Beverage Labeling Company Bottles Success With New DYSS Machine
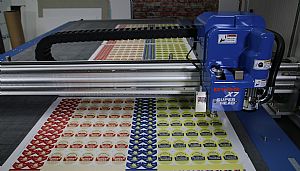
As far as growth and investment go, there are few print businesses currently spending at the level of Print Leeds. The rapidly evolving company has invested over £3.5m in the last four years with a projected spend of an additional £5m in the next 18 months.
In the last four years, the West Yorkshire business has undertaken a factory refurbishment and extension and also acquired a Heidelberg Speedmaster CX102 UV seven colour printer, and just recently a DYSS X7-1630C digital cutter from AG/CAD. In the next 6 months, the company will skyrocket its investment plans with a move from the current 20,000sq/ft factory to a 32,000sq/ft facility and also install another Heidelberg Speedmaster XL106 seven colour printer.
With a factory move planned over the summer and the Heidelberg arriving just before Christmas, the management won’t get time to relax much during the seasonal holidays in 2017. Thankfully, as part of its investment strategy, the 38 employee business purchased the DYSS X7-1630C to help lighten the load.
The company has specialist divisions with core competencies in producing wet-glue labels, UV litho printed plastics, and digital printing that caters for the PoS market and the printing of beverage and food packaging. As one of the most technically advanced printers in the UK, the business always has an eye on the latest technologies and the 3m by 1.6m DYSS-1630C digital cutter was purchased to replace a smaller, slower and ageing cutter. Like the Heidelberg, the DYSS has been acquired to provide capacity, flexibility and added capability at Print Leeds.
Commenting upon the arrival of the DYSS X7-1630C supplied by AG/CAD, Print Leeds Managing Director, Mr Rod Fisher says: “We bought the previous cutter to reduce our reliance on dies and subsequent costs. However, as the PoS and packaging work has grown, we’ve recognised the need for a machine much larger than the previous B2 format. We also needed a router cutting capability for the ever increasing diversity of tough materials we handle, something our previous machine couldn't offer. I reviewed the market and the DYSS immediately stood out above the competition for its build quality, capability and the price point. I asked my technical team to take a more detailed look at the DYSS and they were thoroughly impressed. The DYSS can do exactly what we need and, pound for pound, it's the best machine in the marketplace.”
The DYSS X7-1630C has the ability to cut polypropylene, PVC, foam-board, Perspex, vinyl and much more. With the powerful DYSS X7 Superhead, the new addition can conduct high-speed routing as well as creasing, kiss-cutting and a multitude of extremely precise cutting operations with its oscillating knife tool.
Streamlining Production with DYSS
The £5m+ turnover company already runs a 3.2m wide Truepress W3200UV HS large format flatbed digital printer and when the print specialist moves the factory, the DYSS will be re-located to be positioned alongside the Truepress. “By having the printer and cutter side by side, we’ll streamline our workflow and further reduce lead times. Having the ability to cut 3m printed boards and sheets on the DYSS has already made significant savings over its smaller predecessor. Moreover, we can cut a number of smaller jobs from a single sheet and this has reduced set-up times considerably, improving productivity by over 20%. Furthermore, the DYSS can cut jobs at least 30% faster than the previous machine. The Truepress was recently upgraded to a high-speed model and, without the equally fast DYSS, we would have had a major bottleneck. In fact, we would have been out of the PoS market without the DYSS.”
As well as streamlining production and improving productivity, the DYSS X7-1630C has reduced costs for the rapidly growing company. Cutting a higher volume of small components from large boards is generating a material saving, reducing waste and costs for the environmentally conscious employer.
Referring to this, Print Leeds’ DYSS operator, Mr Mark Craven says: “The material savings on some jobs can be nominal, but on other jobs, it can be as much as a 50%, this will prove significant during the life of the machine. Added to this, we cut a lot of 2.4m high pull-up stands for exhibitions and these were previously cut by hand because they were too large for the old cutting machine. This caused inaccurate cutting and inconsistencies that would sometimes mean scrapping and then re-making jobs. Even when the job was hand cut with precision, each pull-up would take 5 minutes to cut. Now, the DYSS processes these displays in less than a minute with no errors, scrappage or re-working.”
“Additionally, the DYSS has a roll feed facility, so higher quantities of pull-up stands, wallpaper and large posters can be run continuously from full printed rolls that are often up to 60m in length. With the previous machine, we would have to guillotine each poster down from a roll to fit the machine bed. Following this, we would have to hand load, set-up and finally cut each individual job, one by one– a very labour intensive and time-consuming operation.”
Reducing Subcontractor Reliance
Like other companies that aren’t fortunate enough to have a DYSS, Print Leeds were once in a position whereby it subcontracted-out a percentage of its litho work that required cutting. For this litho work, the DYSS has reduced the reliance on subcontractors by at least 20%, saving the manufacturer over £20,000 a year. However, this saving is destined to be just the tip-of-the-iceberg as the business evolves.
As Mr Craven continues: “As well as subbing out cutting of litho work, we used to get Perspex and acrylic jobs cut externally. This is because our previous cutter didn’t have a routing head. Jobs such as shop signage, placards and some PoS work had to be subbed out with a lead-time of around 2-3 days. Now, we can cut these materials in-house to reduce our reliance on external suppliers, eliminate the cost element and shave 2-3 days off the lead-times.”
Taking Diversity Further
The powerful routing head on the DYSS X7-1630C has given Print Leeds the flexibility to cut just about any material it wishes. Whilst this has opened new opportunities for the company, the speed, consistency and precision of the knife tools are equally as important. As Mr Craven says: “We currently produce 2-3 varnish blankets each week for our Heidelberg printer. This is a job we can now process internally with the DYSS. For example, using the kiss-cut tools, we can set a depth of cut at precisely 0.8mm and can maintain this desired depth of cut, even if there are any surface variations or discrepancies in the material. The same tool also handles vinyl kiss-cutting. I’ve worked on all types of leading vinyl plotters and the DYSS is as good as any specialised plotter for doing vinyl work.”
Concluding upon the DYSS X7-1630C acquisition, Mr Fisher says: “The DYSS has been a great buy for our business. It has done everything we expected and so much more. It has given us the potential to open up new markets and take on new work that previously wasn’t possible. We really couldn’t ask for anything more from a new machine purchase. We’re delighted with the performance, the service and the technical support. At the rate our business is growing, there is little doubt we’ll be looking at another DYSS soon.”