Global Packaging Manufacturer Cuts Bottleneck with DYSS Cutting Table
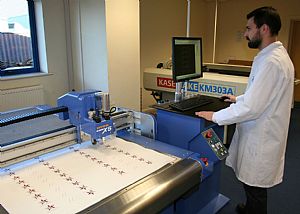
When Blackburn Corrugated Paper (BCP) Fluted Packaging Ltd was taken over by the Huhtamaki Group in December 2013, an acquisition by one of the world's largest packaging companies, nobody could have envisaged the rapid rate of growth and innovation that would follow.
Now named Huhtamaki BCP Ltd, the 157 employee, North West based company is a leading manufacturer of packaging liners, bake trays, microwave susceptor food packaging, paper cup sleeves, food-to-go and confectionary packaging. Regarded as a market leading supplier to the food, confectionary, cosmetic and gift packaging industries, the upsurge in new work at Huhtamaki BCP was creating bottlenecks for the product design department - until it installed a DYSS X5-1316T cutting table from AG/CAD.
As Huhtamaki BCP's Design Manager, Mr Keith Glover takes up the story: "Since the company acquisition, this facility has grown by over 10%. What this means for the design team is that our production of prototypes and samples has increased from approximately 12,000 a year to upward of 20,000 samples a year. The quantity of sample batches and design variations will vary from day to day, but what we found was our 15 year old cutting table wasn't fast enough to cope with the increased workload. For example, we recently had a job that required 35 different design variations with a turnaround of just over a week. Without the new DYSS machine, our old machine wouldn't have been able to fulfil the order."
The volume of enquiries created by an extremely pro-active sales team filtering sample requests through to a team of four designers with access to just one cutting table - a 15 year old KASEMAKE KM303A cutting table - had pushed back lead-times and affected the ability to respond quickly to customers. Whilst the design team were able to originate designs to the short lead-time demands of the sales team, the ageing cutting table couldn't cope with the capacity increase. To support the production of samples in quantities from 1 or 2 up to 500, Huhtamaki BCP was externally sourcing 2-3 die cutting formes a week for platen cutting its prototype/development work. Whilst complementing the ageing cutting table, this strategy was particularly expensive. Additionally, cutting forme design and production would give Huhtamaki an average sample lead-time of up to 5 days - this is now down to less than 48 hours following installation of the DYSS X5.
With an existing supplier relationship based on the 15 year old machine and four seats of KASEMAKE software already on-site, AG/CAD Limited was the natural first port of call for a new machine, but Huhtamaki did their due diligence and researched the alternatives thoroughly. As Mr Glover continues: "Despite being an old table, the KM303A is still extremely reliable and consistent and is well supported by AG/CAD. We knew that if we bought another AG/CAD machine, we would continue to enjoy a good level of service. What was most important for us was the support with the KASEMAKE software. With four designers, we are constantly using KASEMAKE and if we require tweaks to the software and programming to simplify our jobs, AG/CAD's software developers will oblige our requests. No other company could offer that level of service or support."
The Deciding Factor
If the level of existing machine and software support wasn't enough to swing the procurement decision for Huhtamaki, the capability of the high frequency cutting head and the knife blades on the DYSS X5 sealed the deal. As part of its pursuit for a suitable cutting table, Huhtamaki tested the various cutting machine vendors with lightweight glassine papers that it frequently manufactures to protect chocolates in confectionary boxes for high street retailers. With a high frequency oscillating knife and in particular the unique cutting knife geometries capable of delivering high quality edges without tearing the difficult to process paper, even at high speeds, AG/CAD was the only supplier to succeed with this trial.
Cutting The Costs
Like any global organisation, Huhtamaki fully assessed the cost implications of purchasing new plant, and its assumptions on the cost and lead-time reductions the X5 has brought in the two months since installing the DYSS X5 have been realised.
In addition to removing forme costs & reducing lead-times, the DYSS has cut the cost of producing 'print traces' at Huhtamaki. Print traces are tracing films showing the exact location of the cuts and creases for a multi-up design. These are then overlaid onto the printed sheets to verify perfect alignment when the printed job is later cut on Huhtamaki’s die presses. Previously having 2-3 print traces externally manufactured each week, the design team now inputs the design into the KASEMAKE software, purchases its own tracing media and plots out the layouts on the DYSS machine, saving considerable costs.
Time Savings
Time and cost pressure can be an overwhelming factor in a global marketplace, but the DYSS X5 has undoubtedly relieved the burden for Huhtamaki BCP. As Mr Glover concludes “For our sales team, they can now deliver samples to existing and potential customers in less than 48 hours instead of the average 5 day turnaround time we had prior to the arrival of the DYSS. For the design team, having a second cutting table that is almost 10 times faster than its predecessor is what allows us to meet the lead-time demands of the sales team. This relieves pressure for both departments. By having a second machine, we also have process reliability in case one machine requires servicing or scheduled downtime. The DYSS X5 has been a great investment for us."