Dairi-Pak Reap Benefits From DYSS Digital Cutting Table
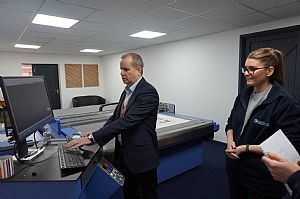
The fundamental cornerstone of Shrewsbury based Dairi-Pak is exceptional customer service. The very founding ethos of the packaging specialist, based in rural Shropshire, stems from company founder, the late Brian Gray. One weekend, Brian was approached by a local farmer and friend in desperate need to package dairy products that required immediate delivery, Brian rushed out and bought a roller press and a gluing machine to help. The rest is history...
This responsive, friendly and innovative ideology is what started the business in 1987; and it is this customer orientated service that has since seen Tim Gray, son of the late Brian and also the Chairman of the UK Sheet Plant Association, drive the company to its modern-day industry-leading position. Of course, investment in both staff and technology has been instrumental to the on-going success of Dairi-Pak, a success that will certainly be taken to the next level with the arrival of a DYSS X5-1625T digital cutting table from AG/CAD Limited.
Moving into its 30th year of business, the 48 employee corrugated sheet company has diversified down the decades from its roots in the dairy industry into the design, print and production of boxes, cases, fitments and pads, PoS and much more for all sectors. With a client list that includes some of the world’s most famous brands, Dairi-Pak has invested heavily in machinery and factory expansions throughout its history. The investment strategy in the early years majored on good second-hand machinery, but more recently investment has been in new high volume machines. These in-line case makers and automatic die cutting machines are now well utilised, helping to make a return on Dairi-Pak’s investment in CorrBoard and at Platt Mill (the home of Dairi-Pak).
Dairi-Pak has always been strong in design and has had great success using KASEMAKE and an AG/CAD KM sample cutting table for the last decade. The company has built a reputation for bringing new projects to fruition to very tight timescales enhancing Dairi-Pak’s reputation as a leading bespoke packaging supplier.
However, in 2017, the investment program accelerated further with the arrival of a new ink kitchen, spectrophotometer, a new 4-colour Martin case-maker and a DYSS X5-1625T digital cutter from AG/CAD to replace the previous KM sample table.
Diversifying With DYSS
As the company has grown, more and more demands were being placed on the original KM cutter and the company found a bottleneck with the production of prototypes, samples and short run work. The simple route to resolving the issue was to invest in a new, ultrafast digital cutter and once again, AG/CAD had the solution.
Alluding to the selection of a new cutting table, Dairi-Pak’s Operations Director, Mr Ian Ford recalls: “We recognised the KM machine was relatively slow, the bed size was restrictive to our ambitions and the material it could handle was mainly limited to single wall corrugated sheets. As a business, we have evolved to processing more twin-wall corrugated materials.
Dairi-Pak specified the DYSS X5-1625T with a large work area of 1.6m by 2.5m, ideal for typical sheet plant board sizes. Also contributing to the decision was the clever K-CUT camera system that enables accurate cutting of printed samples when required. Dairi-Pak opted for the print register camera as an additional feature to assist the production of full colour mock up’s and small runs or even individually personalised, digitally printed boxes and PoS units.
Commenting upon this ability to rapidly turn out samples, Sales & Marketing Director at Dairi-Pak, Sarah Glover says: “We have immediately rolled out a ‘sample while you wait’ service for our customers. It allows customers to visit our site, work with the designers and leave with their product packaged to their requirements. It is the high speed of the new table that enables us to do this. Customers with new product launches or unexpected repacking jobs have found this particularly beneficial.”
“A new sample room has been custom built to accommodate the new DYSS X5 cutter. This will further streamline the process of producing small volume production runs. The space this has freed up is becoming a brand hub; a relaxed space full of inspiration and examples of packaging where customers will meet with our designers and sales team to develop ideas before they are produced on the DYSS”.
Mr Ford continues: "The X5 is a massive leap forward from our old machine, cutting all our substrates up to BC at high speed and with excellent quality. The creasing in particular was a revelation, with none of the typical liner cracking along flute direction and yet with vastly better defined creases, both with and cross flute."
Benefitting From the DYSS
The arrival of the DYSS X5-1625T has eliminated bottlenecks and significantly improved the through-put of the design department. Discussing the impact of the DYSS, Dairi-Pak’s Design Technical Chloe Evans says: “The sectors we serve and the sample and materials types are evolving at a rapid rate. In-line with this, our sample design and production has diversified and increased drastically. Our sample and prototype lead-time was being determined by the speed of the old KM machine. The arrival of the DYSS was like a breath of fresh air.”
“The K-CUT Vision registration camera system and incredibly fast cutting tools allows us to process short-run batches in the region of 20 to 200+ extremely quickly. This eliminates platen costs or subcontract cutting costs and we can offer in-house short-run work as well as fast turnaround samples. As an example, we can now produce 100+ samples to test how parts will fit with pallets for downstream transportation.”
“In a typical week, we could be producing hundreds of samples, so having a cutting machine that is several times faster than its predecessor, certainly alleviates pressure and quality is massively improved too."
DYSS Delivers Quality
The technology imbued throughout the new DYSS machine has reduced board waste by over 10% in the design department at Dairi-Pak. Chloe Evans continues: “The X5 is very solid which has improved precision whilst the built-in automatic tool calibration eliminates potential for error when changing blades. For example, the old KM machine required manual tool setting and adjustment. When creasing, it could be difficult to ensure the exact pressure level on fluted board whereas now speed, pressure and depth profiles for all tools are fully automated with the DYSS. This eliminates human error, eradicates the potential for scrapped board and reduces the set-up and processing times considerably.”
Commenting upon the K-CUT Vision system, Chloe says: “Cutting printed sheets wasn’t previously feasible with the old KM table so this has been a big benefit with the new machine. The DYSS has made life so much easier for everyone involved in the design and sales team at Dairi-Pak.”
Managing Director of Dairi-Pak and Chairman of the UK Sheet Plant Association, Tim Gray, has always been forward thinking and recognised early on the industry trend for short run production of plain and printed packs to complement the traditional higher volume die-cut runs. Mentioning the DYSS machine from AG/CAD, Mr Gray says: "With the high speed of the X5 we can see that it has the capability to be used as more than just a sample cutter and is allowing us to explore the possibilities of short run, die-less production as we go forward".