Diesel Generator OEM Wins Global Success With Ellesco Surface Finishing
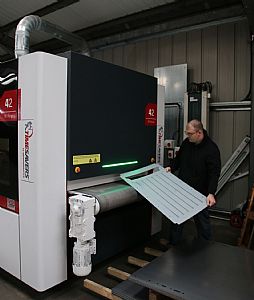
Manufacturing and assembling diesel generator systems for the global audience, Welland Power is truly a UK manufacturing success story with its products 100% exported. Often exposed to the elements, the power units are powder paint coated to ensure they remain in working order throughout their extensive warranty period. But when a redesign of its generator casings compromised the quality of its paint finish, the Spalding company turned to surface finishing specialist Ellesco for a solution.
Producing over 3,000 generators each year that are all exported to Asia, Africa, Europe and the Middle East, Welland generators are exposed to challenging environments on all continents. These environments include extreme heat, cold and also coastal areas with a high potential for corrosion. With a standard product range of over 30 generators that are supplied to schools, hospitals, mining, manufacturing and construction sectors to name a few, the Lincolnshire company re-designed its casings to improve efficiency. As well as enhancing efficiency, the redesign aimed to improve air-flow to dissipate heat in warm climates whilst improving the protection of the generator sets against external factors such as weather and contamination.
Producing all its sheet-metal components in house on its Amada Alpha 4kW laser machine, the redesign created more features and protrusions on the Zintec components that left sharp edges. The result was paint peeling from the sharp edges further downstream. Discussing the issue, Welland Power Managing Director, Mr Charlie Farrow says: "We already had staff conducting upwards of 3 hours hand finishing each day and the redesign was certainly extending this. However, we had to be mindful of manual finishing as we didn't want to remove the fine coating from the Zintec sheets. Additionally, the redesign created features that were difficult to hand finish because of their intricacy. We seen Ellesco at MACH 2014 and we re-visited the company for a potential solution. We gave Ellesco a few samples, they exceeded our expectations and highlighted the benefits of the Timesavers machine. We instantly made the choice to invest."
With the exterior paint coating being such a critical feature in the aesthetics and longevity of the power generators, 19 employee Welland Power invested in an Ellesco Timesavers 42 Series Rb radiusing and surface finishing machine in September 2015. As Mr Farrow continues: "Apart from the engine and alternator that we purchase from Perkins, we manufacture and assemble the complete generator set. With over 30 standard models and hundreds of parts in each generator, quality and consistency are key for us. As a result of installing the Timesavers 42 Series Rb, we have immediately eliminated the 3+ hours of hand finishing. With more holes and detailed slots being cut into our casings, this hand finishing time would have extended without the Ellesco machine."
"However, the bigger picture shows that we have eliminated potential returns or rejects and extended the quality and service life of our products. All this is credit to the Timesavers 42 Series Rb machine that consistently rounds corners to eliminate burrs and sharp edges on 90 degree features. The Amada laser is cutting casings, bases, control panels and boxes and we can now put more of these parts through the Ellesco machine to improve quality and aesthetics throughout our product."
In the 40,000sq/ft facility that manufactures generator sets from 9KVa to 2200KV that can be anything from the size of a dishwasher to a small lorry, the Ellesco Timesavers 42Rb Series sits alongside the Amada laser machine to generate an efficient through-flow of components.
As third generation company owner Mr Farrow continues: "As a company that has evolved over its 100 year history, we are proud of our British manufacturing heritage. This is why we buy from Perkins, because they are British, and as a UK manufacturer, we are proud to deliver our product quality, innovation and longevity to customers around the world. As part of our strategy to continually improve, we are currently 'salt spray testing' our products to check the adhesion of our coatings. We will also be testing a series of different base materials, coating types and also the surface finish of the material, as this is instrumental in paint adhesion. The Ellesco machine also has a full range of settings that will be tested in conjunction with the paint and material technology to deliver the best product to our customers."