facility and headquarters in Winsford is responsible for the complete production process. To maintain full autonomy over its processes during a period of sustained growth and new product development, the company has now acquired a digital die cutting machine from AG/CAD.
With a facility that encompasses the complete production and assembly of frames, printing and mounting of images, and final packing and shipping of the finished items to customers, Cheshire based Venture is always looking for greater efficiencies, improved quality, and cost reductions. As one of the company's first employees, Production Director Mr Mike Sweetman who joined Venture in 2000, is responsible for the production process from receipt of digital files from outlets or on-line ordering through to printing, framing, packaging and dispatch. It was Mr Sweetman's decision to opt for the DYSS X7 digital cutting table.
Mr Sweetman has been a key architect in building a state-of-the-art manufacturing site that employs the latest technology and also adheres to quality and environmental standards such as ISO: 9001, ISO: 14001 and numerous industry standards such as being a Fine Art Trade Guild member. When Mr Sweetman was tasked with reducing the cost of external suppliers and improving control of the production process, the Production Director scrutinised the 100,000+ externally supplied boxes that package the end product.
After reviewing the options for cutting tables to make its own packaging, Venture opted for the DYSS X7-1630 with a 1650 by 3050mm bed size, which was also recommended by the company's supplier of cardboard boxes. As Mr Sweetman comments: "As our business continually grows, we have an increasing requirement for custom size cardboard boxes for packaging our products. We reviewed the available options and the DYSS digital cutter demonstrated superior build quality, rigidity and innovative design software. What finalised the decision was an AG/CAD recommendation from a trusted supplier. With annual packaging consumption at over 100,000 boxes and climbing, the DYSS has already enabled us to produce over 60% of our boxes internally. In financial terms, the DYSS acquisition has saved us over £37,000 in a matter of months. We would produce more boxes on the DYSS, but we've found another use for the machine – it’s also cutting our new range of high-end aluminium 'Lumino' photographic products. This means the DYSS is working flat out every day, either producing boxes or cutting aluminium sheets."
Installed in February 2014, the DYSS X7-1630 has been supplied with a SuperHead cutting configuration. This incorporates a knife tool and creasing tool suitable for processing corrugated packaging, as well as a high powered routing tool with a dust extraction system and K-Cut Vision unit built into the head.
Commenting upon this, Mr Sweetman says: "Our cardboard packaging is externally printed and supplied in 1.5 by 3m sheets. When we put these sheets on the DYSS, the first task is to precisely align the print with the box design to be cut. We opted for the K-Cut vision system that identifies our pre-determined datum points and automatically compensates for any misalignment when the sheet is laid out on the table. This ensures every box we cut is aligned perfectly with the print design."
"Another key factor in our purchasing decision was the KASEMAKE software supplied with the machine. The software has templates for boxes pre-installed, so we can rapidly change the dimensions of our boxes on screen and immediately cut them on the machine. With a huge diversity in our portrait and frame types and sizes, the KASEMAKE software enables us to produce several different custom size boxes all from the same sheet giving perfect fit and maximum protection for our products. The nesting feature within the software optimises designs to maximise the number of boxes we can achieve from each sheet. The benefit of this is reduced waste and also more boxes per sheet. The result is another reduction in our production costs. With the variety of cost reductions that have resulted from the DYSS and the other uses we put it to, it really has been a fantastic investment." concludes Mr Sweetman.