CAD/CAM Suite and High-Performance Package Expanded
9 March 2019
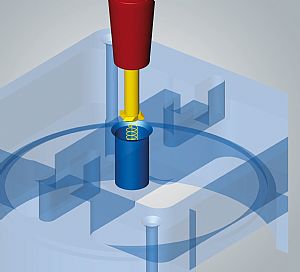
Wessling (Germany), 14 January 2019 – The latest version of the hyperMILL® CAD/CAM suite, 2019.1, is now available. OPEN MIND, one of the leading manufacturers of CAD/CAM solutions, has expanded the finishing module in the hyperMILL® MAXX Machining performance package. Further highlights include process optimisations as well as new functions for reducing calculation times.
‘5-axis Prismatic Fillet Finishing’ is a new function in the finishing module of hyperMILL® MAXX Machining: Thanks to the geometry and automatic setting of the barrel cutter, this feature can be used in accordance with the principle of a high-feed milling cutter.
The processing takes place in a plunging and pulling movement with an extremely high feed and this allows the highest machining performance possible with high-performance conical barrel cutters, also called circle segment or parabolic cutters. Ball and radius cutters can also be used efficiently with this strategy.
hyperMILL® 2019.1 – process optimisation at a glance
Thread milling options have been completely redesigned for hyperMILL® 2019.1 to improve convenience and user friendliness for the programmer. The module supports a variety of different thread milling cutter types and allows extremely easy selection of right-hand and left-hand threads or the definition of the milling direction from bottom to top or vice versa. The thread milling feature also offers automatic approach and retract macros, a selection of roughing options and simplified programming.
Changes without recalculation
hyperMILL® manages the order of the processing steps with job IDs. Changes to these job numbers have so far resulted in recalculations - these are now avoided to save time. The improvement in job management now means that a job ID can be changed without having to subsequently recalculate the machining job in question. The consecutive numbering of the compound and machining job is controlled via a start value and an increment value. The benefit of this new feature is transparent structuring and reduced calculation times. The clamping position can now also be changed later without the machining jobs having to be recalculated.
Improved management of standard and special tools
The tool database in hyperMILL® has received a small but fine improvement. Until now, there was only one comment field. In Version 2019.1, users have the option of individually expanding the tool database. As a result, information such as order numbers, prices or service life can now be clearly stored and the CAM programmer is able to manage tools even better than ever before.