Cumberland Boxes its Way to Success With AG/CAD in its Corner
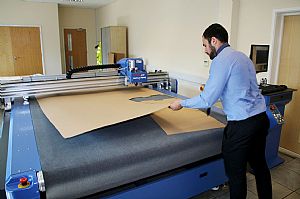
As one of the UK’s top five independent sheet plants, Cumberland Packaging has now invested in a superfast DYSS X7 Sample Cutting Machine from AG/CAD to reduce its lead times and increase its design capabilities.
The Essex manufacturer of corrugated cartons and boxes has used KASEMAKE CAD software and equipment from AG/CAD for more than 20 years, so when it came to updating its plant list the company opted for another machine from AG/CAD. Explaining why, Cumberland Packaging’s Managing Director, Mr John Watson says: “Over 20 years ago we had a plotting machine, then 12 years ago we stepped up to our first sample table, which enabled us to produce quality samples when used with AG/CAD’s KASEMAKE design software. The sample table has served us well, so when it came to modernising our equipment, we opted for the latest DYSS X7 machine from AG/CAD.”
The Shoeburyness manufacturer looked at machines from other vendors, but the existing business relationship and the reliability and service support previously provided, along with the functionality and speed of the DYSS X7 machine were key factors that sealed the deal. Within 24 hours of visiting the AG/CAD showroom in Cheshire, Cumberland placed its order.
“The market has evolved considerably since we bought our last machine. Customers now demand samples of 25-50 boxes often in 2-3 different designs and the turnaround time is a critical factor. Customers in the packaging industry want a number of different designs and package sizes to transit test. The transit test is all about fitting a set number of boxes on a pallet to minimise transportation costs for the end product. We are often supplied with specific racking and pallet dimensions to ensure our designs pass the transport test. With the KASEMAKE software from AG/CAD, our design team can meet the design and dimensional constraints with speed and precision.”
Once the Cumberland design department has its design signed-off, the CAD files are passed to the die-makers to prepare for production runs generally in the region of 10,000 to 50,000 boxes. Even here, the seamless transition of the CAD files via KASEMAKE guarantees that no anomalies in the design occur when transferring data.
Improved Capabilities With DYSS X7…
For Cumberland Packaging, the X7 has delivered more than just reduced lead-times for its samples. As Mr Watson continues: “With our older machine we were restricted to only cutting cardboard up to a particular thickness. This meant that we were either overlooked for many projects or we had to subcontract our sample cutting out to a third party vendor. The issue here was losing control of the complete process or just simply losing business. With the new X7 we can cut Stratocell®, Correx®, foam shapes and many other substrates that were previously beyond our capability.
Furthermore, 10% of our packaging requires foam inserts that we couldn’t previously cut. The DYSS enables us to design and cut our own foam inserts, further reducing our reliance on alternate vendors and re-gaining control of the ‘entire process’. We can now provide a ‘total solution’ as opposed to just a ‘sample’.”
At Cumberland Packaging 90% of its output is corrugated card whilst the remaining 10% consists of foam and Correx®. It is this final 10% that is now also fully under the control of the Essex company, credit to the new DYSS X7 machine.
Cutting Lead Times…
Protective foams such as Stratocell® are cut on the DYSS X7 way faster than previous cutting methods, while consistency, precision and cut quality have all been significantly improved.
The 75 employee business produces flexo printed packaging solutions for a large number of its customers who typically want to see a printed sample prior to production. The KASEMAKE CAD suite allows the Cumberland design team to place artwork onto their structural designs and then fold them into 3D with the artwork rendered onto the packaging to make a virtual 3D model. Cumberland’s sales reps can then take images and live 3D PDF files created by the software to show their customers without having to wait for a physical printed sample. These files can also be emailed directly to the customer for visualisation and approval purposes.
As Mr Watson continues: “The KASEMAKE 3D rendering feature enables our sales reps to provide proposals faster with a more professional and visual display for the end user. KASEMAKE even enables us to show customers what their final design will look like in a particular environment. The software is continually being updated, so we’ll always be at the forefront with the latest design innovations and interactive 3D solutions.”
“We are already reaping the benefits of buying the DYSS X7 and as we take the business forward, we aim to be more efficient and competitive. We have ambitions of taking our turnover from £10 to £15m in the next three years and the arrival of technology like the X7 cutting table and KASEMAKE software will be instrumental in driving our growth ambitions,” concludes Mr Watson.