Blum Delivers Precision for Turbo Manufacturer
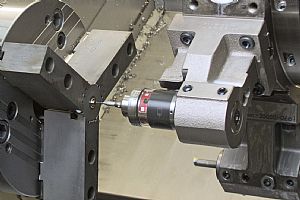
Blum Turbo-Charges Productivity for Automotive Manufacturer
Often faced with the challenge of a complex and almost uncontrollable machining processes, RUMPEL Präzisionstechnik specializes in the machining of high-alloyed materials and investment castings. This is also true for the turning process of turbine wheels for turbochargers of Continental AG. With over 50 years of experience and the use of the measuring system TC54-10 from Blum-Novotest, the company has achieved stabilisation of the complete machining process and time savings of 20%.
Founded by Eugen Rumpel in 1955 as a turning shop, RUMPEL Präzisionstechnik in Upper Swabia region of Germany has a long history of machining high-alloy materials and the machining of investment castings. “The combination of high-alloy materials and investment casting is very common. Therefore it made sense to combine these two areas of expertise in one company”, says Hermann Rumpel, the current managing director. The daily challenge for the 70 employees is to machine materials such as Nimonic, Monel or Inconel to the highest quality standard.
RUMPEL Präzisionstechnik focuses on stainless and heat resistant materials, valve steels, nickel-based and titanium alloys and various special materials. The end customers of the German market leader are primarily automotive manufacturers of turbochargers, such as Continental AG. Flexibility is a priority in the whole company. “Our piece numbers are in the range of one piece in the manufacturing of prototypes up to serial production involving lot sizes of up to 20,000 units. The annual requirement may well be up to 100,000 units," Hermann Rumpel emphasises.
The difficulty in the turning process of turbine wheels for turbochargers is the controllability of the process. The diameter as well as the length of the pin on the rear side of the turbine wheel is machined on a Biglia 565 YS double spindle mill with a Fanuc 18i control system. To be able to meet the small tolerances of 0.012mm in combination with the difficult to machine materials, each workpiece had to be measured manually after manual pre-turning and again after one of the two finishing cuts. Then the correction values had to be entered manually in the machine control. Consequently the production was very low.
Blum Delivers The Solution
A Blum Novotest touch probe was purchased to make the manufacturing process a bit simpler. “The original idea behind it was the determination of the workpiece alignment on the lathe," Gerhard Englisch, the works manager of RUMPEL Präzisionstechnik explains. After further trials to optimise the turning process it became obvious that the measuring task is still more complex than expected. Michael von Rechenberg, the responsible machine operator reports: “I simply tested what the probe is capable of doing. Finally we found out that we are able to monitor the whole process with the aid of the machine control and the probe software."
Consequently it would be possible to implement a closed process chain using the wireless measuring system that uses infrared transmission. The formerly performed manually steps become redundant because the probe automatically detects the current dimension after each machining step and can also correct it immediately by the machine control. The BLUM touch probe also performs the automatic tool breakage detection. This means that the machine control will issue a fault message if the measured dimension is completely out of tolerance because the cutting edge is broken. Compared with the former process it was possible to achieve time savings of 20% through the redundancy of the manual measuring times alone. This is without considering the additional savings from machine downtime and re-working. “The straightforward interplay between the BLUM measuring cycles with the machine control allows us to achieve these enormous savings," Gerhard Englisch sums up.
RUMPEL Präzisionstechnik is dealing with many different tool manufacturers and their products and in this particular turning process tool wear plays a significant role. In the machining process the measuring result cannot always be transferred 1:1 on the in-feed dimension. While for conventional steel the measured 5µm can be set as the in-feed direct, for this special investment casting a certain amount of experience is necessary to achieve the desired result.
This is the starting point for the Blum-Novotest system. Michael von Rechenberg explains: “By measuring both finishing cuts we are able to ensure that for each job the cutting pressure is the same and hence we can meet our tolerances." That ensures highest process reliability. Moreover the tool cost can be brought down by means of the BLUM measuring system. On the one hand the touch probe immediately detects tool breakage and on the other hand, the tools can be used to the actual end of the tool lifetime. While the average tool cost of the industry is about 3% of turnover, RUMPEL Präzisionstechnik utilizes about 10% of the overall turnover for the procurement of machining tools alone.
The advantage of the BLUM touch probe is a higher measuring force, so the cooling lubricant is simply forced through during measurement," Winfried Weiland, Marketing Manager of Blum-Novotest GmbH describes the process. Moreover, a ruby ball of just a millimetre in diameter has to be used for this measuring task. “This is because there is no large measuring surface, a larger sphere would entail the risk of measuring on the radius or the chamfer of the pin which would enormously falsify the measured result," Michael von Rechenberg emphasises. Even this customized design of the stylus is no challenge for Blum-Novotest.
Gerhard Englisch highlights the accuracy of the measurements obtained by the TC54-10: “The measured results are highly precise. The maximum deviation of the probe is 1µm. This is the normal measuring tolerance that even an external measuring machine has." A further probe for a second mill has already been ordered. The new machining centre is also equipped with a BLUM touch probe. RUMPEL also gained positive experience with the service and training services of BLUM during the installation of a TC50 in a further 5-axis machine, and Blum-Novotest are able to offer immediate solutions for any further requirements.
Now, the turning process can be completely monitored by means of the BLUM touch probe. Process reliability was increased to the maximum and the process times reduced by 20%. Rejects could be brought down to a minimum, which is worth hard cash in case of test components that in some cases can cost several hundred Euros. Gerhard Englisch finally says with a view to the future: “Currently different processes in the turning and milling fields are examined for their potential for optimisation with the aid of the BLUM measuring systems. We rely on a partner with whom we can achieve our high quality standards. We have found this partner in Blum-Novotest GmbH."