Blum Ensures NASCAR Team Finishes First For Productivity
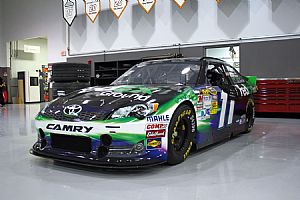
When the owner of your race team is a three-time winner of the American NASCAR championship series, as well as a three-time Super Bowl winning coach, you might expect that no stone would be left unturned in achieving excellence in performance, either on the track or in the machine shop.
For Joe Gibbs Racing (JGR); Huntersville, North Carolina, teamwork is the key to success in the NASCAR Sprint Cup and nationwide racing seasons. Its teams depend on the highest performing chassis and engine parts in their race cars. JGR’s leading drivers include Denny Hamlin in the #11 FedEx Toyota Camry, Kyle Busch in the #18 M&M’s Toyota Camry, and Joey Logano in the #20 Home Depot Toyota Camry.
JGR operates a 929m2 machine shop and quality control department equipped with the latest machine tools that includes 14 Doosan CNC mills and four CNC lathes, a Mitsubishi laser cutting machine, a Mitsubishi water jet, two Mitsubishi wire EDMs, and one Mitsubishi die sinker EDM. There are 21 machine operators, three NC programmers, two manufacturing engineers and a six-person quality control department. Installing advanced probing and non-contact laser systems from Blum-Novotest for tool setting and workpiece measurement has enabled JGR to reduce downtime, increase machine up-time, reduce scrap rates and improve the quality of its high-performance chassis and engine racing parts.
JGR’s operation is setup as a typical job-shop, as Kelly Collins, the Workshop Manager explains: "We set up and run between 60 and 65 jobs a week, some short runs and others longer depending on the volume of parts needed. These parts range from internal and external engine components all the way to driveline and suspension parts.”
One difference, of course, is that the engine and chassis parts and components must meet the stringent requirements of NASCAR before they are even allowed on the track for a race on the next weekend during the season. Maximising the performance of machining operations, Mr Collins goes on to explain: "We are like most manufacturing companies, in that we have a master production schedule and build schedule; there is a need for foresight in the planning and capacity in the shop, especially on the engine side. We know well in advance what we need to make and when we need to make it, how many engines we’ll need, and when we will need them."
When JGR looked to maximise the performance of its machining operations, it asked several suppliers how they managed their tool setting and quality-control issues. Their suppliers recommended the non-contact LaserControl systems and contact touch probes from Blum-Novotest for tool setting, breakage detection, and workpiece measurement.
“At JGR we have a continuous drive to get parts to the race track faster to give us a competitive advantage over other NASCAR teams.” Collins said the company used old methods that involved using 1-2-3 blocks and edge finders to accomplish the tasks. After machining and using hand tools, operators unclamped parts and took them to the quality department to verify features on their Zeiss and Starrett CMMs. Mr Collins explained: “Under the old way of doing things, we experienced a lot of downtime removing parts from fixtures for inspection and re-fixturing, and then manually entering tool and work offsets for re-machining. Also, we were generating an unacceptable amount of scrap resulting from blend-line issues caused by imprecise tool heights. Additionally, we were wasting time on the shop floor by manually entering tool and work offsets into the machine controls.”
Suppliers recommended Blum systems
Searching for hidden machining capacity, JGR began its research into available probing and tool setting sources. Their objective was to get more out of their machines, reduce the scrap rate, increase green light machining time, and improve quality procedures. “Our investigation confirmed the suppliers’ recommendation. Blum’s devices were easy to use, accurate and supported by good service,” says Collins.
JGR then decided they should give the new technology a try and brought in a probe and a tool setter so that the operators could see what the tools could do for them.
There was some initial reluctance on the part of machinists to use the new technology, but after working with the Blum equipment, they began figuring out new and creative ways to use it. Operator Steve Larocque was one of the first operators to use the Blum equipment on a trial basis. “I run a Doosan VMC with a fourth/fifth axis rotary table, a Blum TC50 probe and a Laser Control NT. We load programs that tell what to measure and the Blum software automatically puts in correct offsets, eliminating potential errors while manually inputting data. The TC50 probe has also helped on certain jobs where we had to stop the program to edge-find,” says Larocque.
The Blum system also uses fixed probe programs, which are inserted into their part programs so that they run automatically. The company can run part after part
and the probe will come out on its own and readjust the offsets. Setting tools with either the Z-Nano contact probe or the laser eliminated problems caused by inaccurately produced blend lines in longer runs of parts with multiple tools. Setting tools by hand with the 1-2-3 block depends upon operator experience and there can be differences from operator to operator. “Now that all of the tools are set with a laser or the Z-Nano, everything has the correct height offset,” says Larocque.
95% reduced setup-time
JGR has seen a reduction in setup times in terms of locating stock in the machine by using the probes to more accurately locate the workpieces and set zeros in the control. The company has reduced setup time in most instances by 30% by using Blum technology. Furthermore, it has reduced the level of non-value added quality control tasks by approximately 20%, because the company can now do a portion of its QC effort in the CNC mills.
In one particular case however, they were able to adapt the use of the Blum workpiece probe to reduce setup times of their engine pistons by 95%. In the past, their operators would align and orientate their pistons for final machining using a dowel locating pin inserted through the piston and then orientate the piston with an edge finder. The process took 12 minutes per piston to set up, which with an average of 64 pistons per week, totalled 12 hours 48 minutes for the week. Since the addition of Blum’s workpiece probe the racing team has been able to adjust the piston orientation in seconds, cutting setup time down to 38 seconds per piston. This has resulted in a total time of only 38 minutes per week, a 95% time saving.
“Whenever we needed support, whether over the phone or in person, Blum was quick to respond. The probing accuracy of Blum’s workpiece probe was within 0.0038mm of our Zeiss CMM. This level of accuracy enables us to perform in-the-machine quality control checks,” Collins says.
The Z-Nano, for example, has half-micron repeatability and is used by JGR in both the hard-wired and wireless versions. The laser has a shutter system that protects the optics and creates a higher quality focused beam. The result is better tool-to-tool accuracy, while an integrated tool air blast ensures reliable and repeatable measurements eliminating blend lines. The race team has now eliminated blend issues on the workpiece and without the need for manual entry of offsets, they get more green-light time and have fewer opportunities for typos being entered.
Reliable broken tool detection
JGR is also very content with the ability to check for broken tools with the Z-Nano or laser. In the past, a broken tool caused a lot of scrapped parts, because they would normally not discover the problem until parts were destroyed. Many times, multiple tools would break before the company realized there was a problem. Blum’s tool breakage detection stops the machine automatically when a broken tool is detected.
“We no longer have to rerun multiple tools in order to solve a broken-tool problem, and our scrap rate has decreased by 90% on issues caused by broken tools. Tool breakage detection also gives us the ability to run lights out, which means free capacity. It has snowballed from the first successful installation of the Blum probes and lasers, and nearly all of our machines now have the devices installed," concludes Mr Collins.