DYSS Boxes Up The Perfect Package For Corrugated Case Company
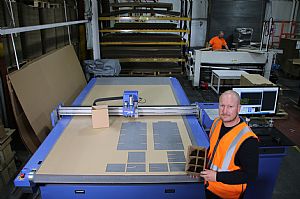
Recently reaching the landmark of its 20 year anniversary, The Corrugated Case Company Ltd (CCC) has set its stall out from day-one to invest in new technology and offer something a little different from its competitors. For the Chesterfield Company, this difference is identified with its Guarantee of Quality and Service or discount USP and an investment of over £1.07m in the last 12 months.
To facilitate its continual growth, CCC has invested in a 680 pallet, 13,000sq/ft distribution warehouse, a new, large format multi point glueing machine, an ink filtration system, and most recently a DYSS digital die cutter supplied by AG/CAD.
Arriving in March 2017, the DYSS X5-1630 digital cutter was purchased for two key reasons, as CCC Chairman, Tony Hession recalls: “We already had an AG/CAD KM sample table for over 12 years, and prior to that another AG/CAD machine that we originally installed back in 1998; although these both served us well, we wanted a faster, modern and more efficient solution with greater capability and production speed. The twofold reason was that our expansion has given us greater capacity and therefore we need to produce considerably more samples as the business moves forward. Secondly, we could see how PoS and digital print companies were applying digital cutting to small production run scenarios and we believed we could apply this model to our business.”
The daily business for the designer and manufacturer of corrugated cardboard and fibreboard packaging material is production runs of thousands of cardboard boxes and packages. However, the astute senior management team recognised an opportunity to manufacture small production runs with immediate delivery schedules. This was something that could be achieved by eliminating the design, production, cost and lead-time of producing and using cutting formes. By generating a CAD design or receiving a CAD file from a customer for a packaging design and processing it on a digital cutter, CCC could realise significant savings and an opportunity for fast-turnaround small production runs whilst reducing customer inventory and of course the cost of the cutting forme.
Why The DYSS?
“We did our due diligence by looking at all the options in the marketplace, but the DYSS X5-1630 from AG/CAD ticked all the boxes. It is a very fast, robust, well built and cost-effective machine. This complete solution was backed by our past relationship with AG/CAD. After already having AG/CAD machines for many years, we knew that reliability, machine uptime, service and support would be exemplary. None of the other machine vendors could offer our business anything capable of turning our heads.” says Mr Hession.
For a corrugated packaging manufacturer, the performance, rigidity and build quality were all key parameters in the selection of the 1.6m by 3m machine that would sit on a factory floor alongside heavy duty production equipment. Regarding the productivity of the machine, CCC Senior Designer Martin Higginbottom says: “The new DYSS is at least 3 times faster than the previous KM603 machine and we are now seeing a similar increase in the number of samples produced each week. As well as being 3 times faster, there is a whole range of additional parameters that are benefitting us with the new machine.”
For example, the previous machine would need blades changing sometimes 2-3 times a day to avoid ripping and dragging especially with lower grammage board grades. This cost us time in blade changeovers and we regularly had to scrap spoiled samples which would then require reproducing. The new DYSS uses different blade technology and much faster reciprocation allowing us to cut E-Flute through to BC and heavy duty up to 10mm thick without any snagging and with excellent edge quality. Blade changes are now only required every few weeks, so spoiled samples are a thing of the past. Additionally, the 1.6 by 3m bed is far bigger than the previous machine. This allows us to set-up and cut multiple samples from a single large sheet, saving us even more, time and effort.”
The powerful T-Head on the DYSS X5-1630 incorporates a high-speed reciprocating knife tool and a creasing tool plus the K-CUT Vision system that guarantees unparalleled accuracy levels when cutting printed sheets. The T-Head is driven by a high-precision AC servo motor, zero-backlash drive system which needs very little maintenance and is designed to last for decades.
Production as well as sampling
Whilst the DYSS X5-1630 has fully delivered on its ability to produce samples with greater efficiency and precision, this new model is also capable of generating far more detailed and complex samples than the previous cutter. This speed and capability has now been adopted for small production runs, just as the CCC team had envisaged.
As Mr Hession states: “Prior to purchasing the DYSS from AG/CAD, we approached our flat-pack customers asking if they would pay a premium for short production runs with immediate delivery schedules but with no tooling costs. We also pitched it as a service that would help customers in the eventuality that they may have placed orders with incorrect quantities or delivery schedules, or just needed urgent production capacity. This added-value service was met with resounding support and justified our purchase of the DYSS.”
At present, the new addition will often be found spending several days per week running short-run production jobs of 10 to 200 pieces, with samples scheduled around production. Using the DYSS X5-1630 for short production runs is having a significant impact for CCC. “Previously, we either had to subcontract out short-run work, charge a much higher rate, or turn it away based upon the £300-£500 cost of cutting formes and factory set-up times, which made it difficult to justify. No company wants to turn business away and using the DYSS means we no longer have to. It also ensures we win more business by reacting faster with better sample quality, whilst the short-run production facility is something that few businesses can offer with the level of cost and delivery parameters the DYSS provides us.”