Blum Makes Measurement Childs Play for Playmobil
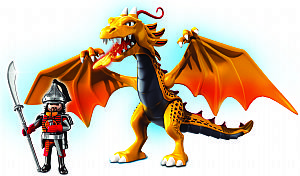
Few toys have brought a smile to a child's face more often than the friendly Playmobil figures. Lots of new figures are released every year, placing high demands on the in-house mould-making shop. To achieve maximum efficiency in its automated operation, Playmobil's numerous machining centres use LaserControl measuring systems from Blum-Novotest.
Playmobil figures are more likely to invoke images of playful creativity and imagination than of high-tech engineering. In fact, the figures are miniature miracles of technology, whose components are all precisely designed and matched to each other. When a hand is rotated in an arm, for example, a specific torque has to be produced to ensure that it does not rotate back of its own accord – and the two individual parts of the arm have to be manufactured with the corresponding degree of precision. The mouth and eyes are not printed on, the head is injection-moulded from two different-coloured plastics in a complex process, whereby the brown plastic eyes are injected into precision-fit recesses in the head blank. So, the demands placed on the mould-making process are very high.
A total of 77 designers and technicians are working continuously to produce new figures and sets, for which new injection moulds then have to be made. "We output as many as 1,200 new moulds a year, around 45% of them internally and the rest from external contractors. To increase our in-house capacities, in 2015 the mould-making shop is going to be relocated to a new building, which will quadruple its size. That will also entail an expansion of our machinery portfolio, and mean more of the injection-moulding will be done in-house," reports Attila Britting, head of the in-house mould-making shop.
For Playmobil figures, hundredths of a millimetre count. The aim in making the injection moulds is to output a finished plastic item with practically no reworking – vital in view of the approximately 10 million single parts a day, and over 100 million figures a year.. Consequently, the mould separation must also be a high-precision operation, so that no burrs occur on the single parts or the finished figure. For two-colour items such as the legs onto which different-coloured shoes are injection-moulded – it must be ensured that the shoe mould precisely fits the pre-moulded legs, so that no gaps occur after the plastic cools. Additionally, he moulds are specified for extremely high volumes of 200,000 to 300,000 pieces from one mould.
To execute the jobs, several of the machining centres are fitted out with pallet changers and tool magazines with the capacity to hold as many as 120 tools. "The machines even keep running unmanned over the weekend, that degree of automation would not be possible without the Blum laser systems. The Blum-Novotest systems are installed in the workshop on our nine automated DMG five-axis machining centres," stresses Marco Mendl, team leader CAD/CAM/NC.
After every tool change, the laser automatically measures the length and radius of the tool prior to machining and after machining checks for breakage and wear. This saves the experts having to pre-set the tool in the presetting device. A new tool is simply shrink-fitted into the holder and measured at machining speed after fitting. This ensures that the tool data in the machine is correct, numerical errors or mistakes reading off data can no longer occur. Further features include high-speed automatic compensation for the thermal expansion of the complete machine and for spindle displacement. "Five years ago I would have still been saying that it is impossible to incorporate the complete tool measurement process into the machine, but now it works like a dream," comments Marco Mendl. "We have had only good experiences with Blum lasers – and we save on working time because there is no need for pre-setting. The accuracy of the LaserControl system is astounding too. Based on our experience, its repeatability is within less than two thousandths of a millimetre."
Incorrect tool data can have costly consequences. A spindle damaged by a crash will cost at least 18,000 Euros to replace. Without a monitoring system to detect worn or broken tools, automated production cannot be implemented. The LaserControl system's breakage monitor ensures that a broken tool is detected immediately after every machining step. Depending on the programming, the machining centre can then swap the tool or notify staff, who can log in to the machine over the Internet and monitor the workshop through a webcam.
At Playmobil, as many as four of the key tools are held in the tool changer, meaning the automated overnight jobs run highly reliably. If the laser detects that the tool is worn after machining, a twin replacement tool is automatically loaded. High chromium content steel is mostly used because it wears less when injection-moulding large quantities. "It does cause considerable tool wear during cutting. That is why it is very important to keep an eye on the running times of the individual tools. The Blum laser measuring systems enable us to do that very well," Attila Britting adds.
High-precision measurement in a dirty environment poses a major challenge, and coolant is essential to the production process. To protect the optic from being soiled, the measuring system is mechanically sealed off from the coolant by a pneumatically operated shutter piston during machining. The rotating tool is also cleaned with compressed air prior to measuring, to ensure that the measurement is not influenced by swarf, dirt or cooling lubricant. During measurement, a stream of barrier air provides protection against soiling.
On the five-axis machines, the moulds are wherever possible cut in a work-holder fixture, in order to achieve maximum possible accuracy. Often very small tools are used, capable of reaching into the most difficult corners of the mould. On the nine automated DMG machining centres, tools from the 0.5mm ball cutter up to the 50mm milling head are deployed. On the two Röders machining centres used to produce the graphite electrodes, the range extends down to the 0.25mm ball cutter. Only PCD tools are used on these machining centres, the diversity of tool variants poses no problem for Blum LaserControl systems.
The LaserControl systems have truly proved their worth at Playmobil. They allow the toy manufacturer to make optimum use of night-time and weekend working to attain the required output without any detriment to quality. The more precise the machining, the less reworking is required. Previously it took as long as two weeks to spot a split mould. Today the job is done in two days, because the moulds emerge already virtually perfect from the machining centre.