CNF Precision Optimises Productivity from ITC Tools
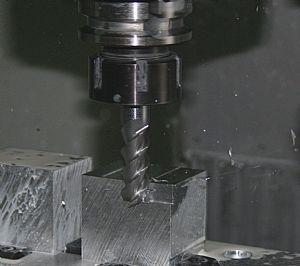
When Clive Fearnley borrowed £200 in 1967 from a family member to buy his first lathe, he couldn't have envisaged that his start-up company would be spending over £1.5m in equipment, some 45 years later. The impressive growth at CNF Precision is credit to investment in the latest technology - something a million miles from a small room above a dairy occupied by one man, a small lathe, a drill and a bench grinder.
Wind forward a few decades and the Aylesbury based subcontractor has invested heavily in recent years with high-end machine tools that include a 15 pallet Matsuura Hplus300 HMC, a two pallet Doosan HP5100 and a Nakamura Super NTJ twin spindle turning centre with B-axis. Commenting upon the company's progression, Managing Director and son of founder Clive, Mr Neil Fearnley says: "When I started here 25 years ago, we made our first foray into CNC's with simple Bridgeport retrofit CNC machines. Now, we have some of the most productive and efficient machine tools available. These are machining extremely complex parts for the aerospace, medical, scientific and motorsport sectors in anything from aluminium, steel and brass through to more exotic materials like inconel and tungsten."
Producing a vast array of parts that include cabin interiors and tooling fixtures for aerospace OEM's and anaesthetic & life support systems to the medical industry, the subcontractor machines everything from prototypes through to production runs of 100k+. With such high production runs, pride of the shop floor is the Matsuura Hplus-300 that is running unmanned for 16 hours a day on aluminium parts only. However, to maintain this remarkable uptime, the 120 tool pots have to be stocked with similarly productive and reliable tooling solutions - and this is where ITC comes to the fore.
As Mr Fearnley continues: "ITC were recommended to us back in 1997 and we've been using their tools ever since. We will always use the best tools for our applications, so we were open to visits from numerous reps from an assortment of tooling OEMs to do trials down the years. However, they have all failed to improve upon the productivity, tool life and consistency of the ITC product line. Now, the 120 tool Matsuura is predominantly tooled with solid carbide drills and end mills from ITC. The Matsuura will run over 120 hours a week, machining up to 6 different jobs at any one time and the same ITC finishing tool has been running on all these jobs for almost 12 months without a tool change."
CNF Precision now uses a complete range of ITC products. In fact, CNF Production Manager Mr Mark Baron flicks through the latest ITC product catalogue and recalls: "I would say in the front half of the latest ITC Catalogue, we have used 80% of the tooling and our ITC consumption is continually increasing. We have tried tools of all types from a range of suppliers, but nothing matches the quality and tool life we get from the ITC range. We have compared like for like tools from competitors and the quality of their carbide and coating doesn't come close to ITC."
ITC Proves its Point
Highlighting the benefits of the ITC product line, CNF confirms that a 10mm diameter ITC 4081 Series four flute solid carbide roughing tool was introduced to an MoD aluminium panel case and it reduced cycle times by 50% whilst more than trebling tool life. This was achieved whilst running on the company's Doosan HP5100 HMC at speeds of 14,000rpm and feeds of 6m/min with a 5mm depth of cut. The tool life has improved so drastically that the same cutter is still running 5 months later. A staggering achievement when the Doosan runs for 20 hours a day.
Even with ITC's unparalleled reputation for aluminium tools, the benefits of Tamworth cutting tool specialists' range is noticed throughout the machine shop on a variety of material types. As Mr Baron says: "We were using two coated solid carbide harmonic flute end mills from a well known supplier. Used for roughing and finishing on 17/4PH stainless steel, they would only last for 1.5 days. This aerospace wing fixture bracket was to be machined in a batch of 320 parts that would take us 6 weeks. The poor tool life and surface finishes were disrupting production, so we turned to ITC. Gary Bambrick from ITC suggested ITC's 4081 Series of 4-flute harmonic end mills for roughing and the 6051 Series for finishing. Running at the same speeds and feeds, we instantly increased tool life from 1.5 to 5 days with a better surface finish for prolonged periods."
The ITC tool life and productivity benefits don't end there for CNF. More recently, the company has introduced ITC's line of Widia VDS drills to a pneumatic valve component that was being produced on the company's Nakamura Super NTJ turning centre. As Mr Baron recalls: "The existing drills were returning poor tool life on the free machining steel parts that had to be produced in two batches of 2000. After struggling to drill 400 holes, we tried the Widia VDS drills on the 5.8mm diameter, 22mm deep holes. We instantly trebled our tool life. Using the VDS drill to process the parts, we found the VDS drill was still usable after drilling 2500 holes. This gain is because the VDS drills have no land, which makes them stronger and they retain their sharp cutting edge. Furthermore, there is no edge chipping."
In conclusion, Mr Baron believes: "ITC is our first port of call for virtually all our tooling solutions. The extensive line of off-the-shelf products is enhanced by an ability to manufacture specials. All this, is supported by an excellent engineer that calls upon us frequently to service all our tooling needs. However, we wouldn't be using ITC if it wasn't for the quality of their products that proves itself time and again on our shop floor."