Exactaform Opens New Vollmer Machine Shop for PCD Cutting Tools
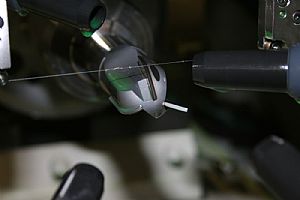
As one of the UK's leading manufacturers of specialised PCD tooling for aerospace, motorsport and general engineering applications, Exactaform has now expanded its operation to maintain its exceptional customer service levels. The Coventry based manufacturer has recently extended its operation with a new 4500sq/ft facility adjacent to its current operation.
The new unit is a dedicated specialist Vollmer machine shop for the eroding of its advanced cutting tool solutions. The machine shop accommodates seven Vollmer QWD and QXD wire and erosion machines and has been set-up to reduce lead times for its cutting tools. The move demonstrates Exactaform's commitment to providing impeccable service levels for its customer base.
Exactaform Director, Mr John Inglis comments: "The new machine shop enables us to improve the lead time for complex geometry multi-stepped tools from 6 weeks to 4 weeks and this will be a major benefit to our end users. The new unit allows us to create more space in our PCD brazing workshop and this will eliminate bottlenecks and allow us to push more tools onto our Vollmer machines."
The prestigious cutting tool manufacturer has grown at a rate of 25% year on year since 2009 and this increased level of business is destined to continue throughout 2012. To meet its growth demands, Exactaform has extended its workforce from 8 to 20 staff and also installed a fourth Vollmer QWD750H wire erosion machine.
A major factor in the success and growth of Exactaform is the capabilities of the Vollmer machine tools as Mr Inglis continues: "The Vollmer machines provide accuracy, consistency, quality and automation levels far beyond anything else available in the marketplace. The automation levels enable us to run our seven Vollmer's for up to 158 hours out of a possible 168 hours in a week. More remarkably is that we only need one operator to run the seven machines. At our rate of growth, we expect to fill our new facility with Vollmer wire and erosion machines in the next five years."
The Vollmer machines can maintain a tolerance band of less than 0.005mm consistently in a machine shop running 24/7 with exceptional surface finishes. It is this accuracy and consistency that ensures Exactaform customers can rely on repeatedly high quality tooling solutions. Additionally, the outstanding surface finishes on all surfaces of the PCD tips and the tool flutes improves product quality and surface finishes far beyond that of competitor tools.
The success of Exactaform has been built on its ability to provide technical tooling solutions for the machining of cast aluminium alloys and carbon fibres; all materials that are increasingly common with the resurgence of the UK's automotive sector and the growth in the aerospace and motorsport industries.
As Mr Inglis concludes: "With regard to machining cast materials and achieving outstanding tool life, more automotive manufacturers are turning to PCD multi-function tooling. Additionally, the increasing use of carbon fibre in the motorsport and aerospace sectors is creating a major demand for highly complex, PCD cutting tools. As one of the UK's major PCD tooling manufacturers with high specification machine tools, we are well positioned to respond to enquiries regardless of complexity. Looking at 2012, we will be launching two new PCD tool geometries specifically for our growing aerospace customer base."