Diba Industries Eliminates Bottleneck with Tornos
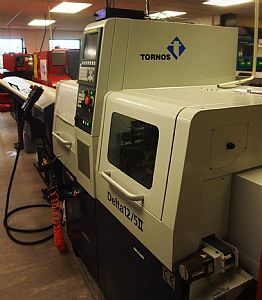
When Diba Industries identified a bottleneck in its machine shop that produces connectors, fittings and adaptors for the fluid handling industry, it found the solution with a Tornos Delta 12/5 turning centre.
As a market leading provider of innovative solutions to the most demanding fluid path applications for the clinical and scientific sectors, Cambridge based Diba has a turning section that was witnessing bottlenecks created by a relatively unproductive single spindle turning centre that required a full time operator for programming, loading and un-loading the machine.
Already a user of other sliding head turning centres with 16 and 32mm diameter capacity machines, the first point of contact for Diba was its existing supplier. However, the only machines available proved over specified and too expensive, so Diba reviewed the Tornos range. Commenting upon the reasoning behind buying the Tornos Delta 12/5 that was installed in September 2013, Engineering Project Manager at Diba Industries, Mr Paul Wright comments: "We wanted to replace the single spindle machine with a more productive twin spindle to eliminate the bottleneck where we produce parts under 16mm diameter. New machines from our existing supplier had too many axes and features and were therefore overpriced for what we required. Whilst Tornos equally have high end turning centres, the Delta proved a perfect fit for our parts as it had the right specification at the right price. What sealed the deal for us was the guide-bushless running on the Tornos that reduces the bar remnants and the associated waste at the end of each bar."
Turning expensive materials such as PEEK and PCTFE, Diba was previously left with 250mm remnants from each bar - a waste rate of almost 10% per bar. The guide-bushless system on the Delta has cut this waste rate by upto 60%, which equates to a 4% overall saving on material costs.
From a productivity perspective, the Delta 12/5 has reduced some cycle times from four minutes down to 1 minute per part. This cycle time saving of 3 hours a day or 60 hours a month is partially down to the twin-spindle set-up that completes each part in one-hit as opposed to additional set-ups on the previous single spindle machine. The benefit of completing parts in one operation on the Delta 12/5 has improved component quality, consistency and overall accuracy. Furthermore, with a typical batch size of anything up to 500 parts, the barfed Tornos removes the need for an operator to constantly load the machine. As Mr Wright continues: "Our previous turning centre had to be manned almost permanently, whereas our other machinists set-up and run a number of machines simultaneously. The arrival of the Tornos has freed up our operator to also simultaneously run other machines."
Whilst the ability of the Tornos to deliver upto a 75% productivity improvement over a single spindle machine is impressive, the Delta 12/5 has also absorbed some of the workload from the sliding head machines at Diba. Here too, Diba has witnessed cycle time improvements. The kinematics of the Tornos with tooling positions close to the workpiece has improved productivity and cycle times by an average of 10% over the existing and more expensive sliding head machines.
Highlighting other benefits of the Tornos installation, Mr Wright says: "As a first time Tornos customer, we are delighted with how easy the machine is to program and set-up. The barfeed integrates with the machine perfectly and it is easier to conduct bar diameter changeovers than our other machines. The set-up times are drastically reduced, which is ideal as we may run two to three different jobs each day on the Tornos. Running upwards of 500 parts and then re-setting the machine for the next job; the Tornos is extremely well developed for flexible production schedules like ours. Additionally, the Delta 12/5 has high pressure coolant and this has been a revelation in managing the long string like swarf that is commonplace with the materials we machine. On the whole, we are delighted with the Tornos machine."