F1 Subcontract Machine Shop Profits with Open Mind
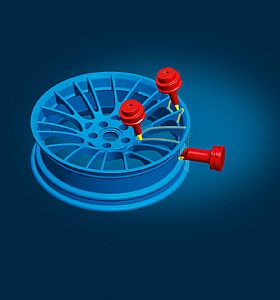
When Newbury based Progressive Technologies built a strong customer base of F1, medical, oil & gas, fibre optics, defence and aerospace customers in the middle of the last decade, the company noticed the increasing need for 5-axis machining to eliminate multiple set-ups. After acquiring its first 5-axis CNC in 2007, a DMG DMU50evo the business fully encompassed 5-axis machining and its incumbent philosophies to great success.
Moving from 3-axis machines that adopted the 3+2 axis machining strategy with rotary tables and fixtures, to full 5-axis machining proved more than just a case of buying new machine tools. As Mr Progressive Technologies Managing Director, Mr Ross Pinchin comments: “When we decided upon the DMG machine, we realised we had to consider a suitable 5-axis CAM package to get the best out of the machine. Our previous package wasn’t capable of meeting our needs, so we reviewed the marketplace and despite talking to the three or four main software vendors, the name OPEN MIND kept popping up among our peers.”
“When we discussed our involvement in the F1 sector with OPEN MIND and the machining of difficult 5-axis components, they took us to visit companies producing similar components for the F1 sector. We also visited some F1 engine suppliers and when we realised they had conducted an in-depth feasibility study among CAM vendors, which OPEN MIND was the clear winner, our decision was all but made, so we opted for the hyperMILL CAM package from OPEN MIND.”
HyperMILL Investment Eliminates Bottlenecks
Since 2007, the company has invested heavily in 5-axis CNC machine tools with over seven 5-axis machine tools on the shop floor. Up until two years ago, Progressive only had two programmers with four seats of OPEN MIND's hyperMILL. Now, Progressive has installed nine seats of hyperMILL. Highlighting the reasoning behind the additional investment, Mr Pinchin continues: "With such a high turnaround of complex parts, any problems on the shop floor had to be rectified on the machine or directed back to the programmers, and this created delays. As a prominent F1 supplier, our business relies upon our ability to turn work around rapidly. F1 sector 'rapid' has seen us receive orders after 8pm and turn it around by the morning. So, bottlenecks in the business have to be addressed."
To eliminate this bottleneck and enable machine operators to resolve any problems immediately, Progressive has now installed a PC at every machine tool and nine seats of hyperMILL. This enables the shopfloor staff to edit NC programs at the machine and this has made a huge impact on downtime and bottlenecks with machines no longer waiting for problem solving. Furthermore, the shopfloor can divert programs back to the office to improve the flow of information. The time being saved on the machine is significant but the time being saved in the office is just as critical. Confidence has also rocketed in the machine shop with operators able to view the component toolpaths prior to running the job.
Added to this, the subcontractor has invested in three hyperMAXX roughing modules that are incorporated into hyperMILL. The optional hyperMAXX roughing strategy creates ideally distributed milling paths. This is based on technology that enables dynamic feed rate adjustment to existing cutting conditions. This achieves the maximum possible feed rate and speed to decisively reduce machining times. What this has delivered to Progressive is a minimum reduction in machining time of 25% on most parts compared to using hyperMILL without the strategy. On other parts such as titanium chassis brackets for an F1 team, the time has been reduced from two hours to 30 minutes.
Despite drastically improving speeds and feeds, Progressive has noted significant tool life improvements. On a large titanium bracket that is regularly produced in batches, the 24 employee company previously used a £100 16mm diameter solid carbide end mill on each part. By turning on the hyperMAXX strategy, the company can now produce more than 5 parts with just one cutter. This is achieved by using the whole flute of the cutting tool with less aggressive toolpaths, which also reduces spindle load.
However, as a manufacturer that is always striving for methods to reduce downtime and improve productivity and quality, Progressive has recently added two seats of OPEN MIND's new hyperCAD package. Justifying this purchase, Mr Pinchin continues: "hyperCAD allows us to review and measure all geometrical dimensions and tolerances and add stock if necessary to ensure parts are correct to the drawings. Inspection and metrology equipment and its respective software is not necessarily easy to use, especially when calibrating the dimensions on particularly complex parts. hyperCAD allows us to set the origin of any particular plane and easily check and identify mistakes on drawings. Furthermore, we can fully interrogate our models, so the final inspection on the CMM is just a matter of double checking what we already know is right."
In the last two years, progressive has employed an additional five staff and seen its turnover increase by over 70%. "The increase in our turnover has been largely down to our ability to manufacture more parts and faster. The investment in additional hyperMILL seats to help us achieve this improved throughput has played a contributing part to this success," concludes Mr Pinchin.