Award-Winning Customer Parts Showcased at US Manufacturing Exhibition
4 October 2012
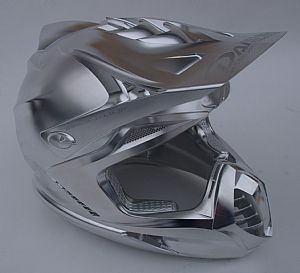
OPEN MIND Technologies debuted its new release of high-performance hyperMILL® CAM package at IMTS 2012. OPEN MIND regularly provides enhancements to all technology segments of hyperMILL® in new product releases. Some of the key functions in hyperMILL® 2012 include innovative 2D pocketing techniques, enhancements to the work-horse profile milling cycle and enhancements to 5-axis shape offset procedures.
IMTS is the largest American trade event for manufacturing technology, held biennially, where customers and prospects meet suppliers and seek new directions and technologies for their investment dollars. OPEN MIND showcased three components, produced by our customers that have won awards for creativity and high quality. Alan Levine, Managing Director of OPEN MIND Technologies USA, Inc said: “the customer components on display gave the visitors to the booth the idea that CAM software should enable and not limit their abilities to meet and surpass their customer’s demands”.
These eye-catching components contributed to a record number of enquiries, many of which are qualified to further explore how hyperMILL® can impact the competitiveness in their shops. hyperMILL® 2012 enhancements focus on streamlined programming techniques and efficient manufacturing processes. These attributes have fundamental impact to prototype and short-run shops as well as production job shops.
The new adaptive pocket technique simplifies programming by reviewing the characteristic geometry of rectangular pockets and automatically assigning best-practice tool path techniques to different categories of pockets (square, long, open, closed). In combination with Feature Recognition utilities, the geometry on simple as well as complex pockets can be organized and then machining techniques can be dynamically assigned to obtain optimal machining. Too often, highly automated techniques rely on sub-optimal machining processes to enable assurance and automation on the programming side.
The hyperMILL® shape-offset technique provides roughing and finishing as offsets from reference surfaces. This provides improvements to machining and leaves consistent rest material for subsequent operations, comparing to “stair-steps” that would remain after using traditional z-level procedures on a curved bottom surface. This procedure is also available in combination with hyperMAXX® high-performance roughing.
The latest enhancement to shape-offset techniques includes axial sorting whose benefits are dramatized in shape-offset “rest machining” in corners. With axial sorting, air transition moves are reduced compared to working level by level.