Automotive Subcontractor Burns Rubber With OPEN MIND
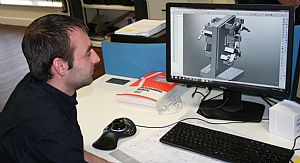
Over a decade ago, Burnley was devastated by the news that French Tyre manufacturer Michelin was closing its truck tyre factory in Lancashire with the loss of over 450 jobs. Since the 2002 closure, the local authority has strived to re-develop the 84 acre (406,270sq/ft) site and its efforts were rewarded in 2013 with Burnley winning the prestigious award of the ‘Most Enterprising Area in the UK’.
Rising from the rubble of the Michelin site with government grant funding is BCW Engineering Ltd. The company that coincidentally started its business in the same year as the Michelin closure, recently moved to a new 30,000sq/ft factory that opened in October 2014 with another factory currently being built and an additional factory planned that will take the total floor space beyond 100,000sq/ft in the next two years. This phenomenal growth has seen the subcontract supplier to the automotive and aerospace industry recently take delivery of its 70th machine tool and its staff numbers swell to its current level of 124.
With the company producing fast turnaround prototypes as well as scheduled batch production for marquee automotive and aerospace brands, BCW relies upon hyperMILL CAM software from OPEN MIND Technologies to program its components. Prior to the arrival of hyperMILL, the highly skilled programmers used a combination of less capable software, manually programming using G-Codes and using external subcontractors. All practices prolonged lead-times and required perseverance to ensure consistently high quality parts.
BCW investigated the packages available from CAM vendors and selected OPEN MIND's hyperMILL based on three factors. As BCW Engineering's Group Engineering Director, Mr Tony Kilfoyle recalls: "We knew that as our business continued to grow and the complexity of our components varied, we needed a reliable, capable and user friendly package that would improve our lead-times, productivity and reduce our subcontract programming dependence. We invited the leading CAM suppliers to conduct an on-site programming trial of a relatively complex part. Only two sales engineers were prepared to blindly program the part on-site whilst the others wanted to send the part back to their office for programming. This instantly raised doubt regarding the technical capabilities and support of the respective vendors and the engineers. The OPEN MIND engineer impressed us by completing the part in 30 minutes, but we were astounded by how easy the programming process appeared. Within 40 minutes the job was on the machine. The knowledge of the engineer, the master class in ease-of-use and the programming speed sealed the deal for us."
"In addition, the fact that OPEN MIND was the only CAM vendor with its own CAD package that is fully integrated into the hyperMILL CAM suite, is something that gave us confidence. We selected OPEN MIND, knowing we were also future proofing our business. The ability of hyperCAD and hyperMILL to work in harmony with CATIA files is a real plus for us as many aerospace files are received in this format. Furthermore, the ability to open and work with CATIA, IGES and Step files simplified the process. In no time at all, parts that took two days to program and then prove on the machine were considerably reduced."
The exponential growth at BCW, now sees the Lancashire company produce over 300 different types of component each week. When considering varying batch sizes, this sees an impressive total of 12,000 parts going out of the door each week. A figure that is projected to grow to 26,000 parts per week in 18 months time. These components vary from gearbox, chassis, bearing housing and turbine parts for the automotive sector to undercarriage, thrust reverser and ejector seat parts for the aerospace industry. To support the diverse range of component and material types, BCW has invested heavily in machine tools from Matsuura, Okuma, Ward Hi-Tech (Dahlih), Mazak, Heller and Mori Seiki with the next planned addition being a Fanuc Robodrill. Open Mind has supplied the post-processor solutions to ensure the delivery from shop floor program to tangible working G-code has been seamless for each machine tool, regardless of machine type and configuration.
Identifying the Benefits..
In its most simplistic terms, hyperMILL has reduced programming times at BCW whilst also reducing its reliance and the cost implications of having some jobs programmed by external subcontractors. Furthermore, the ability to program all its parts in-house has reduced the lead-time for the company's unscheduled production jobs. BCW has two seats of hyperMILL with a programmer dedicated to the aerospace industry and another focusing upon the automotive market.
Shaving time out of the Programming Process..
In both the aerospace and automotive industries, the symmetries of the end product demand a lot of right and left handed parts to be produced. Here, hyperMILL has excelled, as BCW's Chief Programmer, Mr Jim Wharton comments: "We can use the hyperMILL mirror feature for a wide variety of parts. Our parts have an average programming time from 20 minutes to a full day, so the ability to click a button and let hyperMILL reverse the toolpaths and strategy in its entirety is a labour saving for us. We reviewed other packages and their 'mirror' feature will just flip the part and reverse the toolpath; not giving full consideration to special features and strategies on the job."
"We compared our programming time on one component against one of our subcontract suppliers that uses CATIA. Not only did we improve upon their programming time, we also created better toolpaths with smoother and better surface finishes with a shorter cycle time."
"In addition, we have been fully impressed with hyperMILL's ability to change the toolpath and machining strategy from 3-axis to 5-axis (or vice versa) with just the click of a button. This is a huge benefit for our scheduling of work as we produce so many different components that require 3, 4 and 5-axis cutting and we can alternate these jobs around our machine shop depending upon machine capacity and utilisation."
"Furthermore, hyperMILL has also been outstanding on our aluminium extrusion parts. Many CAM packages are no good for extruded parts, but the free-path strategy in hyperMILL allows us to mill through a thin walled surface and then rapid through to the next surface below to continue machining. This eliminates 'fresh-air' cutting. In essence, hyperMILL has reduced my workload and we can now confidently pass programs to the shop floor staff without having to be at the machine to prove-out each job."
As Mr Kilfoyle concludes: "From a CAM point of view, we are confident that there isn't a part that we can program. The only restriction on our capabilities would be the machine tool, but we have multi-axis and multi-pallet machine tools, so our capability level is extremely impressive. hyperMILL ensures that we have the fastest possible route from prototype to finished part."