Engineering Solutions Acquires DMC Machines from Leader CNC
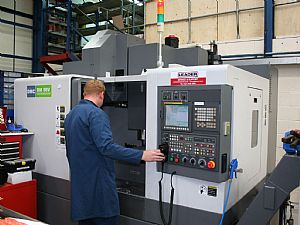
Like many business partnerships, the ambition and strategic desire of one director may be poles apart from their fellow directors. This appears a case in point for Newbury based Engineering Solutions & Supply Ltd, a company partnership that dates back to the early 1990's. Since, Managing Director Mr Nick Wright bought out his business partner four years ago, change has been exponential with the move to new premises and the acquisition of new machine tools for the subcontract manufacturer.
As Mr Wright takes up the story: "We have enjoyed considerable success down the years and when I initially took the reins, I had a 6 year plan but the strategy has moved at a rapid pace and the goals have been exceeded in a much shorter time frame. This year, we moved from our 4500sq/ft leasehold facility to a new 7000sq/ft freehold site and within a month of moving we took delivery of a new turning centre and machining centre from Leader CNC."
The company has always been a prototype and small batch subcontractor to the food, security, packaging and agriculture industries with an emphasis on complex parts turned around in extremely short lead times. However, the issue for Engineering Solutions was a difficulty and capacity shortage that prevented it from competing for larger batch work. That was until the arrival of the DMC DL21LMA CNC lathe and the DMC DM50V machining centre from Leader CNC in May.
The CNC machining section at Engineering Solutions has always had a one man, one machine policy. However, the rapid set-ups, ease of use and unmanned running of the DMC machines has enabled Engineering Solutions to allocate staff to other tasks, with 5 machines now being run by 3 operators.
Additionally, the capability of the new machines has eradicated many secondary operations and the consequent set-up procedures whilst simultaneously cutting cycle times.
When asked why the company opted for the DMC machines from Leader CNC, Workshop Manager, Mr Neil Hutt says: "We looked at a variety of other machines from leading OEMs and it was a compromise between speed, capability, build quality and rigidity. The DMC range unequivocally offered the best combination of these attributes within our budget. The DL21LMA turning centre with barfeed has given us the ability to run longer batches in the 500 off range, which we couldn't previously quote for competitively. Added to this, it has an extremely rigid build quality and tooling turret that can accept up to 12 driven tools. This has slashed cycle times, especially on parts that required secondary milling operations."
Highlighting the benefits of the DMC lathe, a batch of brass washer components previously had a cycle time of 26 hours - a time that included secondary ops on a mill and then finish machining back on a turning centre. The DLA21 LMA has cut this time from 26 hours to 6 and by doing the part in one set-up, component accuracy and batch consistency has improved. Furthermore, the DMC lathe has freed 26 hours of capacity from alternate machines.
With a powerful Fanuc 0iTD control, 8 inch hydraulic chuck and tailstock, Renishaw tool probing system, part catcher and a slant bed with efficient swarf removal, the DL21 has been a revelation for Engineering Solutions. The result of the powerful and easy to use control and the on-machine tool monitoring has reduced set-up times, improved precision and reduced re-work rates previously caused by tool breakages. For example, a batch of eccentric shafts with slots and flats were produced in batches of 14 with a turning time of 9 hours plus an additional 3 hours on a machining centre. This 12 hour cycle time has now been cut to a single operation with a complete batch machined in 5 hours, with the bonus of better surface finishes and improved precision.
The improved capability and processing time has enabled Engineering Solutions to extend its reach from small quantities and enter the small to medium batch spectrum of 500+ parts. This can be noted with a complex castle nut that previously would have been quoted with a batch production time of 60 hours, the company has now quoted and won the business with an estimated turnaround time of 30 hours, a job that would have been unlikely without the DMC lathe.
The benefits of the turning centre have been mirrored in the milling section with the acquisition of the DMC DM50 3-axis machining centre with a 30 tool carousel. As Mr Hutt continues: "When we looked at machining centres, the DM50 really stood out from other machines in the same price bracket. With linear guides, tool changes of 1.3 seconds instead of 3+ seconds, rapids of 36m/min, a robust BT40 spindle taper with through coolant and an extremely rigid build quality and a rotary table fourth axis, we have improved our capability for complex work and our capacity for larger batch production. This means we can retain our core prototype work and not lose the potential for the consequent production runs, because we now have the speed to be competitive."
One of the first jobs on the DM50V for Engineering Solutions was a batch of 200 bearing housings for the security industry. "This job previously had a cycle time of 19 minutes per part. The faster rapids, the 12,000rpm spindle and tool changes alone have cut the cycle time by 4.5 minutes per part. This is a considerable saving on a batch of 200. As we get a better feel for the new machine and its capabilities, these cycle times will continue to fall. In fact, we recently moved a mild steel lever housing from another machining centre to the DMC and it cut the cycle time for 48 parts from 35 hours to 22. So, the more familiar we are getting with the machine, the more efficient and beneficial it is becoming."
"As we become increasingly competent on both machines, the more we are witnessing benefits such as increased capacity, productivity, capability and precision. Added to this, the two DMC machines are allowing us to expand into new markets - something that will develop company growth as we move forward," concludes Mr Hutt.