hyperMILL CAM Software Keeps Wheels Turning For Birmingham Subcontractor
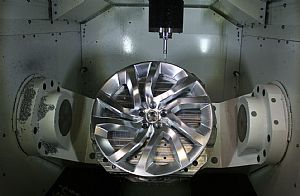
Specialising in the production of prototype components and complex small batch runs for the automotive sector, Birmingham based Advanced Engineering (UK) Ltd has always maintained its ethos of investment in technology to deliver component quality at lead times beyond the capabilities of its competitors. This philosophy has resulted in the company investing over £2.75m in under seven years.
The investment has seen Advanced Engineering evolve with technology to move from 3+2 axis machining into full simultaneous 5-axis machining seven years ago. Since 2006, the company has purchased five simultaneous 5-axis machines with more recent acquisitions including Mazak Hyper Variaxis 630 and Mazak 630-5X machining centres. With two seats of CAM software from two different, local and leading vendors, Advanced Engineering's Managing Director, Mr Terry Pedley was intent on driving through software changes to maximise the capabilities of the new machine tools.
Extensive investigation that involved visits and consequent recommendations from F1 engine manufacturers and other prestigious names in the automotive and motorsport sectors, resulted in the TS:16949, AS:9100 and ISO:9001 accredited company acquiring three seats of OPEN MIND's hyperMILL CAM software just over 12 months ago.
The Engineering Manager at Advanced Engineering, Mr David Richardson takes up the story: "Our MD didn't believe our existing software was up to the job and to improve our quality, he investigated and invested in hyperMILL as he wanted the 'best available' software. With two Engineers in the office with extensive experience on various CAM packages, we have witnessed the multitude of benefits of implementing hyperMILL and can confirm the MD definitely made the right choice."
As a company that produces components for marquee names in the global Automotive sector, 30 employee Advanced Engineering is well versed in producing anything from prototypes to batches up to 100 with remarkable complexity and even more remarkable lead times. Producing anything from CAM covers, cylinder blocks, control arms, pump housings, decorative door linings and prototype wheels for global automotive exhibitions, turnaround time is critical for Advanced Engineering.
Commenting upon how hyperMILL has improved overall turnaround times for the Birmingham company, CAM Programmer Mr Mick Mann comments: "To quantify the benefits of hyperMILL over other leading packages we have; cycle times on the shop floor have been reduced by over 40%. This is credit to vastly improved toolpaths that cut machining time. Additionally, the OPEN MIND tool paths have significantly improved surface finishes. This has eliminated secondary hand finishing and fettling of parts like exhibition wheels and door linings that have to be aesthetically impeccable."
"From a programming standpoint, hyperMILL has cut programming times by at least 70% and in the case of jobs that have left and right hand parts, the mirroring function on hyperMILL cuts times by over 90%. I've used a number of CAM packages and each has its benefits. However, hyperMILL is far superior in all aspects. We do a lot of 3D 5-axis machining and hyperMILL is perfect for this, whereas our other packages do not adapt well to complex designs. For example, the post-processors on alternate packages are out-dated and do not adapt well to our complex geometries and tool paths on new machine tools whereas hyperMILL is user friendly and easy to get from drawing to shop-floor cutting."
The programming team at Advanced Engineering are in agreement that hyperMILL has improved productivity in the office as well as on the shop-floor. As Mr Mann continues: "hyperMILL is very user friendly, intuitive and has features that are far easier to use than alternate packages. The crash testing and tool collision is far beyond previous packages with tool data banks capable of clarifying the path of the tool and even the toolholders inside cavities to give full crash detection. It has been so intuitive and user friendly, we haven't had to make a call for support in over 15 months."
Highlighting the ability of hyperMILL to reduce programming times, Mr Mann spends 90% of his time programming parts that require mirroring. On complex automotive door parts the programming time can be up to 40 hours. To program the 'opposite hand' component; instead of taking an additional week to program the opposite part, the mirroring function on hyperMILL will automatically calculate the part in a an hour or two. This instantly reduces programming times by beyond 90%. In the instance of less complex parts that require 3-4 hours of programming, hyperMILL calculates the opposite hand part in a matter of minutes. Comparing seats of alternate CAM packages at Advanced Engineering with hyperMILL; the Birmingham based CAM vendor offers no such mirroring option whilst another package will still take 2-3 days to mirror a part that initially requires one week of programming input.
With a large percentage of production at Advanced Engineering being prototype production, hyperMILL has time and again been proven to drastically cut cycle times. For example, A wheel that is turned and then 5-axis milled from an aluminium blank would take 20 hours to produce on a Mazak machining centre that is programmed with previous CAM packages. With hyperMILL this time has been cut to less than 12 hours, a 40% improvement. Added to this, the improved tool paths with hyperMILL eliminate secondary fettling and hand finishing that would be necessary with previous CAM packages. With improved quality, productivity and the elimination of hand finishing on a job that is manufactured up to 100 times a year, the savings have been exceptional.