As clean as they come - Karcher Acquires Tornos Turning Machine
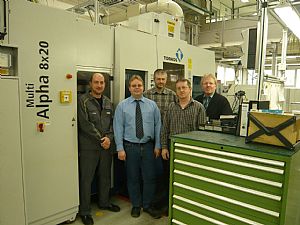
The Kärcher company, based in Winnenden, Germany is the undisputed world leader in the cleaning apparatus sector, with its inventiveness, outstanding performance and innovative solutions ensuring it stands apart. With 8.25 million devices sold every year, the company sets standards in both the professional and private market.
Innovation and quality are the prominent driving forces behind its growth. This is also true of the in-house production which, in terms of precision and productivity, is hard to beat. When producing the triple nozzle for professional high pressure cleaners, Kärcher places its trust in a Tornos MultiAlpha 8x20 CNC multi-spindle automatic turning machine and uses this to achieve impressive results.
Alfred Kärcher was one of the many inventors and entrepreneurs to emerge from Württemberg since the beginning of industrialisation – along with Robert Bosch, Gottlieb Daimler and Graf Zeppelin. He showed great dedication in bringing his ideas to fruition. In 1924, the 23-year old concluded his studies at Stuttgart technical university and started work at his father's marketing company, which he developed into a design office. In 1935, the engineer founded his own company in Stuttgart-Bad Cannstatt in order to manufacture and market for himself his product ideas in the heating technology sector.
Amongst other things, Alfred Kärcher constructed and built the so-called "Kärcher salt-bath furnace", to his own patent, for tempering steel and hardening light alloys for industrial use. 1950 saw the start of the company's unstoppable rise in heating technology, with the development of the first European hot water high pressure cleaner, the DS 350. This design for heating water proved to be so forward-looking that it is still used as the basis for all burners today. However, this just lit the fuse that produced an explosion in innovation.
Every year since, without fail, numerous new products have been launched, and 1270 patents have been registered to date. Furthermore, global cleaning projects gave rise to new processes. For example, the 284 travertine columns in St Peter's Square in Rome were restored using a blasting process specially developed for this task – a total surface area of 25,000m². Since 2009, Kärcher has sold high-pressure cleaners that can not only clean but also renovate facades and strip concrete with pressures of up to 2,500 bar. The name Kärcher has become synonymous with sophisticated cleaning devices across the globe.
A seemingly unsolvable problem…
The professional equipment, amongst other products, is produced at the headquarters in Winnenden. One of the key components, which ensures it stands apart from the competition, is the triple nozzle fitted to unheated professional high-pressure cleaners. By simply turning the nozzle, the user can switch between a high pressure, flat jet or low pressure spray.
Until two years ago, these nozzles were made from brass and procured from one supplier.
Due to the constantly increasing demands, this material was slowly reaching its limits, so process engineer Gunther Laube; Uwe Bareiß the turning shop team leader and shift manager Kurt Schneider started looking for suitable alternatives. All three men are 'Kärcher veterans', shaped by the spirit of the company. This ensured they searched for solutions and worked tirelessly to find the best result in the competent, pragmatic and hard-working way their region is famed for.
The Kärcher manufacturing specialists started with two main aims. The first was for the entire manufacturing process to be brought back in-house. The second was for stainless steel nozzles to be created with a patented inner contour that could produce a more efficient high pressure flat jet. Something that had previously never been managed with a drilling depth of 6xD in stainless steel.
This was a particular challenge for Gunther Laube and his colleagues. To produce the nozzles, sophisticated drilling and milling operations to considerable depths are required and must be carried out with extreme positional accuracy. Each drill hole requires a machining process with at least three to four tools, most of which need internal cooling. For financial reasons and to ensure the positional accuracy, the entire process must be carried out on a single machine.
Brilliantly solved
In this phase, numerous machines were evaluated and numerous trials were conducted. It soon became apparent that the engineers at Tornos were the right partners. Initially, the contours were tested on Almac machines and CNC sliding headstock machines and the process know-how was collated. To achieve the required quantities, a MultiAlpha 8x20 CNC multi-spindle automatic turning machine was finally considered.
This is the only machine that has sufficient tools to finish the part in a single clamping arrangement. On this machine, test machining was carried out using brass and for a long time, Tornos assumed that this material would also be used in the final process. But Gunther Laube had higher goals, and once production had been sufficiently assured with these preliminary tests, the next step was taken using stainless steel. This is where the skills of Uwe Bareiß and Kurt Schneider came fully into play. Together they developed new devices, built a special Y-axis and, in consultation with the product managers at Tornos, undertook some more product modifications.
"It really brought the sweat to our brows" says Gunther Laube, looking back. "We sometimes doubted whether the repeat accuracy of the precisely coordinated machining operations would be sufficient. But we kept on working to optimise the production process. In this phase, we really learnt to appreciate working in partnership with Tornos". This highly complex project was a special challenge for both parties. Finally, the operators also had to adjust to completely new processes. They underwent intensive training for their task in Moutier and got up to speed in record time. When you consider that six tools are constantly in use and the corrections for one tool have an immediate effect on the entire process, you can appreciate what kind of pressure the operators are under. Especially as the load on the tools is substantially higher when using stainless steel.
Meanwhile, the MultiAlpha 8x20 runs like Swiss clockwork with part production times that are actually below the set target. This means Gunther Laube and his team can manufacture additional parts on the machine and relocate yet more products back to the factory.