From the garage to global market leader with Tornos Turning Centres
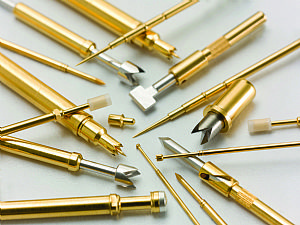
What do you say to a lathe operator who usually turns highly complex parts with an outer diameter between 0.4 and 0.6mm? Kudos! Ingun Prüfmittelbau GmbH started in a garage and has developed to the global market leader in the fields of test probes and test fixtures within just a few years. Since 2014, the company has been applying the technology of the Tornos SwissNano machine that has been contributing its share in this success story.
In 1971, the company Ingun Prüfmittelbau GmbH headquartered in Konstanz, Germany, opened its doors for business with the production of test probes and test fixtures. At that time, 7 employees were involved with the production. Now, the staff has grown to more than 300 employees world-wide and Ingun Prüfmittelbau GmbH is one of the top players among the test equipment experts.
Many electrically powered products such as harnesses used in cars, battery packs for bicycles or state-of-the-art smartphones, laptops and PCs are tested for correct operation with an Ingun product. As such devices are getting smaller and smaller and smarter, it is inevitable that their PCBs are getting smaller whilst featuring more functions and closed-loop control circuits. Examining and testing PCBs is becoming more and more complex and Ingun is making every effort to continue coping with these technical challenges as they evolve.
The complexity of the products is not particularly evident at first sight. They consist of a barrel, a spring, a plunger and a probe with gold-plated tip. It's getting really interesting, though, when it comes to the sizes and the material to be machined. For Ingun, outer diameters smaller than 0.8mm are already large and the turning of 0.12mm cross holes and of 0.19mm studs are usual tasks. For the most part, brass as well as copper-beryllium alloys are machined. Most recently, the share of Teflon and other plastics has also been increasing as these materials have inherent insulation characteristics.
In 2012, the business management followed the plan conceived by Thomas Wind, Head of Purchasing, to establish its own turning shop. In the first place, this idea came up because the time slots between engineering, prototype construction and test phase were becoming smaller and smaller. Under these circumstances, external suppliers were quickly reaching the limits of their capacity. Thomas Wind regards 'his' turning shop as the forefront of technological development.
In close collaboration with the design engineers, new solutions are sought and new technologies are experimented with. Set-up times of two to three days with subsequent machine operation times of just 20 minutes are not uncommon. "For parts of 1mm length and 0.07mm wall thickness, discharge rather than production is the real art," Nick Symanczyk, Ingun’s engineer responsible for Tornos machines declares. "If we hadn't installed an integrated special pick-off device, it would have been difficult to distinguish in-spec parts from chips." As soon as a process is running steadily, it is outsourced to external local suppliers who will produce about 80 million turned parts per year. The fact that the turning shop is now equipped with 11 machines proves that Thomas Wind's plan was right.
A further step forward with SwissNano
A highly complex test probe with a crown on its face pushed the machines that had already been used to their limits. Therefore, Thomas Wind and his team were looking for a new means of production. In 2014 the company saw the SwissNano machine that had just been launched by Tornos. The technical parameters perfectly matched. The machine is small, compact, easily accessible, stable and precise. In the course of elaborate turning trials in Pforzheim, Germany, the machine showed what it had to offer. In this context, the team unanimously praised the support offered by Tornos.
Together, they developed solutions for process optimisation. With a shortened bar loader, the vibration could be further reduced. In this regard, the specific oil extraction system and the pick-off device directly mounted on the spindle are some very interesting features. Such details emphasize the high demands Ingun makes on its machines. Ingun does not content itself with the standards and is always looking for improvement.
Only good experiences
The person in charge of the Tornos machines at Ingun is Nick Symanczyk, a young man with huge commitment and enthusiasm. "It really makes it fun to work with the machine. It is amazingly fast and what is particularly important to me is the easily accessible and easy to set-up." With an annual ratio of two thirds set-up work and one third turning work, these reflections are all too understandable. The possibility to change over in 'next to no time' between turning with or without guide bush and the resulting flexibility are features that prove popular as well.
Another aspect applauded by the operator is the TISIS software. "I have felt at ease with it from the very beginning. The machine is easy to program; important features are already registered and the simulation function provides reliable protection against collisions and opens up possibilities to further optimize the program." In view of so much positive experience, it is not surprising that another SwissNano was purchased in 2014, followed by two additional machines that were acquired in 2015. Thomas Wind is already thinking about purchasing another SwissNano, especially because he considers the service and the customer support provided by Tornos to be exemplary. Thanks to customized solutions that were realized on the SwissNano machine within two weeks, the company managed to land two big orders that would not have been possible in earlier times. Another chapter has thus been added to SwissNano's success story and it's going to be interesting how this bestseller will evolve.