FANUC Puts a Spring in the Stride of Press Tool Manufacturer
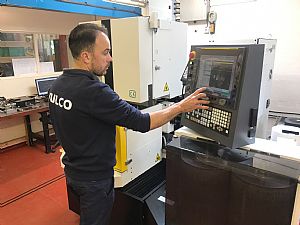
FANUC Puts a Spring in the Stride of Press Tool Manufacturer
With a rich history of manufacturing pressings and formwork, Vulco Spring & Presswork Ltd has maintained a strategy of investing in the latest technology to retain its industry-leading position. This path to success has recently seen the Redditch Company that manufactures electrical installations, brackets, clips; clamps, flanges and wire formed parts buy a FANUC Robocut C400iB.
Manufacturing in-house press tooling for its multi-forming machines and also its 20 to 70 tonne power presses, Vulco Spring & Presswork manufactures everything from one-off jobs on its machine tools through to long series production runs on its power presses and forming machines.
Commenting upon the arrival of the new FANUC EDM machine, Mr Joseph Draper, the Production Engineer at Vulco Springs & Presswork says: “We do have older EDM machines on-site but we’ve been struggling to locate the spare parts for these machines. Taking this into account, we realised we needed a new machine and FANUC assured us that its latest machines, like the Robocut C400iB that we bought, will be serviced and have spare parts available for years to come. This wasn’t the case with our existing supplier or alternate vendors. FANUC has an excellent reputation, an excellent product and the machine was supplied with a two-year warranty that gave us peace-of-mind. Added to all this, the FANUC was very cost competitive with its rivals.”
Referring to some of the key features that swayed the decision to buy from FANUC, Mr Draper says: “The high-speed automatic wire feed has been essential to our business and its one of the main reasons we bought the FANUC Robocut C400iB. This system will automatically feed the wire through a start hole and then the CNC program will begin to cut the job. Afterwards, this automatic feature will cut the wire, move to the next datum point and then process the next feature or hole. The machine will automatically continue to process hole after hole or shape after shape.”
“Previously, we had to manually feed the wire at the start point, start the machine and upon completion, we’d cut the wire and move the workpiece or wire to the next point. What this gives us is the ability to leave the EDM work for significantly longer periods without intervention. Furthermore, we can leave the machine to run through the night unmanned and arrive in the morning to finished parts.”
Peace of Mind Guaranteed
For a manufacturer less familiar with the opportunity for unmanned operation or lights-out production, the FANUC Robocut C400iB assures the end user with its impressive automatic repair system. Inherently, EDM users are all too familiar with the issue of wire breakage and the inconsistent control over the process, which is ultimately governed by the wire spool. However, the FANUC Robocut C400iB automatic repair function dissolves these concerns, as the automatic repair system will automatically repair the wire and continue production. Commenting on this function, Mr Draper says: “The repair system will pull the broken wire that is unsuitable to re-use into a bin and then re-feed new wire and re-start the production process. This is all completely automatic and requires no operator intervention.”
Regarding the precision of the FANUC Robocut C400iB, Vulco Springs & Presswork utilises 0.25mm diameter wire and this enables the West Midlands Company to cut its press tools to within a tolerance band of 5 microns. “This precision level is wonderful for us as we can produce fits and finishes into different locations with exact precision. This wasn’t possible with previous machines and this new level of precision has eliminated secondary operations and the associated times and costs involved.”
“Added to this, we get a far superior surface finish on the edges of our press tools. The surface finish is a critical factor for our business as the high-quality edge finishes significantly extends the tool life and process stability of the press tools we are manufacturing. The sharp edges are retained to a higher standard on our press tools and the end result is a higher quality pressed part.”
The new FANUC Robocut C400iB also gives Vulco Springs & Presswork the ability to cut to a depth of 200mm and beyond whereas the previous EDM machine had a maximum capacity of 125mm cutting depth. This added capacity enables the company to process a wider variety of components on the new FANUC machine.
The installation of a new machine and the associated technology can often be a daunting prospect. This Worcestershire Company had no such issues with thanks to the CAMi system and the Linki interface. The FANUC Robocut C400iB is equipped with a new Linki graphic interface. This updated production and quality information management tool allows customers to remotely monitor up to 32 ROBOCUT machines in real time, an Industry 4.0 feature for end-users. This user-friendly and intuitive system gives the customer access to preventive maintenance functions as well as consumable and repair services.
Referring to the specific needs of Vulco, Mr Draper concludes: “The Robocut CAMi CNC control software is a piece of software that runs absolutely perfectly with this machine. The software allows us to do absolutely anything with the machine and when we send the program to the machine, it does exactly as planned. The CAMi package also allows us to cut our parts up to 40% faster than before and this is a huge saving. When you add this saving to the overall productivity of the FANUC machine as well as the ability to run lights-out, you can understand that we are making massive savings with the new addition.”