Celebrities Endorse Signs Developed Specifically for Dementia Sufferers
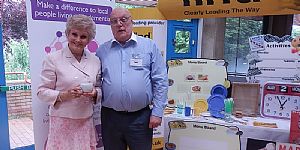
When Find Signage was acquired by Anthony Cockcroft in 2011, the new owner quickly recognised there was an urgency in evolving the company's established reputation as market leader in the mental health sector by creating new product innovations. In the last three years the company, which is the world’s first developer of dementia-specific signs, having previously worked closely with numerous mental health experts at Sterling University and Bupa to create a range of signage, has diversified its offerings which now include revolutionary dining products, clocks, visual communication boards and memory boxes for those affected by dementia and cognitive disabilities.
Establishing these products overseas, Find Signage has witnessed exponential growth for its innovative product lines and particularly the visual communication boards that include menu boards, pain assessment charts, personal orientation boards and activity cards. With many of the Forex®/Foamex, acrylic, aluminium and DIBOND® boards requiring the insertion of a variety of different visual aid cards, Find Signage was witnessing a bottleneck between its wide format printing and the hand cutting of small quantity cards. This is why AG/CAD's DYSS X7 cutting table was acquired to deliver savings.
As Find Signage Managing Director, Mr Anthony Cockcroft comments: "We realised that while our large quantity print runs could be cut with industrial routers, smaller quantities and prototype work was labour intensive. It was clear that we needed a flexible and accurate cutting solution and we opted for the DYSS X7-2230C Superhead cutting table. We fully reviewed the various vendors and found the DYSS solution with its innovative KASEMAKE software to be exactly what we needed."
With regard to its food menu boards for dementia patients, the Foamex and DIBOND® wall mounted boards have pockets for patients to select their next meal from a selection of card images and position on the boards. Printing post-card images of meals from 3 by 2m large format printed sheets, the card quantities of up to 200 per sheet were previously cut manually with a knife and ruler. This labour intensive task would take upward of four hours. By installing the DYSS, this task now takes 5 minutes with precision, consistency and cut quality also improved. Furthermore, capacity has been increased and staff can be allocated to alternative tasks.
Boarding Brilliance
The design variation and quantity levels of visual boards and signs produced by Find Signage has also caused capacity and lead time issues for the Leeds based company. As Mr Cockcroft continues: "Our visual boards are available in a wide variety of dimensions, designs and colours, so production of each type rarely stretches into double figures. In addition, a lot of the visual boards and signs are prototypes and development projects where we are creating samples for customers. This caused extended lead times and quality deviations prior to the installation of the DYSS X7."
With varied schedules, the DIBOND®, Acrylic, Aluminium and Foamex boards that can be up to 20mm thick, were either externally produced by the company's die manufacturer or they were machined on the two heavy duty routing machines at Find Signage. By using the external supplier, lead times for prototypes were extended and response time was outside the control of Find Signage. For the production of heavy duty signage boards that were machined in-house on the routing machines, the issue was edge finish and precision. This led to extensive secondary hand finishing.
With the arrival of the 3.2m by 2m bed DYSS X7, Find Signage has cut the cost of external suppliers by over 20% by reducing the work passed to subcontractors. It has also reduced the reliance on platens/dies for small quantity production. A benefit of this is the drastic improvement to the lead times on prototypes and development work. Find Signage can now produce samples internally by printing its signs and then cutting on the AG/CAD machine. In addition, the removal of work from the heavy duty routing machines has improved capacity on the machines whilst the quality of finished product straight off the DYSS has eliminated the secondary hand finishing operations.
As Mr Cockcroft continues: "The benefits of the DYSS cutting table are evident throughout the company. It has improved productivity and capacity, reduced lead times and labour requirements and streamlined our operation. Furthermore, the KASEMAKE software enables us to conduct 3D rendering samples for customers. It gives the customers a better visual perspective of the project at hand and helps to prepare estimates for end users. The software also enables our shop floor to generate better layouts of our work, so we can make material savings by producing more parts from each sheet. We are delighted with the DYSS machine and software."