Blum Helps Ceratizit To 'Measure at Speed'
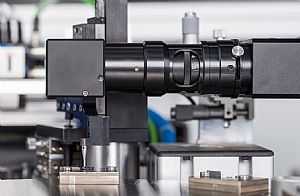
Practically everyone has used a consumer product that has been manufactured with carbide inserts from Ceratizit at least once in their lives, 90% of all the balls in ballpoint pens come from this company. For the measurement of carbide cutting inserts, Ceratizit Austria recently began using an automated measuring cell from Blum-Novotest. This system is special in that the measurements are precise down to the last few microns – and this even though each measurement takes less than four seconds.
The Ceratizit facility in Austria is located in the picturesque mountains of Reutte in Tyrol, near the border to Germany. on this site, the company supplies semi-finished carbide blanks and finished products, with the portfolio being broken down into 'pre-forms', carbide rods and tool inserts. Pre-forms are made-to-order carbide parts that are preformed and partly ground and then processed by the customer. The carbide rods are generally semi-finished products that become drilling or milling tools whilst the tool inserts are finished products used for milling, turning and drilling tools.
The portfolio of tool inserts covers around 2,700 standard inserts with many more special geometric forms made-to-order on the basis of customer specifications. In addition to the inserts, the portfolio includes numerous types of carbide that provide the ideal combination of properties for any purpose.
The MaxiMill 211 is a range of shoulder and slot milling tools that has been well established since 2006 with diameters ranging from 10 to 160mm. The MaxiMill 211 series includes around 100 variations with a large number of materials and coatings to enable the tool to be adapted to the material to be cut.
Ceratizit Presents The Problem - Blum Delivers The Solution..
Until recently, an old automated measurement system was used to measure the many plates, but it was already being put to the limits of its capacity back in 2011. A new measuring cell was sought out to achieve very short throughput times and also be as compact as possible. At Control, the international trade fair for quality assurance, Daniel Scheiber, CERATIZIT's Quality Officer for the Presses Production Line, discovered the flexible Blum-Novotest's BMK measuring and automation concept for the first time. Scheiber had until then never seen such a compact measuring cell that combined automation and measurement from any other manufacturer.
With the BMK 3, Blum-Novotest GmbH has developed a flexible measuring and automation concept in the form of a variable, modular, expandable measuring cell that can also perform additional functions such as sorting, labelling and packaging of parts. The BMK 3 can be deployed in fields ranging from small-series production to fully-integrated process systems for high-capacity serial production. The compact measuring cell can support multiple measuring devices tailored to the purpose at hand.
"While we already had the BMK 3 successfully in use with a number of customers, Ceratizit presented two new challenges. They required a high throughput rate and high measurement precision," said Peter Mösle, Head of Sales of the business division Measuring and Testing Technology at Blum-Novotest.
"There aren't any flat surfaces on the tool inserts, the cutting edges are curved. This makes them very difficult to measure using conventional methods – especially to the precision required in the specifications. We very quickly came to the conclusion that we would have to use a high-resolution optical measuring system," said Mösle.
Ceratizit's Mr Scheiber says: "We had only used camera systems until then to detect positions or geometry, not to measure micron level tolerance values. The required unit throughput time of 3.5 seconds also required us to use a very fast delta robot, which would normally have been used in pick & place machinery in packaging, instead of a conventional robot arm."
The specifications, which laid out the requirements were discussed in a first meeting, and BLUM already presented a concept during the second meeting. "We prepared a very detailed definition of the functions it had to perform. Our experience has shown us that the only way that the best possible machinery can be created is if both sides are perfectly aware of how the final result is supposed to look. When we say micrometres, we do mean micrometres. BLUM was aware of this from the beginning, so we felt at ease with them right away," said Lothar Schmid, the Head of Presses Production Line at CERATIZIT.
A concept using two robots was first pursued – a delta robot for handling the inserts and another portal conveyor system for handling the boxes, in which the tool inserts were to be placed. The robot would remove the plates from a transport pallet and place them in the machine on a high-speed rotary bench. This rotary bench would turn the insert under the camera where it would be measured. Finally, the robot would place the insert into a 10-insert box. To ensure a stable process, Blum-Novotest developed a monitoring system that ensured that the boxes would lock into place correctly during stacking.
"It became apparent as early as the design stage that robots would be too expensive and that getting two systems to work together would be too complicated. A changing gripper system was the breakthrough. We now use two different rapid prototyping vacuum grippers to transport the tool inserts and the boxes using the delta robot," said Mösle.
"The BLUM developers did a great job. The plant is now running absolutely reliably. "We didn't ship the machine until optimisation was complete and it was running reliably without any problems. That can take a little longer with such a machine, where we're working at the limits of the laws of physics, and with prototypes," remembers Schmid.
"The inserts were really heavy considering their small size, and it wasn't easy to ensure that they didn't fall off with the fast movements of the robot. The precision of the measurement process is also on the limit of what is technically possible," said Schmid, explaining the challenges.
"BLUM has provided a compact, space-saving machine. We're very low on space, so every square metre counts. The BMK 3 is nice and compact, and can be installed anywhere. We also have the option of actually integrating the machine later in the production process, just as I had envisioned."
The Blum-Novotest measuring cell offers quantifiable advantages – the BMK measures 40% more tool inserts per hour on half the space compared to the old system, and all this at a speed that could not be achieved before.
"We were fast before, but now we're measuring what we want – all of the insert's features," explained Daniel Scheiber.
"And we can operate the system practically without personnel – the operator just looks in from time to time to fill up empty packaging boxes. Our operators have taken quite a liking to the BLUM system. We have a very open and honest relationship with Blum-Novotest, that was clear in the development and optimisation phase. Our needs were understood right away and met superbly. We've achieved the necessary throughput rate, whilst still achieving maximum measurement precision and a very reliable process. This has provided us with large capacity reserves – and shown us that the vision of integrating measurement into the production process is certainly realistic," concluded Lothar Schmid.