Freddy Sucks Up Enquiries at MACH 2012
2 May 2012
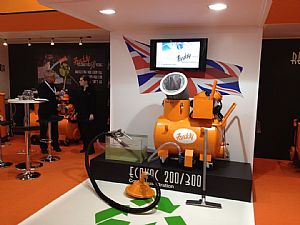
Freddy Products celebrated its 50th Anniversary in style at MACH with an attractive stand design that was a great platform for the company to exhibit its exciting new Centrifuge system for the re-cycling of oil, coolant and a multitude of additional fluids.
As a market leading provider of centrifuge systems with a brand image that is synonymous with impeccable quality, Freddy's products were well received among MACH 2012 visitors. As Freddy's Managing Director, Mr Simon Hanmer comments: "Freddy is a brand globally recognised throughout industry and we were delighted to re-introduce our brand to the UK's leading manufacturing event. The response we received at MACH was amazing. We generated a huge number of high quality leads from new customers as well as customers that have been using our products for over 25 years, which proves the longevity of Freddy products."
"MACH was an opportunity for us to educate our existing customer base as well as approach potential new customers with regard to the possibilities of what our products can provide. We found that many companies have been running our products for decades and not using them to their full potential. With the continually increasing cost of oil, many manufacturers are disposing of coolant without recycling through one of our machines. This is effectively pouring thousands of pounds of coolant away each year, whereas using one of our machines can prolong the life of the coolant, saving thousands of pounds each year."
At the UK's showcase manufacturing event, Freddy demonstrated how its new HP20-22 High Performance Centrifuge system and additional Freddy innovations can resolve problematic issues that surround oils and coolants in the workplace as well as highlighting the company's green credentials.
The new HP20-22 Centrifuge delivers particle filtration down to less than 5 microns - far below the standard 10 micron level offered by many systems. This prevents swarf and dust particles returning to the work envelope, which cannot be guaranteed by competitor products. Ineffective filtration and the return of waste particles to the work area can be detrimental to surface finishes, tool life, machine service cycles and most importantly the health and safety of machine operators.
The new innovation works by feeding contaminated coolant through the connection lid and this is then deflected by the centre cone to the base of the rotating bowl. Centrifugal forces then act upon the dirty coolant to pack the contaminants into a cake at the wall of the rotor liner. The clarified fluid then overflows at the top of the unit through the vane assembly that returns the clean oil to its machine tool.
With its single rotor clarification system, the new HP20-22 offers throughput levels of up to 80 litres/min of soluble oil with marginally reduced rates for neat oils. The exciting new clarifier will be fitted with a solid state inverter device that is complete with a lid-lock to ensure the clarifier lid cannot be opened as the system 'ramps down' to a complete stop. Likewise, the new unit cannot be re-started with the lid in the unlock position. This automatic lid-lock fully conforms to the Health & Safety at Work Act to guarantee the safety of operators. The inverter drive increases the speed of the centrifuge rotor, which in turn increases the forces being exerted on the solid particles to maximise efficiency.
The HP20-22 unit is available with 380,400, 460 Volts with 3 phase 50/60 hertz supply that is operated with a push button start. The extremely flexible units can be supplied on a trolley with wheels to enable the end user to move the centrifuge from machine to machine.
Concluding on the event, Mr Hanmer states: "Freddy undoubtedly made its mark at MACH and we are delighted with our response levels. Additionally, we sold a number of solutions and consumables from our stand, which truly made the event a worthwhile exercise."