Floyd Sorts Success For Production Manufacture
7 May 2014
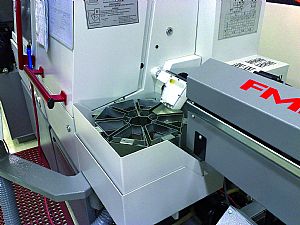
To improve the inspection of randomly selected parts during series production runs, Floyd Automatic can now offer the new Schwanog Selector System. This innovative new component selection system divides loose production batches into bins consisting of up to eight smaller units. In the case of lights out or unmanned production, sorting costs and time invested can be drastically reduced in the case of tool breakages or alternate disruptive factors.
The new Schwanog Selector System can partition production batches into smaller quantities through its eight selector bins. The eight component compartments can be indexed automatically using time or quantity settings that are pre-determined by the end user. The bins are located on an indexing table that rotates when the bin achieves its pre-determined quantity. Fed from the part conveyor/chute of the machine tool, the exceptional new Schwanog system is completely flexible and can be a productivity partner for machine tools such as single spindle turning centres, multi-spindle automatic lathes, rotary transfer machines, punch and stamping machines, gear cutting and spring coiling machines plus many more.
Completely flexible, the Schwanog Selector is a compact plug-and-play unit that can be moved from one machine to the next to suit the production demands of the customer. The flexible system is available in four individual models, the 200, 270, 420 and 570. The various models have an overall diameter from 230mm to 475mm with bin dimensions suited to the varied part length and diameter requirements of the end user. This enables the selector to sit comfortably in front of a machine tool without excessive space requirements.
From an inspection perspective, the Schwanog unit drastically improves the time taken with visual inspections. If the parts in the last bin are inspected and correct, then the parts in the previous seven bins will also be 100% correct. However, if faulty components are found, the operator can work backwards and rapidly arrive at the correct parts or point of failure. For the end user, the benefit is that allocating the point at where a fault occurred and parts are scrapped can be narrowed down to one part bin as opposed to inspecting a complete production batch. The time and scrap savings for the end user can be considerable. With the market for precision turned parts in the automotive, aerospace, medical and alternate industries demanding medium to large batch numbers of exceptional quality and zero error tolerances, the Schwanog Selector System is a must have solution for the modern machine shop.
For sensitive parts that cannot have scratches or surface imperfections, Schwanog has developed over-floating, oil-filled double bins. These bins have been developed to catch the parts and eliminate the potential for quality reducing marks to the components. This is of particular interest to customers machining parts manufactured from relatively soft materials, parts requiring a high quality aesthetic finish or parts with intricate and sensitive features.