Dream Performance from KDM Vertical Turning Lathe
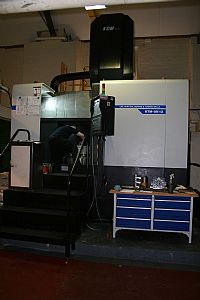
In four short years MG Sanders Company Ltd has witnessed a turnover increase of 40%, extended its floor space by 50% to 70,000sq/ft and increased its staff levels from 40 to 80. To support this growth level, the company has increased its number of machine tools to 50, with the latest addition being the UK's first KDM KTM9/12 Vertical Turning Centre from Leader CNC.
The Stone based manufacturer specialises in the low volume production of difficult to manufacture components for the aerospace, F1, nuclear and power generation sectors. The prestigious manufacturer is at the top end of the manufacturing industry, working with OEMs such as GE, MAN Diesel, Rolls Royce, Augusta Westland, a multitude of F1 teams and Triumph to name but a few. This has resulted in the AS:9100 approved manufacturer working on critical elements of marquee projects like the JET Tokomak nuclear project. To maintain its market position and reputation, investment in plant has been critical with over £4m spent in the last six years and a further £1m spend planned for 2013. This has seen the arrival of 5-axis HMC's and VMC's, turning centres and wire cutting machines from suppliers such as Doosan, Micron and Agie.
However, its the arrival of the KDM KTM9/12 in November 2012 that has really boosted the productivity levels and freed up capacity for the Staffordshire company. With the industrial power division of the company witnessing a fourfold increase in turnover in four years, a rigid and robust machine tool was required to produce pistons, cylinder heads and con-rods for marine engines, as well as critical diffusers, diffuser vanes and rotor shafts for gas turbine engines rated up to 2MW.
Commenting upon the acquisition of the KTM9/12 machine from Leader CNC, MG Sanders Managing Director, Mr Nick Farnsworth, comments: " We fully reviewed the marketplace but it was the exceptional build quality, the tooling set-up and the service support for the KDM machine on which we primarily made our decision. We produce one-offs and small batches of large parts that are machined from nimonics, titanium alloys, inconel and high chrome steels that require multiple set-ups, so for us it’s not all about cycle times and shaving seconds off jobs - its more about robust and rigid machines that will reliably and consistently do the job."
Highlighting the build quality, Mr Farnsworth says: " Upon closer inspection, the KDM has motors, drives and couplings that would be found on larger machines with tables well beyond the 900mm diameter of our machine. Additionally, the KDM can comfortably support our large heavy tools that can weigh up to 60Kg. This demonstrates that, although the machine may be a smaller model of much heavier machines in the KDM range, they haven't scaled down the critical elements. The build quality is outstanding and probably over-engineered, whilst maintaining a very competitive price."
This high build quality is an accepted fact with other Leader CNC’s machine tools at MG Sanders, like the Toshiba BMC800 HMC that was purchased in 2008 and two other Toshiba machines that are now over 20 years old. " Over the past 10 years we have replaced all of our machine tools except for the two 20 year old Toshiba machines. The Toshiba machines have done excess of 50,000 hours of machining whilst the BMC800 has completed over 15,000 hours in 5 years. In a facility that relies on 24 hour production for 5.5 days a week, these machines work non-stop and we never have any issues. In fact, Leader CNC is the one machine tool supplier whose phone number I don't have. This is because we never have breakdowns and the build quality of their machines ensures that they will last for 20 to 30 years - and this is what we expect from the KDM."
With regard to the tooling set-up, there are two big advantages on KDM machines. Turning tools are clamped onto a 240mm diameter Hirth coupling with a force of 7 tons for absolute rigidity and high metal removal, and the live spindle on the KTM09/12 incorporates a BT50 spindle taper – all major plus points for MG Sanders. The majority of machine tools for processing large parts at MG Sanders utilise BT50 tooling, so there was instant interchange capability between the KDM and other machines at the company. As Mr Farnsworth continues: " Amongst all the machines we reviewed to produce our industrial power parts, the KDM was the only machine offering BT50 tooling. To put this into context, we have over £1m of tooling on site, which includes front and back-ends. Acquiring more back-ends for compatibility with a new machine would have been expensive, increased our tooling inventory and would have reduced our ability to interchange tools between machines, which is pointless when we have over 2000 back ends on site. Completely new tooling for a new machine would have added up to 30% to the cost of a machine tool."
Already Reaping Rewards
Despite only being on-site for two months, the KTM09/12 is already making an impact at MG Sanders. In its first week of production, the KTM was turning marine pistons and machining cylinder heads at cycle times equivalent to the existing machining and turning centres. A fact that delighted Mr Farnsworth: " The KTM matched cycle times of our other machines on its first day and, in the longer term, we expect it to be 40% faster than our machining centres. This will effectively double our capacity for large parts, as the KTM can machine parts up to 4,000kg with a maximum turning height of 800mm. Additionally, we have been able to move batches of large parts like cast iron cylinder heads from our £600,000 HMC onto the KTM. The capacity saving is like having an extra £600k machine on site, whilst the surface finishes, accuracy and lead times are all improved, a credit to the KTM."
With a 12 tool carousel and driven tooling for milling and drilling operations, the KTM is capable of turning, drilling and milling the complex features on the cylinder heads with consistent accuracy well within +/- 5microns. Furthermore, the KTM is estimated to reduce tooling costs by over 70% in the longer term. Currently, the KTM is turning features on the cylinder heads with 4mm depths of cut at a feed rate of 0.4mm/rev. This material is being removed with heavy duty turning inserts. Previously machined on a HMC, a heavy duty indexable insert end mill or face mill would interpolate the features and rapidly burn through 10 milling inserts. The KTM improves surface finishes, with the added bonus of only using one turning insert mounted on the large 32X32mm tooling block. This capability can be credited to the rigid and robust 16,000kg machine weight and its frame of 4.8m height X 4.8m width and 3.5m length – all combining to provide optimal machining conditions.
The table, capable of swinging parts 1200mm in diameter, offers a rotational speed from 1 to 600rpm. Cutting feed rates are 30 M/min in the X and Z axes and the spindle speed of the milling head is 1 - 2,500rpm. The mechanical performance of the high specification machine is complemented by a powerful Fanuc 31i control unit and productivity rates far beyond alternate machine tools are possible. Reduced set-up times of the KTM are enhanced due to the ease of operator access to the machine table.
In conclusion, Mr Farnsworth says: " In the short period since the machine arrived, we have been delighted. It has drastically cut cycle times and tooling costs whilst massively increasing our capacity in the milling section. The service from Leader CNC has, as always, been excellent. This is why we are now looking forward to the arrival of our next Leader CNC machine."