Automotive Subcontractor Improves Productivity With Tornos Multi-Spindle Lathe
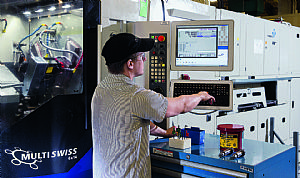
With 15 sophisticated lean manufacturing locations in North and South America, Europe and Asia, employing 2000 people worldwide to make precision-machine components for all major OEMs and Tier 1 automotive suppliers, Autocam is an amazing success story. Operating for over 25 years and boasting sales of US$300M in 2013; Autocam started out with 1 customer like everyone else. The difference behind this manufacturers' success, is that it started out with a handful of Tornos machines.
Today: 200+ Tornos machines globally
Mike Clay, Technical and Quality Director for Autocam, and Frank Zacsek, Manufacturing Quality Engineer, emphasised their experience with Tornos. Mike begins: “We have around 200 Tornos machines today. We use them globally and Tornos is an important partner for us.”
In the Kentwood, Michigan, USA headquarters Autocam manufactures ultra precision stainless, alloy and tool steel components for fuel systems, braking, transmission and other automotive parts on their Tornos machines.
How does Tornos fit into the Autocam equation?
“The market we’re in is ultra-high precision transportation parts,” Mike explains. “We’re turning tolerances of ±10 microns and below. We provide the majority of our products into advanced fuel systems such as GDI and high pressure diesel. Many of these parts have complex geometries and materials that are very challenging to machine. To maintain our leading position in these markets, we need a machine tool supplier who can provide us with a ultra-precise and rigid machine that ensures optimal process reliability. This allows us to provide the highest quality products to our customers at a competitive cost. The relationship that we have with our machine tool suppliers is very critical to us."
Enter the Tornos MultiSwiss Team
When Autocam was looking to add 2 more CNC twin spindle machines to increase production on a direct injection engine pump component at the Kentwood facility, Frank Zacsek, and Matt Tufer, Senior Technician, convinced their Autocam colleagues to consider the new Tornos MultiSwiss machine. Mike tells the story, “The interesting thing on this direct injection program is that the volumes did not require a fully equipped Multispindle CNC. So we wanted a machine that was more suited for this type of program volume that still required high precision. Therefore, it made sense to compare the MultiSwiss to a bank of competitive model CNC twin spindle machines”.
Frank said his thinking was: “if we can do it on one machine for roughly the same manufacturing cost as several single spindle machines, it’s a better process for us and for our customer.”
With high precision direct fuel injection components, surface finish damage to the part must be avoided. The less material handling and moving between machines for these parts, the better. Mike explains, “The more that we have to handle the part and go through subsequent operations, the more opportunities for damage. Our CEO’s philosophy is to stay on top of technology; and if there’s a better technical solution out there that improves the quality or reduces the variation to our customer, we better pursue that even if we’re going to spend more money.”
The purchase price of one MultiSwiss was higher than two additional twin spindle machines; but Autocam thought the ROI on the MultiSwiss looked promising. “So John Kennedy (Autocam CEO) said, ‘Pursue it. Let’s prove it out to see if we can actually manufacture this part on the MultiSwiss. And if we can, we’ll make sure we place an order.”
“With the MultiSwiss, we’re able to develop processes that finish critical dimensions, especially surface finish or flatness,” explains Mike. “And we’re able to do that complete in the machine where a lot of other companies would have to do a face grinding operation.” The fact that the parts don’t have to travel from machine to machine to complete all the necessary operations and instead stay in the MultiSwiss where turning, drilling and milling are done in six sequential spindle stations with up to 3 tools per position means they have a leaner process with reduced chance for part damage.
A key characteristic of a good relationship, according to Mike, is the ability to react quickly. Tom Broe, the direct sales agent for Tornos explains how the MultiSwiss program began. “We were pushing the envelope with this part on the MultiSwiss. It’s not an easy part. There are some tight tolerances and difficult material. I felt confident that the part could be done and so I had to convince Rocco Martoccia, (Tornos Product Manager), and in turn, Rocco had to convince a few people.”
Pushing the limits of the MultiSwiss
The part required turning, drilling and milling operations on 440C material with a 7.3mm diameter and a length of 24mm. Tolerances on the part are ±30 microns on the length and ±20 on ODs. The part was going to push the length-to-diameter limits of machining. Mike adds, “I think if you talk to Rocco, I’m sure he was a little uncomfortable. He knew from the tolerances and cycle time target that we had to hit, and with the material and part geometry, that it was going to be challenging. And he was very up front about that. This is where we work well together. We pushed him a little bit. And we all decided to take the risk.”
Tom continues the story, “One by one people bought into the idea of pursuing the MultiSwiss for this fuel injection production part. Donato Notaro, the Product Engineer for Tornos SA did a lot of work with Autocam to develop the part. He was involved in writing the program and developing the sequencing of the operations, working with feeds and speeds to optimize the cutting operations. On the multi-spindle machines, each position is optimized because each position works independently.”
Frank adds, “We had 2 people in Switzerland for about 3 weeks or more. To develop this particular process, both organizations really worked together to make it a success. When we saw some issues, neither one of us walked away. Together we developed a robust process. We got it over to the US and it’s been a great process for us.”
What Autocam likes best about the MultiSwiss
In addition to the excellent service Tornos has provided to Autocam over the years, and the ability of the MultiSwiss to get the job done and help Autocam make money, the group has other great things to say about the machine. As Frank begins: “One of the nice things about the MultiSwiss, is you can optimize the spindles. This will allow us to hold even closer tolerances on future products. We can bring each spindle into its most capable state.”
Frank also likes the ergonomics of the machine. “Most of the tools are a little bit higher than a standard multi-spindle, so you’re not bending over quite as much. And when you open the door, everything is right in front of you. It’s much better for the machinists.”
With 130 Tornos operators on staff in Kentwood alone, ease of use is also very important to Autocam. As Mike explains: “The the learning curve is generally much steeper for machinists on multi-spindle machines. But I like that when a machinist or engineer looks at the MultiSwiss, it’s not threatening. Because of the way it’s laid out, you can break it down pretty quickly in your mind and get your head around the processing and the management of it. The MultiSwiss is comparatively easier to understand and operate.”
“I really like the integrated coolant lines. With our parts, the material is very difficult to break into small chips. The MultiSwiss design means we don’t have all those oil lines catching chips. When we look at processing a part, chip flow is a very real thing that needs to be considered. A lot of machines will have a significant amount of downtime because we have to open it up and pull chips off the oil lines. With this machine, Tornos eliminated the problem. We have better uptime because of that. Also, since the majority of our equipment is temperature controlled, the ability to integrate the MultiSwiss with our temperature control system is nice too,” concludes Frank.