CNC International Provides the Spark for Oil & Gas Subcontractor
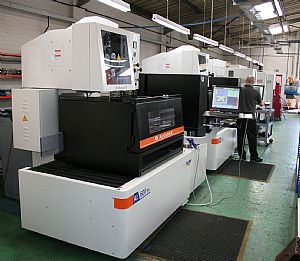
Carving your own niche in the subcontract manufacturing sector is something that many will boast, but in reality, there is always a company snapping at the heels offering the same service. This isn't the case for Poole based Multispark, a subcontract manufacturer to the oil & gas, satellite and F1 sectors.
The second generation family owned business has been working in the wire EDM and spark erosion sector since its inception in 1969. As Multispark Director, Mr Dave Sheldon confirms: "We have decades of expertise. We don't offer subcontract turning or milling, everything is EDM and this alone puts us in a niche market position. Our expertise and the capabilities of our plant list of 19 machines that includes 8 wire EDM, 9 spark eroders and two hole burning machines enables us to cut anything from steel, copper and brass through to graphite, aerospace grade alloys such as titanium and also PCD. Our ability to machine PCD through our innovative techniques and in-house machine tool retrofits and methods, is something that takes our niche capabilities to a whole new level."
As a continually growing business that is investing in cutting edge technology whilst replacing ageing machines, Multispark has just acquired two new Accutex AL600 wire erosion machines from CNC International to replace two old Agie machines. Like any astute subcontractor, 8 employee Multispark reviewed the EDM market but it was the capability, build quality, performance and above all the service from CNC International that sealed the deal. As Mr Sheldon continues: "Down the years we've had machines from most EDM suppliers, but its the service from CNC International that clinched the deal. CNC has been servicing our machines since the late 1990's and this longstanding relationship has always been based on their exceptional service levels."
Sparking Up the Savings...
The driving factor behind the Accutex purchases is the relentless company growth that will soon see the Dorset company open a second factory unit on the other side of the coastal town. Whilst a new facility is part of the growth strategy, investment to improve productivity is also a must. Since the December 2014 installation of the two new machines, Multispark has witnessed productivity improvements of 40% with each of the new Accutex machines. Commenting upon this, Multispark's Works Manager and Accutex operator, Mr Chris Bailey says: "With the increased productivity of the new Accutex wire EDM's, the output of the two new machines is equal to four of our older machines. So, we have drastically improved capacity without requiring additional floor-space. Furthermore, the ageing Agie machines constantly required operator intervention because the rollers and belts that feed the wire constantly needed changing. By eliminating this maintenance factor, the Accutex AL600's are saving us another 10 hours a week in lost production."
"Furthermore, we run our machines lights-out and we have CCTV on the shop floor to alert us when machines are on-stop. Our team is alerted to any machine stoppages via mobile phone texts, so we can come back to work to correct faults and commence production. With our older machines, we would either avoid lights-out running or risk being recalled for machine stoppages. The reliability of the AL600's allows us to comfortably set large jobs for lights-out production, confident that there will be no call-outs. The combination of 40% improved productivity, saving 10 hours a week in downtime and the ability to confidently run unmanned makes the machine utilisation of the Accutex machines closer to 75% more productive than our older machines."
An additional benefit for the South Coast company is the more powerful generator and flushing pump on the AL600. The pump fills the tank 50% faster than the old machines, reducing non-cutting times even further. Not only does this feature reduce non-cutting times, it also clears waste from the work area faster, which enables the AL600's to use less power and generate a slower more efficient pulse. The result is a reduced wire feed rate, which is allowing Multispark to slash its wire costs by over 60% on the new machines.
Improved Flexibility With Accutex..
The distinct advantage of the Accutex AL600 Series is its spacious work area of 600 by 400 by 300mm; something that allows Multispark to process significantly larger jobs. The work area of the AL600 is 50% larger than the previous machines whilst only occupying a similar floor-space to the machines they replaced. As Mr Bailey continues: "The large work envelope allows us to machine larger jobs, which is suited for lights-out and the space inside the tank makes it easy to maintain the machine and load the jobs. As a business, we have gained a multitude of productivity, machine uptime and cost reduction benefits. On top of this, the Accutex has improved surface finishes and precision by delivering a tolerance capability of +/-3microns."
"On a personal note, the Accutex machines are intuitive and easy to use with their 19 inch touch screen monitor that is graphically driven to make operation almost self explanatory. The powerful control is linked to the OptiCAM system we purchased from CNC International with the Accutex machines and this streamlines our operation with regards to improving machine programming, set-up and work through-flow. From an operator perspective, I'm delighted we have the machines as they are very user friendly. From a management perspective, we couldn't ask for more in terms of productivity benefits, quality and precision improvements, machine utilisation and capacity increase and of course the cost reductions through less consumable usage. All this will undoubtedly deliver a fast return on investment for Multispark," concludes Mr Bailey.