Faster and as Accurate as Ever
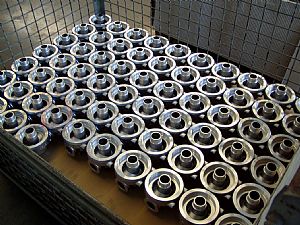
Ernst & Landerer GmbH is a family owned company with a proud tradition of serving as a partner to leading automotive gearbox manufacturers. The company actively looks towards innovative technologies to improve their products rather than rely on structures and proc-esses that have developed over time. Achieving increasingly faster speeds and keeping processes economical, while delivering the same accuracy and quality, calls for constant advancements. For Ernst & Landerer, continuous progress is a way of life and Blum-Novotest’s measuring technology makes a major contribution.
The family run foundry has 80 employees and aims for this figure to rise slowly, with a focus on optimum product quality while maintaining the company at a manageable size. Established as a pure aluminium chill casting foundry more than 40 years ago; the company has customers from the automotive, medical, mechanical engineering and construction industries that no longer require unfinished, raw steel parts. Customers now demand ready to install cast products and as a result, mechanical production was added to the casting process at the turn of the millennium. Since then, it has become the company’s largest area of business, running a 2-shift system with 22 Haas machining centers. Between 30 and 40 percent of the parts produced are supplied to gearbox manufacturers – high precision components with j6 tolerances, h6 for diameter boring and 1/100mm variances in rectangularity and parallelism.
Tailored Equipment
“Because it was what our customers needed, we have increasingly specialised and im-proved," explains Thomas Ernst, one of the company directors. The unfinished parts are cast with minimal machining tolerances. For each workpiece, there is a dedicated piece of equipment for clamping it on the processing machine. The tolerances for the components are so stringent that almost all parts can only be clamped once for the entire machining process. Depending on size, up to four components can be produced simultaneously in one pass. For years, the parts were transferred to a 3D measuring machine for measure-ment after machining.
This measuring was essential but very time consuming. If finished components were found to have a tolerance deviation, rework was only possible at very high cost. It then became a logical solution to measure the components in the machining center itself. For example, the last component produced was measured with a tripod type measuring in-strument that was used to manually measure a particular diameter. If it still complied with the relevant tolerance, all previously bored diameters also had to be within the tolerances.
For some time, components at Ernst & Landerer were measured this way. On the one hand it was time consuming, as the machine had to be stopped during the measuring process, while on the other hand, it was susceptible to errors as measurement was carried out manually and the measuring method required the surfaces to be completely clean.
No Downtime
A better solution was needed and came to light in the form of in-process measurement. Two of the machining centers came with a probe from a measuring technology manufac-turer and this allowed measuring during the machining process for the first time. However, it soon became apparent that measurement with these probes took offered remarkable measuring speeds.
Thomas Ernst and Jürgen Hinkofer travelled to a measuring technology workshop run by the supplier, Blum-Novotest. The casting specialists were delighted with what they found, and while there, submitted their first order for tool and workpiece measurement probes. Six months later, the number of probes was increased. More new machining centers were added over time, including a horizontal machining center with a pallet changer and a cell for 6 pallets. This new machining center was also equipped with measuring technology from Blum-Novotest. Now, every machining center at Ernst & Landerer that produces high precision parts is fitted with Blum’s Z-Nano tool probe and a TC52 probe. In total, more than 25 systems from Blum are now in use.
Complaints are rare
“All gearbox parts produced with strict tolerances are now measured using the Blum probes. We have simply discovered that it is actually a fast and reliable process. There were few complaints even before the introduction of measuring technology from Blum-Novotest; however, since the probes have been in use, this figure has decreased even further. From a product range made up of high precision gearbox parts with around 20,000 manufactured every year, fewer than ten workpieces were returned with complaints in 2010," Thomas Ernst explains.
As the director of Ernst & Landerer describes, "Using Blum’s probes has significantly in-creased the availability of the machining centers. Inspection of the workpieces was ex-tremely stringent in the past, so the number of rejects has not fallen significantly overall. However, it used to take considerably longer and with Blum's measuring technology, the processing times are lower and process reliability has improved significantly."
Extremely Fast Broken Tool Detection
Compared to other metal processing methods, structural irregularities are common in cast-ing and can be caused by impurities. For example, ceramic particles in the casting can cause premature wear on the tool. When it comes to bores with diameters of just a few millimeters, the tool can often break. If a tool was broken or not working correctly during machining, this could previously only be identified by a visual inspection after completing the entire machining cycle.
Since the implementation of Blum’s Z-Nano tool probes, no more parts have been pro-duced at Ernst & Landerer where employees identify a missing thread at the end of the process because a broken tool had not been noticed. Each individual tool is moved to the Z-Nano tool probe after machining the component and checked in a matter of seconds. This ensures that the tool is functional and that the corresponding machining operation has actually been performed. If the Z-Nano detects any damage to the tool, machining is stopped. The employee then replaces the tool and the machining program continues. The Z-Nano tool probes allow tools with a diameter of above 1/10mm to be measured. When the tool comes into contact with the interchangeable measuring surface, a miniature light barrier is shaded inside the Z-Nano. A skip signal is generated capturing the current ma-chine axes, allowing the control to calculate the tool length.
The Z-Nano is now used to perform the length measurement check on tools at Ernst& Landerer with a repeatability of 0.2µm. At present, no temperature compensation is carried out, although the Z-Nano is able to do so. Measurement of the tool also ensures that the thread has actually been cut correctly. During machining cycles it is possible for the thread cutter to be pushed back into the collet. This reduces the thread depth and was previously a problem in the production of high precision components. Another problem was a borer getting stuck in the work piece without being noticed. Subsequent tools were then also destroyed by the resulting collision.
Finding the Workpiece Location
As well as the Z-Nano, the TC52 probe has also become an indispensable part of produc-tion at Ernst & Landerer. The probe’s measuring mechanism has a symmetrical, circular design, which gives it repeatable measurement behaviour when measuring from various directions. In the chill casting foundry, it is used for zero point detection, verifying clear-ances and for monitoring the position and orientation of the workpiece. In order to be able to machine a component completely in its original clamping position, the employees at Ernst & Landerer have developed a mechanism whereby the component can be turned and oriented. Based on the TC52’s measurement of the workpiece, the position is known to micron accuracy and orientated as necessary.
Rapid Measurement in a Coolant Intensive Environment
During inspection with the TC52 probe, the coolant continues to flow in the same quantity as before. The probe operates with a slightly higher measuring force and requires a certain amount of deflection to generate the skip signal. With this probe design, coolant on the surface of the workpiece does not lead to an incorrect measurement. When the opto-electronic measuring element generates the skip signal, the machine’s axes are simultaneously read and stored in the controller memory. This means the actual position of the workpiece and other measured values are available. The non-contact, opto-electronic measuring principle ensures the measuring element on all Blum probes is wear free, allowing maintenance free use over a longer period.
This is just one of the reasons why Thomas Ernst is satisfied, commenting: “Previously, we were able to produce excellent parts with precise dimensions, but it involved much more measuring time and work."