Ellesco Develops Bespoke Surface Finishing Solutions with Autopulit
7 August 2014
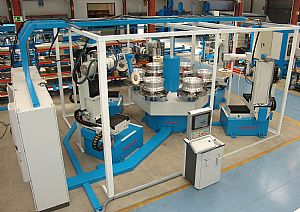
To complete the grinding, deburring, surface finishing and micro-finishing of anything from the simple to the most complex of components in production environments, Ellesco is now offering its complete line of Autopulit robotic polishing cells. Since working with the Spanish manufacturer of automatic and CNC machines for belt grinding and polishing, Ellesco has installed a large number of bespoke production solutions for some of the most prestigious names in UK manufacturing.
Autopulit has an established reputation as a deburring and surface finishing solution provider with an armoury that includes everything from manual belt grinding and polishing machines, rotary machines for finishing round parts, hydraulic coil polishing machines, alloy wheel polishing machines and even transfer machines with 10 working heads for the production of sintered parts. However, it is the flexibility, capability and the ability obtain consistently high quality surface finishes that has drawn the attention of some of the UK's leading aerospace, automotive, medical, white goods and plumbing manufacturers. The consistency of surface finish is of increasing importance to prestige OEM aerospace and automotive manufacturers, for whom impeccable quality levels and meeting minimum quality standards are the norm.
The robotic polishing cells from Autopulit are fully bespoke solutions that incorporate workholding pick and place storage units for operators to load new parts and unload finished components. The jigs and fixtures are fully manufactured to support the workholding of anything from the simplest to the most complex of parts in quantities that suit the application and production process. This can include multiple loading and unloading stations to feed one or two robot loading arms.
Upon collecting the parts, the precision robot will feed the parts through belt grinding heads, buff polishing heads and in some instances through drilling and threading stations prior to unloading completed parts. Whilst the Autopulit range is unique to the application of the end user, the company does manufacture base models that can be extended or configured to the needs of the customer. For example, the Autopulit CR-60/2UL robotic cell incorporates a loading and unloading station that indexes a magazine of parts, a robotic arm and two belt grinding units to finish the components.
For higher production demands, the Autopulit 2 CR-60 is a cell that consists of two robots with four belt grinding units, a large buff polishing unit, two indexed part magazines and a part exchanger between the robots. To complete the finishing of several parts simultaneously, Autopulit has developed its CR-165 manufacturing cell. This fully enclosed production station includes a loading and unloading robot, 3 polishing heads and a multi-spindle device for completing a number of parts simultaneously.
Commenting upon the increasing sales of the bespoke component finishing systems from Autopulit, Ellesco's Managing Director, Mr Guy Newton comments: "What we have found with the globally acclaimed OEM's is that demand for everything from UK manufactured vehicles to aircraft is on the rise. To increase production levels and achieve high quality surface finishes is undoubtedly a challenge. The combined expertise of engineers from Ellesco and Autopulit has delivered remarkable results whereby a robotic cell can comfortably sit within a production line environment to achieve the surface finishing and deburring quality demanded by OEMs on their high quality components in a production facility."