Cut Coolant Costs With Nederman 'Plug and Play' Swarf System
2 July 2016
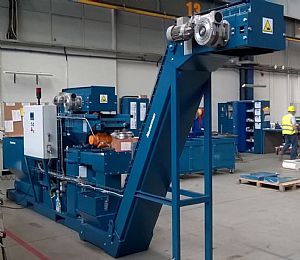
For manufacturers conducting heavy material removal machining, Nederman has now introduced its impressive new SS40 ECON swarf and coolant management system. Capable of processing up to 200kg of steel swarf an hour, the SS40 ECON system removes the coolant from the swarf and recycles it back to the machine tool, storage tank or filtration plant. The SS40 ECON is suitable for most Ferrous and Non Ferrous materials.
The benefit for the customer is two-fold. Firstly, by removing excess coolant from swarf and collecting it, operators can re-cycle the coolant back to the machine tool or tank, reducing coolant waste and the associated cost of continual topping-up. Secondly, by removing excess coolant from the swarf chips the customer generates clean dry swarf that yields a higher re-cycle value. Most impressively, this cost-effective system rapidly re-coups cash for the customers. Furthermore, it is completely flexible with its small footprint and plug-and-play design that makes it easy to install inside the factory.
Capable of processing a diverse selection of material types, the SS40 ECON consists of a 300L receiving hopper and a hinged belt conveyor that is driven at 2.4m/min by a 0.37kW motor to rapidly transfer chips through the process.
Rising to an outlet height of 1.5m, the conveyor passes the swarf to a bar-end separator. This separator rejects bar-ends and larger parts from the centrifuge inlet to avoid damage to the centrifuge drum. This separator also doses the chips to the centrifuge drum to prevent any unbalancing of the centrifuge.
Installed on vibration dampers, the VD40 centrifuge incorporates stainless steel wear plates on all wear surfaces to prolong machine life. With its 4kW motor, the centrifuge can process up to 200kg/hour of short steel swarf. The compact centrifuge separates the coolant from the swarf and the dry swarf is evacuated via air-flow at the top of the centrifuge to a swarf bin.
The system utilises a Siemens S7 PLC for its main control output, which is encased in a CE marked E-cabinet. The cabinet is pre-assembled and delivered to the customer ready for connection to a 400V 3 phase 50Hz power source. All elements of the SS40 ECON are installed on a robust steel skid plate, so the complete system can be delivered 'ready-to-run'. As can be expected with any high quality Nederman product, the exterior elements of the SS40 ECON are black steel that is primed and painted according to RAL 5009 in Nederman's Azure Blue whilst galvanised and coated features do not require painting. This meticulous attention to detail ensures the SS40 ECON is prepared to deliver a lifetime of production with minimum maintenance requirement whilst retaining its aesthetically pleasing appearance.
Furthermore, the SS40 ECON has a small footprint and is ‘plug and play’. This ensures quick and easy installation, although it can also be tailored to the specific demands of the customer and application with optional extras such as level sensors for the swarf container and hopper conveyor and also skip hoists.