ATA Group delivers yet another Premier service at MACH
28 February 2012
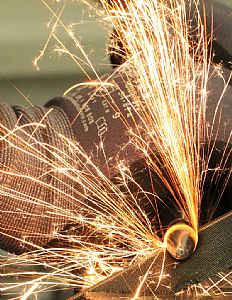
As a market leading manufacturer of abrasive products, hand held power tools and associated services, the ATA Group has now launched a new initiative aimed at improving productivity whilst reducing customers exposure to health and safety risks in the workplace. The new ATA Premier initiative that will be promoted at MACH 2012 on stand 4634J has been developed in conjunction with a globally renowned aerospace manufacturer to assist customers in the provision of a safer work environment in areas where operators are using power tools in combination with abrasive consumable products.
The 6 point process from the ATA Group is an extension of the company's existing programs for reducing the risk of vibration in the workplace. With its new initiative, ATA is assisting its customers with their obligations under The Control of Vibration at Work Regulations 2005.
With over 1400 Hand Arm Vibration Syndrome (HAVS) related claims being reported each year and a number of high profile successful prosecutions being made by the HSE, the ATA Group have developed this program to help create a safer, more productive work environment that reduces the risk of HAVS and the associated cost of litigation.
The first element of the ATA Premier program is to 'Observe Processes'. This involves a site visit whereby an experienced ATA technical engineer will inspect all the customers' processes that may involve exposure to vibration. From this, an overview report is compiled to identify potential risks.
The second step is to 'Propose Improvements'. Areas of concern will be identified in the initial report and improvement proposals will be presented with particular focus on the match between the consumable and the respective air tool. This combination has the largest impact upon the key factors of productivity, safety and reducing operators exposure to vibration. Moving to step 3, 'Measure Vibration'; a trained ATA Engineer will conduct vibration testing to ISO: 5349-2 Standards and submit a report highlighting the free running and in-use vibration results from test runs. This step will focus upon high risk elements identified in Step 1 and compare with levels taken when utilising the changes proposed in step two to give a comparative between the two steps.
The fourth stage is to 'Agree Action' and this will see the results from Stage 3 presented to the customer in a full Test Report, highlighting the key issues and proposing recommendations for improvement. From this, an action plan can be devised to agree improvements with regards to reducing vibration and improving productivity through reduced 'finger on trigger time'. Once action is agreed, ATA implements Step 5, 'Communicate Agreed Improvements'. At this stage, ATA will provide visual aids for the end user to print and use as a reminder for both operators and management. The visual aids will provide guidance on the usage of the correct combination of tool and consumable and any restrictions that may apply. Once agreed upon, the visual aids will be converted to reinforce the benefits of the HSE points system using the key factors from Step 3.
The sixth and final step is to 'Monitor Operator Compliance'. With ATA technical staff regularly visiting customer sites, the ATA Group is able to continually monitor the use of the correct combinations and the overall usage.
Unless vibration is managed in line with current regulations, employers put themselves and their employees at great risk. Can you afford not to implement ATA Premier?