Floyd Launches Time Saving Spindle Centring System
6 August 2012
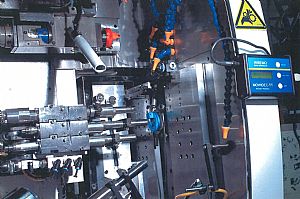
As the leading industry specialists in the provision of tooling and associated products for sliding head turning centres, Floyd Automatic is delighted to now offer the Mowidec-TT spindle centring system.
The new Mowidec-TT that received its UK exhibition debut at MACH is a spindle centring system that enables the user to perfectly centre tools on the main or counter spindles to improve accuracy, performance and tool life with a simple and fast method on Swiss automatic lathes.
When changing the set-up or settings on an automatic lathe, operators frequently have to re-centre the spindles, usually with a dial test indicator. Whilst this can be conducted in a number of ways, the process is so restrictive that operators often prefer not to do it at all - resulting in poor quality, precision and premature tool wear.
With the Mowidec-TT, centring is carried out without removing either the guide bush or the tools. It is conducted without any complicated equipment or training and is so simple that users start centring systematically, thereby benefitting from enhanced tool life and productivity.
With some small adaptations, the system is capable of checking the alignment of the headstock, guide bush and sub-spindle. The Mowidec digital read out control panel can be mounted on the machine housing with a magnetic pad in a position where the user can see a clear indication of the measurements to within a micron. Additionally, the system can offer an imperial measurement display by the touch of a button. Incorporating an electronic proximity sensor, the Mowidec-TT gives the end user a very high precision measurement without any contact.
An adaptation ring is fitted to the spindle and it contains a contactless transversal sensor. The tool is manually moved opposite the spindle with the sensor positioned visually at short range. The unit is re-set to zero, the spindle is turned 180 degrees and the unit shows an error in the diameter vertically. All that remains is to correct the machine offsets by half (radius error), reset the unit to zero and rotate the spindle to its original position. Any residual error appears on the unit to the nearest micron. To correct the position horizontally, the spindle is then rotated 90 degrees and any error is displayed. This axis can then be corrected either mechanically or with the software. This procedure is suitable for aligning the drilling spindle in relation to the headstock.
By simply changing the sensor bearing ring, it is possible to re-align the secondary operation machine spindle or even the spindle and counter spindle simultaneously. The system can be used for any instances of an alignment problem and remains the same for all machine types, only the adaptation ring is different.
This exciting new innovation is ideal for all types of Swiss automatic lathes from manufacturers such as Tornos, Star and Citizen. Additionally, the Mowidec-TT can also be used for many other applications such as multi-spindle lathes, transfer machines and machining centres. The technology behind this new innovation that is now available from Floyd, drastically reduces set-up times regardless of machine type. With quality at the heart of the Mowidec-TT, the unit has been developed to significantly improve the service life of cutting tools and component quality, whilst seamlessly fitting into the machine set-up.
The simplicity of the system is epitomised by its digital read-out with three buttons for resetting, choosing the measuring mode (imperial or metric) and the measuring unit or resolution. The installation of the Mowidec-TT is also a straightforward exercise with only the electronic unit, power supply cable, USB connection cable, two proximity sensors and the adaptor rings required.
The philosophy of the Mowidec system is that it is first and foremost a system for making a comparison between two points, and not a measuring device. The actual measurement can vary according to the type of sensor used, the distance to the probe and the diameter of the cutting tool. When all these parameters are considered, the Mowidec-TT provides a comparative measurement of several points as opposed to the actual measurement of a specific point.
The system is very easy to use. The customer receives a case containing the device, sensor, cables and a set of rings that are colour coded for each diameter. The power supply is connected using the machines socket and the sensor is connected to it with a single USB port. The operator attaches the unit wherever he believes it will be most effective, the ring is fitted and measuring can commence.
This technology is new to the UK market and proved a resounding success at its first outing at MACH. For further details on how the Mowidec-TT can improve productivity, tool life and overall component quality, please contact your local Floyd Automatic representative.