Floyd Improves Hole Accuracy For Motorcycle Subcontractor
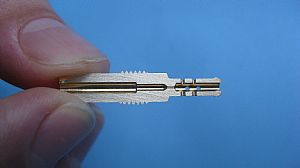
When A-BAX Precision Engineering Ltd was having difficulties in achieving holemaking concentricity and accuracy on a new order the company won, the scrap rate and re-working rapidly escalated. Looking for a solution that would improve concentricity, accuracy and repeatability with its small hole drilling, A-BAX turned to Floyd Automatic Tooling and its Mowidec-TT Spindle centring system for the answer after facing some difficulties in achieving using conventional methods.
Since its inception over 7 years ago, A-BAX has been manufacturing motorcycle components in batches from 150 to 2500 on its Tornos Sigma turning centre. Over the last three years the steady growth of the business is the result of a new order to manufacture 75,000 brass pilot jets for a global motorcycle distributor. However, the intricate and precise pilot jets that can be up to 28mm in length, require a hole through the centre with a concentricity of +/-5 microns, and this is where the Mowidec spindle centring system has come into play.
As A-BAX Managing Director, Mr Alan Baxendale recalls: "We produce 12 different families of pilot jets with between 20-30 sizes per family, all with a through hole of between 0.3 and 0.7mm diameter. The issue we had was the inlet/outlet venturi counter bores need to be concentric with each other, otherwise any small deviation would result in the much smaller pilot hole drills being deflected on entry resulting breakage/scoring or a burr occurring on uneven break out, which would not be so exacerbated, if simply drilling through two parallel flat faces. So, it was essential that all the related holes were concentric with each other in order to eliminate these problems."
"Clocking the drills and reamers on the main spindle side of the machine proved difficult as sliding head machines don't offer much space for movement with the restricted space between the guide bush and tooling. In most cases, it meant the guide bush had to be removed. To use the main spindle, the process had to be interrupted to re-heat the machine because it took so long using a DTI. This meant measuring and consequent part checking had to be done with hast, as the smallest thermal variation in the machine during downtime could cause further inaccuracies."
"Now with the Floyd Automatic Mowidec system, this can be achieved more precisely in one hit without removing the guide bush. We also found that we can set up the main tooling in the counter spindle more precisely for the same reason. We are now clocking the tool itself rather than suffering the deviation between the collet cone, collet and the tool tip, which we experienced using the DTI method. Only by repeatedly clocking the collet cone and undertaking numerous inspection and pre-heat cycles, we managed an acceptable result. Floyd Automatic offered us their Mowidec centring system that accurately clocks the cutting tools and compensates for any deviations.
With the Floyd Automatic Mowidec centring system there have been no drill breakages or burrs and the company has improved surface finish and substantially reduced setup time and the excessive inspections. The pilot jets have been a breeze with massive time savings and a 0% scrap rate."
As a machine shop set up for production runs, A-BAX would run six different batches consecutively, so 6 pilot drills had to be clocked with the jobs checked mid-cycle with an eye-glass/ sectioning to minimise scrap. The 6 pilot hole drills on the counter spindle would take upwards of 1hour per shift for each consecutive batch runs. Added to this, the company was spending up to 5 hours a day inspecting the parts that generally yielded a scrap rate of between 5-10%.
As Mr Baxendale comments: "The Tornos Sigma that produces the pilot jets allows us to have the number of tool positions we require to make such a large number of parts/size variants, but its a 25mm machine isn't normally suited for the extreme precision demands of such small detailed parts, unless the tooling is clocked precisely and thermally stable. So, Floyd Automatic's Mowidec system has allowed us to achieved/enhance the machines capabilities beyond that normally expected for this size of machine."
The new Mowidec-TT centring process can be done without removing either the guide bush or the tools. The system is capable of checking the alignment of the headstock, guide bush and sub-spindle. The Mowidec digital read out control panel can be mounted on the machine housing with a magnetic pad, so the user can see a clear indication of the measurements to within a micron. Incorporating an electronic proximity sensor, the Mowidec-TT gives the end user a precise measurement without any contact.
The sensor is mounted in position using an adaptor ring fitted to the bar in the case of the main spindle or the nose cap for the sub spindle. The tool is manually moved into position with the sensor moved to within approximately 0.50mm in the X-axis (close enough to register a reading). The unit is re-set to zero. The spindle is turned 180 degrees. The display unit will indicate the error which can be corrected by half with the machine offsets. The process is repeated for the Y-axis.
As Mr Baxendale continues: "For a series run of 6 batches that would total 3000 parts and be produced in one-hit, I would spend almost three to four hours a day setting and re-setting drills. This is now one hour a day. The inspection time would be 4 to 5 hours a day and this is now 1.5 hours a day. The Mowidec has completely changed everything for us."
Other time reductions have arrived from the extended tool life created by the Mowidec system. Using solid carbide drills that were specially made, A-BAX was breaking in excess of 3-4 drills a week. Drills no longer break and are only replaced due to wear. "The special drills are expensive to replace and there is obviously the downtime created by tool changeovers and then the scrap created by the drills. This has all now been eliminated. Furthermore, our longer batches can run for 24 hours without any intervention, giving us confidence in our lights-out machining. Before the arrival of the Mowidec-TT system, we would come into work in the morning expecting parts with holes off-centre, which always required extensive inspection. Furthermore, broken drills meant we had to work back through the batches to eliminate the scrap parts."
"The Mowidec-TT has delivered revolutionary change to our tool positioning and precision levels of a specialist micro turning centre of our 25mm capacity sliding head. We are always looking at ways of improving our operations and this has defiantly been one of the best decisions we have made especially to this and all our machines capabilities," concludes Mr Baxendale.