GE Engineering Speeds ahead of Competition with hyperMILL
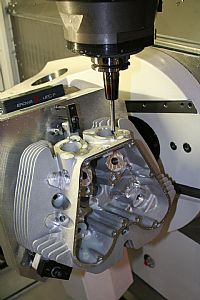
There is never more of a truism than ‘you get what you pay for’ and this is definitely the case at GE Precision Engineering (GEPE). When the company opened its doors for business little over four years ago, like most start-ups the Northampton based company purchased equipment within its budget constraints.
The acquisitions included a number of second hand machine tools and low end CAM software to program its parts and the truism was duly noted by Company Founder and Managing Director Mr Garry Edwards. As a motorsport engineer, Mr Edwards left his post at Ilmor to set up GEPE to service the motorsport industry. To work in this industry, high specification machine tools, CAM software and highly qualified and experienced staff are a pre-requisite.
To meet such demands, Mr Edwards invited three highly skilled ex-colleagues to join the company as directors and when it was financially feasible, the company invested in 5-axis machine tools. In the four years of trading, this has included a DMG DMU50, a seven pallet MikronUCP600, a Hardinge XR60-5AX and Doosan turning centres with driven tooling. However, the most important purchase for the 17 employee business has been CAM software from OPEN MIND Technologies.
As Mr Edwards confidently states: “The hyperMILL package from OPEN MIND is undoubtedly the best decision I have made for my business. Four years ago we initially acquired a CAM system based on cost and even during the training period, I knew it wasn’t capable of meeting our needs. Nine months later we bought our first seat of hyperMILL. I have been trained on all CAM systems and spent many years competently using CAM systems from ALL manufacturers. My vast experience has seen me actually support some CAM vendors. So, when I say that OPEN MIND is the best available package, I am speaking from years of experience with ‘ALL’ CAM systems.”
The selection of hyperMILL occurred when GEPE was awarded a contract with a leading F1 Engine manufacturer to produce CAM covers from solid billets. Mr Edwards was given a demonstration of hyperMILL at the F1 team and immediately realised how easy it was to produce complex shapes and forms. As Mr Edwards continues: “The demo really opened my eyes to the capabilities of hyperMILL, but most importantly how easy it was to program complex 5-axis forms. It was streets ahead of anything I had previously used, so the decision was immediately made.”
The ISO: 9001 registered company is embedded in concept, design and consultancy projects with its customer base. Despite the Motorsport expertise levels of the directors, the company made a conscious decision during the recession to explore new markets. This now sees GEPE working with manufacturers of radar systems, engines for Unmanned Automated Vehicles (UAVs), the “Ultra Boost” engine project, Norton motorcycle engine projects and a reverse engineering and manufacturing project for English Premier Shotguns.
Commenting on the shotgun project, Technical Director Mr Scott Bredda states: “The English Premier Shotgun project is a good example of how we reverse engineer products. Each part is assessed with respect to its form, fit and function. We assess the manufacturability of the part i.e. work holding, tooling, cycle time, etc. Ultimately the aim is to replicate and where applicable, improve the design, manufacturability, material and cost. hyperMILL has been invaluable in the huge production engineering exercise that has taken place.”
Regarding the UAV project, we are at the forefront of developing engine technology for this market, which has the potential to expand exponentially. Again hyperMILL is being used extensively in the production engineering of all the engine components.
The Ultra Boost project is another example of where GE can exploit its design and manufacturing expertise. The project consortium is led by Jaguar Land Rover and includes Lotus Engineering, GE Precision Engineering, CD-Adapco, University of Leeds, Imperial College London, University of Bath and Shell as partners. The intention is to produce a demonstrator engine that will use advanced pressure charging techniques together with an advanced combustion system to realise a downsized engine concept that returns diesel-like fuel economy with gasoline levels of engine refinement. In addition to any design work, GEPE will manufacture the prototype connecting rods, pistons, cylinder head and inlet system components.
GEPE’s production technology sees the company retain a considerable customer base in the motorsport industry, with GEPE manufacturing small batches, prototypes and chassis work for F1 teams with larger production runs for Norton motorcycles running alongside the prototype work. As Mr Edwards states: “We would be incapable of meeting the short turnaround demands of our customers if we didn’t have hyperMILL. From the moment I went to an OPEN MIND demo day, I knew it was the only package for our company. We also do a lot of prove-outs and fixturing for one F1 team that uses hyperMILL, so it made sense to have the same package.”
The first seat arrived in April 2009 with additional seats following in June 2009 and September 2010. The quality of components immediately improved, with Mr Bredda continuing: “We have machined parts with hyperMILL and we have seen some customers’ machine the exact same parts with alternate CAM packages, there is no comparison in quality. The toolpaths of hyperMILL drastically improves the surface finishes and overall component quality whilst the programming times are significantly reduced.”
An opinion mirrored by shop floor machinist, Mr Stuart Palmer: “hyperMILL is a million times easier to use than the previous package. It has an extremely intelligent and user friendly interface that gives the user the maximum output with the minimum input, making complex 5-axis jobs simplistic to program.”
Mr Edwards echoes this sentiment: “Programming times have fallen by anything from 30 to 60% and when our average programming time is approximately 16 hours, it shows how invaluable hyperMILL is to us. As an employer, I am also very confident that staff can be trained to be very competent with a short training period.”
“I recall our first job with hyperMILL, an F1 wing from a solid billet. It was like programming a part with a package I have been using for years. This is down to the benefits of a package that are almost too many to mention.”
“The optimisation of tool paths and rough machining cycles ensure ‘fresh air’ cutting is minimised and this has contributed to cycle time reductions of beyond 20%. hyperMILL also has astounding computation times, this allows you to work on the next cycle whilst the previous cycle is being calculated, a time saving benefit not available with most packages.”
Continuing his praise of the hyperMILL cycles, Mr Edwards states: “hyperMILL offers complete finishing cycles for all surfaces whereas other packages have a cycle for horizontal machining and another for vertical machining, prolonging the programming times. hyperMILL also offers shorter program lengths with less code by condensing outputs, such as incorporating radii into G2 & G3 codes.”
The company has two seats in its design office with the third on the shopfloor. This allows the shopfloor staff to program smaller jobs that require 3-4 hours of programming, removing bottlenecks. As Mr Edwards states: “We have some extremely high end machine tools on our shop floor and the collision avoidance of hyperMILL is second to none. This gives me, as an employer and the machinists, complete confidence in turning jobs around rapidly and 100% correctly with no collisions and impeccable quality.”
“As well as prototype work, we now have a production cell machining 40 sets of Norton crankcases and cylinder heads per week. With its port machining strategy, hyperMILL makes port and exhaust machining simplistic. It requires less effort to resolve tool paths, improves cycle times and makes the prove-out process faster – reducing the burden on our production engineering department. With my extensive CAM experience, my opinion is that OPEN MIND is the only feasible option for any business conducting complex 5-axis machining.”