ETG Expands Additive Offering with Chiron AM Cube
9 April 2021
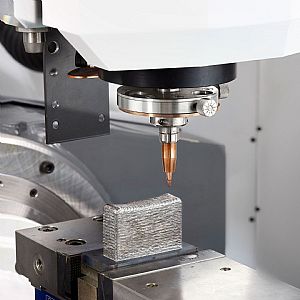
The CHIRON Group has expanded its core competencies to now include additive manufacturing. The new AM Cube that is now available from the Engineering Technology Group (ETG) is an easy-to-use 3D metal printer for manufacturing large and complex components.
The new CHIRON AM Cube is suitable for coating and repairing components up to 500mm and for cylindrical components up to 1m long. Perfect for the near-net-shape production of semi-finished products, the new arrival ensures CHIRON is recognised as a single-source provider of complete solutions for all components that cannot be produced using conventional manufacturing methods alone.
CHIRON has selected laser metal deposition as its technology of choice for additive manufacturing. With laser metal deposition, a feedstock material (Fe/Ni/Co-based) is melted using a laser beam and fused to the substrate by metallurgical bonding. One of the benefits of this process is that it results in lower thermal loading – it is also excellent for repairing damage, reinforcing components at selected points and restoring the original geometry of components employing material deposition.
With this technology, the laser beam of the CHIRON AM Cube melts wire as the base material, the melt bonds and solidifies. Complex geometries can be created in this way as the workpiece builds up layer by layer. The main advantage of wire is the high application rates. The laser is flexible and is suitable for both fine surfaces and large build-up rates. The material is supplied to the AM Cube using a coaxial - completely direction-independent process control with a wire. In order to avoid oxidation, welding is carried out with shielding gas in a closed system.
This process is also used in the AM Cube. The welding filler material is made from powder that is fed into the weld pool, which is ideal for thin coatings. Thanks to the coaxial nozzle, this process is independent of the welding direction. To ensure wear and corrosion resistance whilst accelerating the application process of the protective layer, AM Coating uses ‘extreme high-speed laser deposition welding’ (EHLA). The patented process is a further development of laser deposition welding and is ideal for coating brake discs. A special feature of EHLA is an innovation in process management whereby the metallic powder particles are blown into the laser beam and melt there instead of in the melt pool. The result is significantly higher coating speeds compared to conventional laser deposition welding.
Unlike other 3D metal printers, the deposition head on the CHIRON Group's AM Cube can be changed during an active printing/coating process. This allows different process requirements to be fulfilled. For example, one deposition head can be used to achieve a high-quality surface finish, while another can be used to achieve a high deposition volume. The automatic head change function enables these properties to be combined in a single workpiece. The AM Cube has three deposition heads in total and additionally allows the deposited material to be changed. Wire and powder can be deposited in different phases of the same manufacturing process.
The modular design of the new CHIRON AM Cube offers the flexibility for coating, 3D printing and repair whilst the automatic deposition head change allows wire or powder feedstock material, 3D printing plus internal or external coating as well as the facility for 3, 4 and 5-axis working. From an ease-of-use perspective, the CHIRON AM Cube offers its innovative user interface with CHIRON TouchLine, programming through DIN ISO or CAM and a cartesian coordinate system. The system is programmed either using a standardised DIN ISO code or a CAM system for complex components. All aspects of the system can be controlled using tried-and-tested Siemens components, from hardware to the HMI through to programming of the AM Cube.
From a technical perspective, the new AM Cube is equipped with a state-of-the-art sensor system and therefore fulfils all the relevant safety requirements, it does not need to be constantly manned. When working with highly reactive materials such as titanium, the entire system can be flooded with shielding gas to reduce oxidation. The maximum workpiece dimensions are 1m by 400 by 500mm for the 3-axis configuration, Ø300mm by 1m for the 4-axis platform and Ø500 by 500mm for the 5-axis set-up with a maximum load of 1,000kg for the 3-axis and 400kg for the 4 and 5-axis variants. The solid-state laser can be specified as a 2, 4 or 6kW power output with a beam quality of NA0.1 and a focus diameter from 1.2 to 4mm depending upon the selected deposition head. The new arrival provides an unprecedented number of optional solutions that make the CHIRON AM Cube the additive manufacturing machine of the future. For further details on this new modular concept, please contact Engineering Technology Group (ETG).