Bosch Brings Home the Bacon with HAM tools
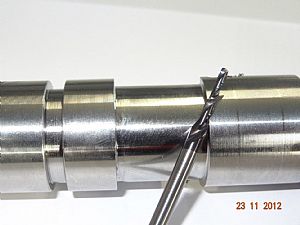
The agreement Rainford Precision has struck with HAM Tools (www.ham-tools.com) to distribute its cutting tools in the UK will now enable British manufacturers to witness the productivity benefits that are being made on the continent. The new range of cutting tools has reaped significant rewards among various industry sectors throughout Europe. With regard to the automotive sector, one such company that has benefited is household name Robert Bosch GmbH.
With a turnover of €52 billion and over 300,000 staff worldwide, Bosch regards itself as the world’s largest supplier of automotive components and assemblies. The company's manufacturing plant in Homburg, Germany, is widely acknowledged as the world leading producer of diesel fuel injection systems, common rail injector systems, high pressure accumulators and pumps for domestic and commercial vehicles. When an injector body manufactured in regular batches of 1 million parts was creating production issues, HAM Tools supplied the solution.
The production of cross holes on common rail injectors from 37HRc Alloy Steel (50CrM04) has posed a multitude of questions for Bosch Engineers. The cross holes for internal return flow of diesel was previously machined in a number of steps that have now been reduced, by using special HAM step drills. The issue for Bosch was the burrs left inside the rails when the drills break through the material into the inner bore. The burrs had a detrimental effect upon the flow of diesel through the rail injectors and would create issues in a completed engine assembly, therefore producing burrs is unacceptable.
Initially, Bosch used a 2mm drill without spot facing in an inclined position on a transfer line station to drill to an 8mm depth via the riser bore. Then a second station would precision ream the tight tolerance holes to the required 2.25mm diameter.
Unfortunately the internal burrs created by conventional tools machining at high cutting pressures could only be fully removed by Electro Chemical Machining (ECM). This not only added another time consuming process, it also changed the physical properties of the material, which resulted in reduced product quality and stability.
To eliminate this material change, Mr Rainer Lauffer, the tool scheduling and technology manager at Bosch Homburg and his colleague Mr Michael Walter, the applications engineer responsible for the production line wanted to develop new cutting tool solutions with the remit of creating a drilling and reaming tool for production of virtually burr free holes. The Bosch Homburg plant with over 6,000 employees has enjoyed a longstanding relationship with HAM Tools, so the engineers called the prestigious German cutting tool manufacturer to develop a solution.
The engineers at HAM Tools created a solid carbide step bore-milling tool that was engineered to the exact specifications of Bosch. The first trial runs with the new bore-mill-reaming tool instantly delivered promising results, so the development engineers at HAM, working closely with the Bosch team evolved the tool to its final design. Commenting upon the project, HAM Tools technical engineer recalls: "Firstly we had to check the technical feasibility on the basis of the required profile. The final design of the solid carbide bore-mill reaming tool and its associated geometries for piloting, the pre-cutting step and the drilling cutting edges were all incorporated into the design process. We chose a tough and wear resistant ultra fine carbide composition for the drill. The sample tools underwent severe field testing and had to prove themselves with centre drilling and straight positional entry without spot facing."
The solid carbide step bore-milling tool has a 1.87mm diameter at the pre-cutting step and a stepped diameter of 2.25mm to complete the process. The 4mm diameter shank step tools conduct the drilling and secondary reaming process in one-hit to deliver the virtually burr free holes to tight tolerances and with improved productivity levels - just as Bosch required.
The overall benefit to Bosch is the elimination of tool changes, the separate process of reaming, the time consuming part handling and de-burring process. These successes are achieved whilst also improving the hole consistency and quality, but above all delivering the removal of burrs. Despite cross drilling and reaming without spot facing to an 8mm depth, the HAM solution drills 550 holes prior to precautionary tool changeovers. This is supported by 50Bar coolant pressure being delivered to the cutting edge to flush swarf from the impact zone to contribute to the hole quality and extended tool life. For further information on how HAM Tools can deliver solutions for your production requirements, please contact your local Rainford Precision representative.