Drill Manufacturer Improves Productivity & Quality Control With Blum Probe System
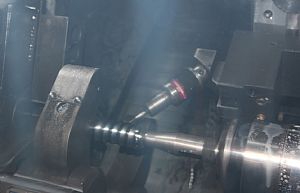
To be a world leader in a specified sector when you have a history that dates back to 1911, is something that is rarely found. However, Padley & Venables has found its niche as the leading UK manufacturer of construction tools that are sold worldwide.
The Sheffield Company has undoubtedly kept abreast of the latest industrial technology down the generations and combined this technology with the skill set and expertise of its staff; a blend that is combined with a relentless commitment to quality. It is this drive for innovation and quality that has seen the company install two Doosan Puma 3100M turning centres, a robot loading system and metrology equipment from Blum Novotest.
As the UK's leading manufacturer of high quality tools for rock drilling, quarrying, mining, tunnelling, construction, civil engineering and the demolition industries, Padley & Venables has subsidiaries in Germany and Australia with products being exported to over 55 countries around the world, so conforming to global quality methods is essential.
Discussing the company's most recent search for leading technology, Padley & Venables Quality Manager, Mr Steve Foster says: "We were getting to a point where we had to re-new some of our older lathes and we thought we'd take the opportunity to speed up the process by using automation. By doing this we have increased productivity by over 40%; and we can also run the cell unmanned at periods between shift changeovers."
The equipment that has delivered the 40% increase in production output is the robot for loading and unloading and two Doosan Puma 3100M turning centres that were installed as a complete cell; with the Blum Novotest Digilog metrology system completing the process. The new production cell at Padley & Venables is solely committed to manufacturing numerous families of steel drilling rods and connecting rods for the rock drilling industry on a 24/7 basis. Whilst the robot has eliminated the need for an operator to load and unload and the Doosan machines have improved productivity, the company would have still required an operator at the cell to check the finished parts.
Commenting upon the value of the Blum Digilog, Mr Foster continues: "The Digilog is central to the operation of the cell. Without the Digilog, we wouldn't be able to run the process as a robotised cell, as the operator would have to be present to put a gauge on every single component to check the parts conform to our stringent quality demands."
"Its pointless having an automated cell and having a guy stood at the machine opening and closing the machine to inspect every part. With the Digilog, the probe checks that the part is within tolerance. If the part is within the desired dimensions, the machine continues. If not, the probe stops the machine and alarms the operator to investigate further and the Digilog software shows where the problem has occurred on the integrated touch screen."
Quality and consistency is a critical factor for Padley & Venables as its product lines and bespoke components interact with parts manufactured by other vendors. In instances where Padley & Venables components are interchangeable parts of larger assemblies, precision and conformity to standards is critical.
In the cell, the Blum Digilog probing system checks the workpiece in-situ to ensure the part achieves the specified parameters. This ensures that quality and consistency are achieved before the component leaves the machine tool.
On the connecting rod parts on the Doosan Puma, the machine turns the thread and the Digilog follows the threading process to scan the thread and ensure the part is correct with no operator involvement. This allows the Sheffield Company to run the cell unmanned 24 hours a day if necessary.
Also attached to the Doosan turning centre is the Blum Contour Scan (BCS) 3.0 software, which is displayed on an industrial Windows based PC that is conveniently attached to the machine with a swivel arm. The BCS software shows the operator two individual displays and two sets of results. One screen gives the customer the nominal values as well as the details of the part that has just been machined whilst the second shows the current scanned result against the pre-set wear and extreme limits. This enables the operator to pre-empt tool breakages and prevents the occurrence of faulty parts. Beyond the pre-determined 'yellow' wear limit is a set of 'red’ extreme limits. These dimensional parameters signify a more serious issue that requires the machine to be stopped immediately
Commenting upon the installation at Padley & Venables, Blum Novotest UK Managing Director, Mr David Mold says: "Whilst this customer places a high emphasis on quality, the core reason for implementing the Blum Digilog system is to achieve a completely autonomous automation system that permits unmanned production and delivers the cost and productivity benefits associated with automating production. This successfully demonstrates that probing is not only applicable for precision manufacturing but should also be considered for automation."
"In addition, the application on the two Doosan machines highlights the ability of the Digilog to perform in harsh environments with swarf and coolant flying around the work envelope. Like all Blum probing systems, the Digilog incorporates our Shark 360 technology. The Shark 360 multi direction measurement technology is a patented design that has a face gear that significantly increases measurement accuracy when performing off-centre probing by using cranked styli. This is ideal for harsh environments such as measuring the form of threads on a turning centre covered in coolant and swarf," concludes Mr Mold.
The success of the Blum system has now led the Sheffield Company to look at a tool breakage detection package for two of its DMG EVO50 machining centres. The company is having issues with tool setting, operator error, and inconsistent tool life and machining performance. By installing the Blum Laser Control NT tool measurement and inspection probes, Padley & Venables will be able to automatically measure tool length and diameter parameters. The Laser Control NT will also monitor the wear on individual inserts, cutting edges and flutes. This will pre-empt catastrophic tool failures and prevent part scrapage caused by broken or damaged cutting tools.